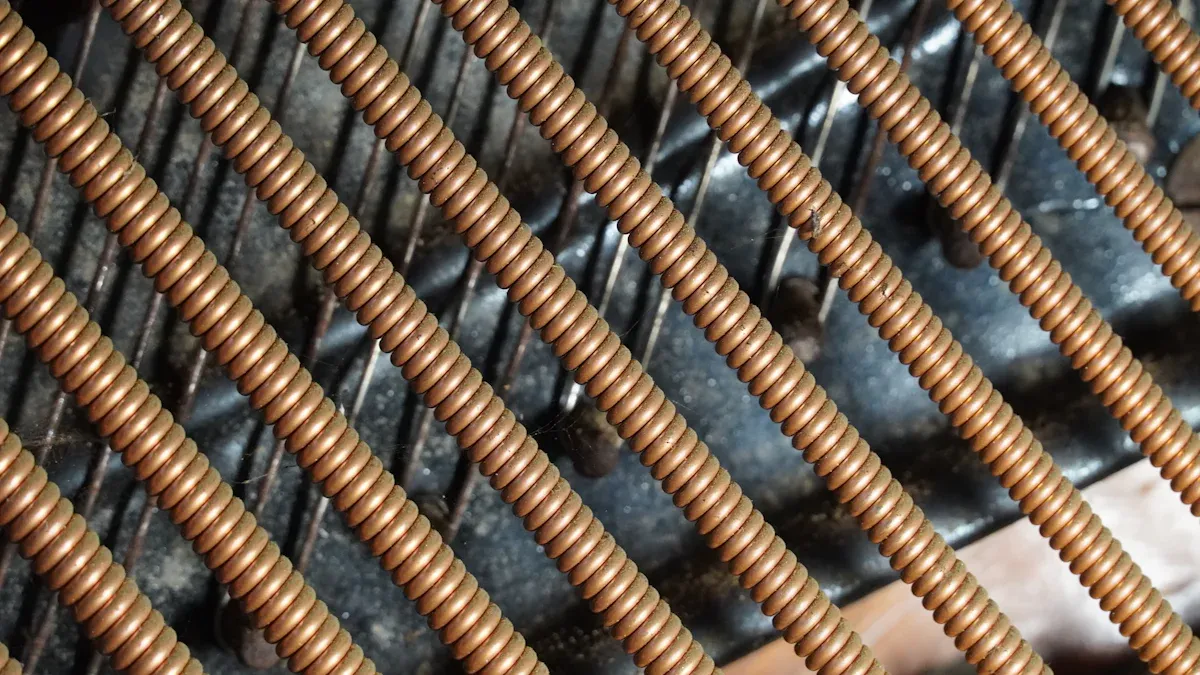
You achieve optimal results in your 2025 application by selecting a heating coil that matches your exact requirements. The right choice depends on critical factors like coil material, size, shape, and the operating environment. With the global heating coil market projected to reach $4.1 billion by 2032, more industries demand energy-efficient solutions. You should focus on factors such as durability, performance metrics, and protective sheaths. Matching coils to your needs ensures efficiency, safety, and long service life.
Key Selection Criteria for Heating Coil Applications
Application Requirements for Heating Elements
Temperatura
You must define the operating temperature for your application before selecting heating elements. The required temperature range determines the type of electric heating coil elements you need. For example, polyimide heaters perform well at high temperatures, while silicone rubber options offer moisture resistance. If your process involves rapid temperature changes, choose heating elements that can withstand thermal cycling without degrading. Always match the coil’s maximum temperature rating to your system’s needs to avoid premature failure.
Heating Load and Capacity
Accurately calculating the heating load ensures you select heating elements that deliver the right amount of heat. Consider voltage, wattage, and watt density, as these factors drive the design and performance of electric heating coils. Manufacturers adjust element thickness and spacing to meet your heat output requirements. For applications with multi-zone heating, you can use multiple input power lines or a single temperature controller to manage different areas efficiently.
Environmental Conditions
Environmental factors such as air velocity, humidity, chemical exposure, and mechanical stress directly impact the performance and longevity of heating elements. Protective coatings or ruggedized materials help resist corrosion and physical damage. When space is limited, thinner elements with tighter spacing allow for uniform heat distribution in compact or moving parts. Always consider the installation environment to ensure reliable operation.
Performance Considerations for Electric Heating Coils
Efficiency
Energy efficiency remains a top priority for electric heating coils in 2025. Performance benchmarks like the Coefficient of Performance (COP) and Energy Efficiency Ratio (EER) help you compare systems by measuring heat output relative to energy consumption. Even though most electric heating coil elements convert nearly all electrical power into heat, the way heat distributes within your space affects overall energy efficiency. Systems with better heat distribution consume less energy while maintaining comfort.
Response Time
Fast response time allows you to reach the desired operating temperature quickly. Etched foil heating elements, for example, provide precise heat control and rapid thermal response, making them ideal for applications that demand quick adjustments. Shorter response times improve process control and reduce energy waste.
Control and Modulation
Advanced control and modulation features let you fine-tune heat output for optimal energy efficiency. Integrate temperature sensors like thermocouples or RTDs for real-time monitoring. Multi-zone heating and variable power input help you maintain consistent temperatures and prevent overheating.
Safety and Compliance in Choosing the Right Heating Element
Regulatory Standards for 2025
You must comply with industry standards and certifications to ensure safety and performance. Key standards include:
- ASME Boiler and Pressure Vessel Code
- UL 207 and ANSI/ASHRAE safety codes
- Canadian Registration Number (CRN)
- CSA certification (STD C22.2)
- European Pressure Equipment Directive (PED)
- AHRI Standard 410
- ETL certification (ANSI/UL 1995, CAN/CSA C22.2 No 236-05)
- ISO 9001:2015 for quality management
These standards define design, safety, and regulatory requirements for heating elements worldwide.
Overheat Protection
Overheating poses significant risks to both equipment and personnel. Integrate thermal cut-offs, fuses, and redundant sensors to prevent unsafe temperature rises. Regular calibration and correct placement of temperature sensors help maintain safe operation.
Electrical and Fire Safety
You must prioritize electrical safety by ensuring proper grounding, secure wiring, and regular inspections. Use corrosion-resistant materials and protective coatings to prevent leaks and structural failures. Operator training and adherence to manufacturer guidelines further reduce the risk of fire or electrical hazards.
Consejo: Regular inspections and preventative maintenance help you avoid common failures such as corrosion, leakage, and sensor malfunctions, ensuring safe and reliable operation of your heating elements.
Longevity and Maintenance Selection Tips
Durability
You want your heating coil to last as long as possible, especially in demanding environments. Durability depends on the material, construction quality, and how well the coil resists corrosion, oxidation, and thermal fatigue. Stainless steel and Incoloy alloys offer excellent resistance to high temperatures and corrosive atmospheres. If you operate in a harsh setting, select a coil with a protective sheath or coating. This extra layer shields the element from moisture, chemicals, and physical impact.
Consejo: Always check the manufacturer’s recommended operating limits. Exceeding these limits can shorten the coil’s lifespan and lead to unexpected failures.
Serviceability
Easy maintenance saves you time and reduces downtime. When you choose a heating coil, look for features that simplify inspection, cleaning, and replacement. Modular designs allow you to swap out faulty elements without dismantling the entire system. Quick-connect terminals and accessible mounting points make routine service much easier.
A simple maintenance checklist can help you keep your heating coil in top condition:
- Inspect for signs of wear, corrosion, or discoloration.
- Clean dust and debris from the coil surface.
- Test electrical connections for tightness and integrity.
- Replace damaged insulation or protective sheaths.
Maintenance Task | Frequency | Benefit |
---|---|---|
Visual Inspection | Monthly | Early issue detection |
Cleaning | Quarterly | Evita el sobrecalentamiento |
Electrical Testing | Annually | Ensures safe operation |
Warranty and Support
Reliable warranty coverage and technical support give you peace of mind. Before you finalize your purchase, review the warranty terms. Look for coverage that includes both parts and labor. Some manufacturers offer extended warranties for critical applications. Responsive technical support helps you resolve issues quickly and minimizes downtime.
Nota: Keep all documentation, including installation guides and warranty certificates, in a safe place. This makes it easier to access support or file a claim if needed.
When you follow these selection tips, you ensure your heating coil delivers long-term performance with minimal maintenance. Prioritizing durability, serviceability, and strong support will help you maximize your investment and avoid costly disruptions.
Understanding Heating Coil Types and Selection Tips
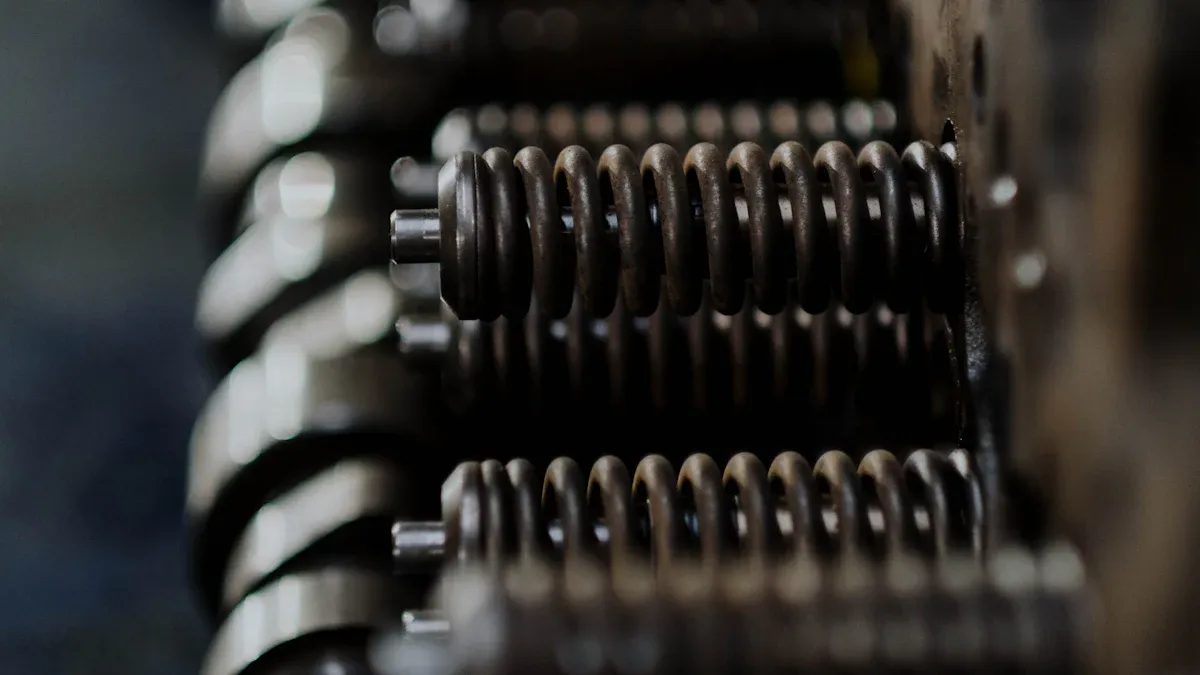
Tubular Heating Coils
Pros and Cons
You benefit from tubular heating coils when you need robust performance and adaptability. These coils use a metal sheath to protect the internal electrical resistance wire heating element, which increases durability and safety. You can rely on empirical models, such as the ε-NTU method, to predict their thermal capacity and effectiveness across a wide range of conditions. Tubular coils adapt well to different environments and system requirements.
- You gain consistent heating capacity, even in complex HVAC configurations.
- These coils handle variable flow rates, glycol concentrations, and different altitudes.
- You can use simplified models for sizing without needing detailed geometric data.
- Tubular coils perform well in both dry heating and cooling modes.
- They integrate easily with simulation tools for dynamic performance evaluation.
However, you may find that tubular coils require more installation space than some alternatives. Their metal sheath can limit maximum operating temperature compared to open coil designs.
Typical Applications
You often see tubular heating coils in HVAC systems, including air handling units, fan coil units, and split systems. They excel in applications where you need precise temperature and humidity control. You also find them in dedicated outdoor air systems, desiccant wheel systems, and heat recovery devices. Their versatility makes them suitable for both partial load and specialized applications, such as chilled beams.
Finned Heating Coils
Pros and Cons
Finned heating coils offer you enhanced heat transfer due to the increased surface area provided by the fins. The global market for these coils continues to grow, driven by demand in HVAC, power generation, and automotive industries. You benefit from their strong corrosion and oxidation resistance, especially when constructed from stainless steel. Finned coils are durable, easy to maintain, and meet strict safety standards.
- You can use them in wet or hazardous environments, as they resist moisture-related short circuits.
- Finned coils protect against dirt, dust, and lint, reducing the risk of electrical shorts.
- You can replace elements easily from the terminal box, improving serviceability.
- Their rugged design withstands high-vibration settings, such as nuclear power plants.
- You achieve precise temperature control due to greater thermal inertia.
You should note that finned coils have a higher pressure drop than open coil types. However, they avoid the need for additional pressure plates, which can further increase pressure drop in open coil systems.
Typical Applications
You use finned heating coils in environments where you need efficient thermal management and durability. They are common in HVAC duct heaters, industrial process heating, and renewable energy systems. Their resistance to moisture and foreign matter makes them ideal for challenging settings, including food processing and chemical plants.
Open Coil Heating Elements
Pros and Cons
Open coil heating elements provide you with a cost-effective solution for high-temperature applications. You benefit from their simple design and quick thermal response. The table below compares open coil elements with finned tubular elements:
Aspecto | Open Coil Heating Elements | Finned Tubular Elements |
---|---|---|
Cost | More economical construction due to simpler design and lower weight | More expensive due to accommodating higher watt densities |
Maximum Operating Temperature | Up to 1200°F, suitable for higher temperature applications | Recommended up to 600°F |
Pressure Drop | Lower pressure drop because of less space occupied by elements | Higher pressure drop due to element design |
Thermal Response | Quick response due to low thermal inertia | Slower response but more uniform temperature control |
Coil Temperature | Runs cooler when exposed directly to air stream | Runs hotter due to sheath and fin design |
Airflow Requirements | Requires uniform airflow to avoid hot spots | More tolerant of non-uniform airflow |
Safety Considerations | Less suitable where accidental contact is possible due to lack of sheath | Safer due to metal sheath |
You must ensure uniform airflow to prevent hot spots and overheating. Open coil elements lack a protective sheath, so you should avoid them in areas where accidental contact is possible.
Typical Applications
You select open coil heating elements for applications that require rapid heating and high temperatures, such as industrial ovens, dryers, and process air heaters. Their low cost and fast response make them attractive for large-scale heating where safety enclosures are present.
Cartridge Electric Heating Coils
Pros and Cons
You gain precise and reliable heating with cartridge electric heating coils. These coils fit tightly into drilled holes, delivering high watt density directly to the target area. You can expect long service life, especially in critical applications. Miniature pencil heaters, for example, often last between 50,000 and 90,000 hours. Advanced split-sheath designs help you reduce process heating costs by up to 40% compared to conventional heaters. Modern cartridge heaters, such as NPH eheat models, improve energy efficiency by as much as 25%. Stainless Steel 321 sheaths resist corrosion and simplify removal, while longer ceramic cores mean fewer electrical connections and greater durability.
Performance Aspect | Description / Metric |
---|---|
Heater Life | 50,000–90,000 hours in critical applications |
Cost Savings | Up to 40% reduction in process heating costs |
Energy Efficiency | Up to 25% improvement over traditional cartridge heaters |
Material Quality | Stainless Steel 321 sheath for corrosion resistance |
Construction Quality | Longer ceramic cores for fewer connections and improved durability |
Manufacturing Precision | Tight tolerances and optimal wattage distribution |
Engineering Services | Thermal consulting and design optimization available |
However, you may face challenges with heat removal in poorly ventilated setups. Cartridge coils require precise fit and installation to avoid hot spots or premature failure.
Typical Applications
You use cartridge electric heating coils in plastic injection molds, packaging equipment, hot stamping, and medical devices. These coils excel in applications demanding localized, high-intensity heat and tight temperature control. You also find them in food processing, die casting, and scientific instruments.
Flexible Heating Elements
Pros and Cons
Flexible heating elements give you unmatched adaptability. You can shape them to fit curved or irregular surfaces, which is essential when rigid heaters cannot perform. These elements remain thin, lightweight, and energy efficient. You benefit from uniform heat distribution and rapid response times. Advanced materials, such as silicone rubber, polyimide, and carbon-based elements, enhance durability and customization. Printed heating technologies and graphene-based heaters further expand your options for miniaturized products.
- Flexible heaters conform to complex shapes and surfaces.
- You achieve seamless integration in compact devices.
- They operate reliably in extreme conditions, such as aerospace de-icing or electric vehicle battery heating.
- Market growth remains strong in automotive, medical, and industrial automation sectors.
You should note that flexible heaters may have lower maximum temperature limits than rigid coils. They also require careful installation to avoid damage or performance loss.
Typical Applications
You find flexible heating elements in automotive seat and battery heaters, medical diagnostic devices, wearable electronics, and aerospace systems. They also serve in semiconductor manufacturing and smart building applications. The ribbon heating element, a type of flexible heater, provides uniform heat in compact spaces and supports rapid thermal cycling.
Induction Heating Coils
Pros and Cons
Induction heating coils offer you rapid, contactless heating with precise temperature control. You benefit from high energy efficiency, as these coils heat only the targeted component. You can automate processes and improve manufacturing quality. However, you must optimize coil design, frequency, and positioning to achieve uniform heating. Improper settings can cause temperature heterogeneity due to the skin effect, especially in complex shapes.
Aspecto | Operational Benefits | Constraints and Challenges |
---|---|---|
Temperature Control | Precise, consistent heat treatment | Uniform heating difficult for complex shapes |
Heating Speed | Rapid heating, increased productivity | Limited to conductive materials |
Energy Efficiency | Reduced energy waste and operating costs | Higher initial system costs |
Component Durability | Improved hardness and wear resistance | Requires advanced control and monitoring |
Manufacturing Quality | Consistent product performance | Coil design critical for process quality |
Typical Applications
You use induction heating coils in metal hardening, forging, and brazing. These coils play a key role in firearm barrel manufacturing, ammunition production, and energy generation. You also see them in automotive part fabrication and high-precision industrial processes.
Comparing Heating Coil Materials and Designs
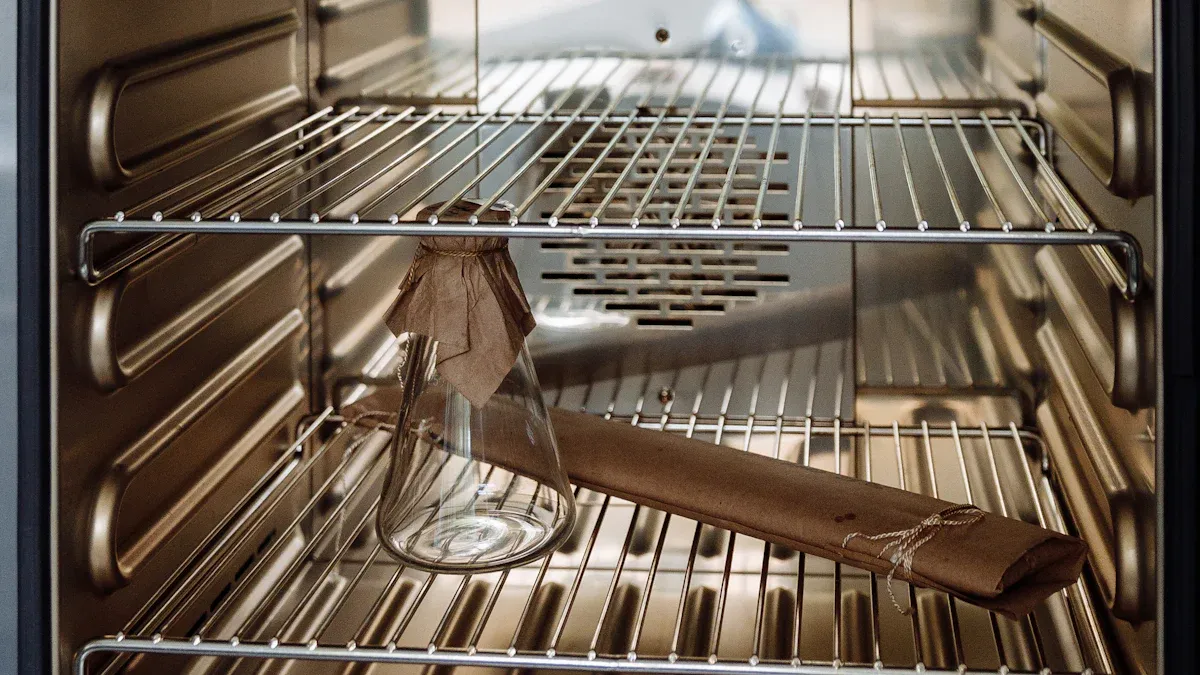
Common Heating Coil Materials
Stainless Steel
You often choose stainless steel for heating coil materials when you need strong corrosion resistance and durability. Stainless steel, especially grades 304 and 316, forms a passive oxide layer due to its chromium content. This property makes it suitable for industrial, marine, and pharmaceutical environments. However, stainless steel has moderate thermal conductivity, so it may not transfer heat as efficiently as other options. You benefit from its high mechanical strength and low maintenance, which supports long-term use in high-temperature operations.
Copper
Copper and copper-nickel alloys provide excellent thermal conductivity, making them ideal for heat exchangers and systems where rapid heat transfer is critical. You find copper especially useful in marine environments because it resists pitting and stress corrosion. Copper’s ductility and formability allow you to create complex coil shapes, which improves heating element design flexibility. While copper offers lower initial costs, you must consider its suitability for high-temperature applications and ensure material compatibility with your process fluids.
Incoloy and Other Alloys
You select Incoloy and specialized alloys like AL-6XN® or Hastelloy® for the most demanding high-temperature operations. These materials deliver superior resistance to oxidation and corrosion, even in aggressive chemical environments. Incoloy’s mechanical strength and stability at elevated temperatures make it a top choice for high temperature applications and corrosive atmospheres. When you require maximum material compatibility and long service life, these alloys provide reliable performance.
Consejo: Use the table below to compare key properties of common heating coil materials:
Property | Stainless Steel (304, 316, 403) | Copper-Nickel Alloys (70/30, 90/10) |
---|---|---|
Corrosion Resistance | High; forms passive oxide layer | Excellent; forms protective oxide layer |
Mechanical Strength | High tensile strength, good hardness | Good ductility, enhanced with alloying elements |
Thermal Conductivity | Moderate (8.1–15.1 Btu/(ft·hr·°F)) | Higher (29–40 W/m·K) |
Application Suitability | Industrial, food, marine, pharmaceutical | Marine, heat exchangers, cooling systems |
Cost and Maintenance | Higher cost, low maintenance | Lower cost, minimal maintenance |
Material Selection Tips by Application
Corrosive Environments
You must prioritize material compatibility when operating in corrosive environments. Field studies using online corrosion monitoring sensors show that real-time data helps you understand how operational changes affect corrosion rates. You can use gravimetric analysis and SEM-EDX deposit analysis to assess material degradation and select the best heating coil materials. Thermal spray coatings and solid lubricants further enhance corrosion and oxidation resistance, especially in high-temperature operations.
High-Temperature Applications
For high-temperature operations, you need materials that maintain integrity and resist oxidation. Stainless steel and Incoloy alloys perform well under these conditions. You can improve coil longevity by applying advanced coatings and heat treatments. Always match the material compatibility to the specific temperature and chemical exposure in your process.
Food and Medical Applications
You require strict material compatibility in food and medical applications. Stainless steel remains the preferred choice due to its hygienic properties and resistance to contamination. You should select heating coil materials that meet regulatory standards and withstand frequent cleaning cycles without degrading.
Design Considerations for Electric Heating Coils
Coil Shape and Configuration
You influence heating element design performance by selecting the right coil shape, diameter, and pitch. Engineering reports show that coil geometry affects heat dissipation, surface area loading, and durability. You can optimize surface area loading by adjusting coil stretch and wire diameter, which improves efficiency in high-temperature operations.
Mounting and Integration
You must support coils with proper insulators to prevent sagging and manage thermal expansion. Good mounting practices reduce hot spots and extend coil life. You should also consider airflow and shielding to balance surface area loading and avoid overheating.
Custom vs. Standard Designs
You decide between custom and standard heating element design based on your application’s complexity. Custom designs allow you to tailor coil shape, surface area loading, and material compatibility for unique requirements. Standard designs offer faster lead times and proven performance for common high-temperature operations.
Step-by-Step Guide to Choosing the Right Heating Element
Define Your Application Parameters
Gather Key Data
You start by collecting all essential information about your application. This step ensures you select heating elements that deliver reliable performance and long service life. Follow these steps:
- Identify the type of heat transfer you need—conduction, convection, or radiation.
- Calculate the required power and heat flux. Use the formula:
Power (W) = Mass × Specific Heat Capacity × Temperature Change / Time
- Determine the size or mass of the heating element. Balance heating speed with temperature stability.
- Decide if your application needs a rigid or flexible heater. Consider the shape and stability of the area to be heated.
- Evaluate the operating environment. Check for humidity, corrosive gases, or contaminants.
- Choose an installation method that matches the heater type and allows for easy replacement.
- Assess the total cost of ownership. Include initial purchase, operating costs, and expected lifetime.
Tip: Matching the heating element temperature range to your application prevents premature failure and ensures durability.
Identify Constraints
You must recognize any limitations that could affect your choice. These constraints help you avoid costly mistakes and ensure the heating elements fit your system.
- Space limitations: Measure available space for installation.
- Power supply: Confirm voltage and current availability.
- Environmental factors: Note exposure to chemicals, moisture, or dust.
- Safety requirements: Identify any regulatory or industry standards you must meet.
- Maintenance access: Ensure you can inspect and replace the heating element easily.
Note: Proper installation and routine maintenance help you detect wear or damage early, preserving performance and extending lifespan.
Match Heating Coil Type and Material to Needs
Use Case Scenarios
You improve your selection process by reviewing common scenarios:
- For high-temperature industrial ovens, choose resistance wire or ceramic heating elements that withstand extreme heat.
- In food processing, select stainless steel or metal-sheathed elements for hygiene and corrosion resistance.
- For laboratory testing, use flexible or custom-shaped elements to fit specialized equipment.
- In automotive or aerospace, advanced materials like molybdenum disilicide or silicon carbide handle harsh environments and rapid cycling.
You must always match the heating element to the required temperature range and operational environment. This approach prevents chemical degradation and maintains efficiency.
Decision Points
You face several key decisions when choosing the right heating element:
- Does your application require rapid heat-up or precise temperature control?
- Will the element operate in a corrosive or humid environment?
- Do you need a standard or custom design?
- What is your priority—energy efficiency, durability, or cost-effectiveness?
Decision Point | Consideration | Example Solution |
---|---|---|
Temperatura | Maximum and minimum operating temperature | Nichrome for up to 1200°C |
Material Compatibility | Exposure to chemicals or moisture | Silicon carbide for oxidizing |
Energy Efficiency | Reduce operational costs | High-resistivity materials |
Durability and Longevity | Minimize downtime and replacements | Metal-sheathed or ceramic |
Installation and Maintenance | Ease of access and replacement | Modular or quick-connect design |
Callout: Awareness of specialized heating element types and advanced materials helps you align with market trends and meet unique application needs.
Evaluate Performance and Safety of Heating Elements
Testing and Certification
You ensure safety and reliability by verifying that your heating elements meet recognized standards. Leading organizations like CSA Group and UL Solutions conduct rigorous testing and certification. These tests include:
- Functional safety evaluations
- Compliance with IEC 60730 and UL 2417 standards
- Product performance and environmental simulation testing
- Energy efficiency verification
- Autoignition temperature and dielectric breakdown voltage testing
These certifications validate that your heating elements perform safely under demanding conditions and meet industry requirements for sanitation, efficiency, and reliability.
Safety Features Checklist
You protect your equipment and personnel by confirming the presence of essential safety features. Use this checklist:
- Overheat protection (thermal cut-offs or fuses)
- Proper grounding and secure electrical connections
- Corrosion-resistant materials and protective coatings
- Redundant temperature sensors for critical applications
- Compliance with all relevant regulatory standards
Tip: Regular inspections and adherence to manufacturer guidelines reduce the risk of fire, electrical hazards, and unexpected downtime.
Consult with Manufacturers or Experts for Selection Tips
When to Seek Professional Advice
You should recognize the value of expert input during the heating coil selection process. Manufacturers and industry specialists possess deep technical knowledge and experience with a wide range of applications. Their guidance helps you avoid costly mistakes and ensures your system meets all performance and safety requirements.
Consider reaching out to professionals in these situations:
- Complex or Custom Applications: If your project involves unique temperature profiles, non-standard voltages, or custom geometries, you benefit from expert design support.
- Stringent Regulatory Compliance: When your application must meet specific industry standards or certifications, experts help you interpret and implement these requirements correctly.
- Challenging Environments: If you face harsh conditions such as corrosive atmospheres, high humidity, or extreme temperatures, specialists recommend suitable materials and protective features.
- Integration with Advanced Controls: For systems that require precise modulation, multi-zone heating, or integration with smart controls, you gain from consulting engineers who understand the latest technologies.
- Uncertain Performance Requirements: If you lack clarity on heating load calculations, response times, or efficiency targets, professionals assist with accurate sizing and selection.
Consejo: Early consultation with manufacturers or technical experts streamlines your project timeline and reduces the risk of design revisions later.
Questions to Ask Suppliers
You strengthen your decision-making by asking targeted questions when engaging with heating coil suppliers. Clear communication ensures you receive products that align with your technical and operational needs.
Consider using this checklist when speaking with suppliers:
- What coil type and material do you recommend for my application?
- Ask for justification based on your operating environment and temperature range.
- Can you provide performance data or test results for your heating elements?
- Request documentation such as efficiency ratings, response times, and durability metrics.
- What certifications and standards do your products meet?
- Confirm compliance with relevant safety and quality standards for your industry.
- How do you support installation and maintenance?
- Inquire about available guides, training, or on-site support.
- What warranty terms and after-sales support do you offer?
- Clarify coverage for parts, labor, and technical assistance.
- Can you customize coil designs for my specific requirements?
- Determine the feasibility, lead time, and cost implications of custom solutions.
- How do you handle quality control and product traceability?
- Ask about manufacturing processes, inspection protocols, and batch tracking.
Nota: Document all supplier responses and compare them using a simple table. This approach helps you evaluate options objectively.
Question | Supplier A Response | Supplier B Response | Supplier C Response |
---|---|---|---|
Coil Type & Material Recommendation | |||
Performance Data Provided | |||
Certifications & Standards | |||
Installation & Maintenance Support | |||
Warranty & After-Sales Support | |||
Opciones de personalización | |||
Quality Control & Traceability |
You ensure a successful heating coil selection by engaging with experts and asking the right questions. This process leads to better performance, safety, and long-term value for your application.
Practical Heating Coil Selection Checklist and Decision Matrix
Quick-Reference Selection Checklist
Essential Criteria
You need a clear checklist to streamline your heating coil selection process. Focus on these essential criteria to ensure your system delivers reliable performance and safety:
- Define the required temperature range for your application.
- Calculate heating load and ensure proper surface area loading for efficient heat transfer.
- Confirm material compatibility with process fluids, environmental conditions, and cleaning agents.
- Assess the installation environment for factors like humidity, airflow, and exposure to chemicals.
- Verify compliance with industry standards and safety regulations.
- Evaluate surface area loading to prevent hot spots and ensure uniform heating.
- Check for robust overheat protection and electrical safety features.
Tip: Prioritize criteria based on your operational goals and stakeholder input. Decision-making frameworks like the Analytic Hierarchy Process (AHP) help you weigh each factor according to its importance.
Optional Features
Once you address the essentials, consider optional features that can enhance performance or simplify maintenance:
- Advanced control systems for precise modulation and multi-zone heating.
- Modular or quick-connect designs for easier serviceability.
- Enhanced surface area loading through custom coil shapes or finned designs.
- Smart sensors for real-time monitoring and predictive maintenance.
- Extended warranties and responsive technical support.
A structured approach, such as the House of Quality (QFD), helps you link these features to your specific needs and rank them for optimal selection.
Heating Coil Decision Matrix for Applications
Application vs. Coil Type
You can use a decision matrix to compare coil types against your application requirements. This method allows you to score and rank options based on technical, economic, and contextual factors. Tools like scoring sheets, value tables, and color heat maps help you visualize trade-offs and identify the best fit.
Application | Tubular Coil | Finned Coil | Open Coil | Cartridge Coil | Flexible Element | Induction Coil |
---|---|---|---|---|---|---|
High Temp Industrial Oven | ✓ | ✓ | ✓ | ✓ | – | ✓ |
Food Processing | ✓ | ✓ | – | ✓ | ✓ | – |
Medical Devices | – | – | – | ✓ | ✓ | – |
HVAC Systems | ✓ | ✓ | ✓ | – | – | – |
Automotive/Aerospace | – | ✓ | – | ✓ | ✓ | ✓ |
Note: Use performance benchmarks and modeling tools to validate your choices. Set measurable goals, such as energy efficiency or surface area loading, and track them throughout the design phase.
Material vs. Environment
Material compatibility plays a critical role in coil longevity and safety. You must match coil materials to the operating environment, considering factors like corrosion, temperature, and cleaning requirements. A decision matrix helps you visualize these relationships.
Environment | Stainless Steel | Copper | Incoloy/Alloy | Surface Area Loading Considerations |
---|---|---|---|---|
Corrosive | ✓ | – | ✓ | High surface area loading |
High Temperature | ✓ | – | ✓ | Optimized surface area loading |
Food/Medical | ✓ | – | – | Uniform surface area loading |
Marine | ✓ | ✓ | ✓ | Enhanced surface area loading |
Cleanroom | ✓ | – | – | Controlled surface area loading |
A dynamic decision matrix, using weighted criteria and sensitivity analysis, ensures you select the most robust and efficient solution. Methods like TOPSIS and fuzzy multi-criteria decision-making models allow you to balance technical performance, cost, and risk.
Callout: Always document your rationale and scoring. This practice supports quality assurance and helps you justify your final selection.
Installation, Maintenance, and Safety Best Practices for Heating Elements
Installation Guidelines for Electric Heating Coils
Proper Mounting
You ensure optimal performance and safety by mounting electric heating coils correctly. Always follow the manufacturer’s recommendations for orientation and support. Secure the coil firmly to prevent vibration or movement during operation. Use appropriate insulators to avoid electrical shorts and thermal expansion issues. When you install heating elements in ducts or enclosures, maintain adequate clearance from walls and other components. This spacing allows for proper airflow and heat dissipation.
Electrical Connections
You must make all electrical connections with care. Use terminals and connectors rated for the voltage and current of your system. Tighten all connections to prevent arcing or overheating. Label wires clearly to simplify future maintenance. Before energizing the system, double-check for exposed wires or loose fittings. A qualified electrician should verify the installation meets local codes and safety standards.
Maintenance Tips for Heating Coil Longevity
Inspection Schedules
You extend the life of heating elements by following a structured inspection schedule. Centralized maintenance management systems help you automate reminders and track service history. Routine inspections allow you to detect early signs of wear, corrosion, or electrical faults. Studies show that systematic preventive maintenance can extend equipment life by 20-30% and reduce unexpected breakdowns. Use smart sensors and digital documentation to monitor coil health and schedule timely interventions.
Cleaning and Care
You maintain efficiency and prevent premature failure by keeping electric heating coils clean. Dust, debris, and residue can insulate the coil, causing overheating. Regular cleaning, filter changes, and lubrication reduce wear and tear. Maintenance tracking tools help you identify trends and optimize care strategies. Always follow manufacturer guidelines for cleaning agents and methods. Keeping detailed records of maintenance actions supports warranty claims and improves operational efficiency.
Consejo: Dedication to preventive care and attention to detail significantly improve uptime and reduce operational costs.
Safety Protocols When Choosing the Right Heating Element
Emergency Procedures
You prepare for emergencies by establishing clear response protocols. Post emergency shutdown instructions near control panels. Train staff to recognize warning signs such as smoke, unusual odors, or tripped breakers. Keep fire extinguishers and first aid kits accessible. Regularly review and practice emergency drills to ensure everyone knows their role.
Training and Documentation
You build a safe workplace by providing thorough training on heating elements and electric heating coils. Ensure all personnel understand installation, operation, and maintenance procedures. Maintain up-to-date documentation, including wiring diagrams, service records, and safety data sheets. Digital maintenance software helps you track training completion and equipment status.
Safety Practice | Benefit |
---|---|
Staff Training | Reduces risk of accidents |
Clear Documentation | Simplifies troubleshooting |
Emergency Drills | Improves response readiness |
Note: Consistent training and documentation help you comply with regulations and maintain a safe, efficient facility.
You can select the right heating coil by following a structured approach:
- Define your application’s temperature and environmental needs.
- Match coil type and material to your specific requirements.
- Evaluate performance, safety features, and maintenance options.
Consejo: Always consult with experts and review certifications before making a final decision. Careful selection ensures reliable performance, safety, and long service life for your heating system.
PREGUNTAS FRECUENTES
What is the most important factor when selecting a heating coil?
You should prioritize matching the coil’s temperature rating and material to your application. This ensures safe operation and long service life. Always check compatibility with your process environment.
How often should you inspect electric heating coils?
You should inspect heating coils monthly for signs of wear, corrosion, or electrical issues. Regular checks help you catch problems early and maintain system efficiency.
Can you use the same heating coil for different applications?
You should not use the same coil for all applications. Each process may require specific materials, watt densities, or safety features. Always select a coil designed for your unique requirements.
¿Qué certificaciones debe buscar en los elementos calefactores?
Look for certifications such as UL, CSA, and ISO 9001:2015. These standards confirm that the heating element meets safety, quality, and performance requirements for your industry.
How do you calculate the required heating load?
You calculate heating load using this formula:
Power (W) = Mass × Specific Heat × Temperature Change / Time
You should gather accurate data for each variable to ensure proper sizing.
What maintenance steps extend heating coil lifespan?
You should clean coils regularly, check electrical connections, and replace damaged insulation. Following a preventive maintenance schedule reduces downtime and extends coil life.
Are flexible heating elements safe for high-temperature use?
Flexible heating elements work well for moderate temperatures. For high-temperature applications, you should verify the material’s maximum rating and consult the manufacturer for guidance.