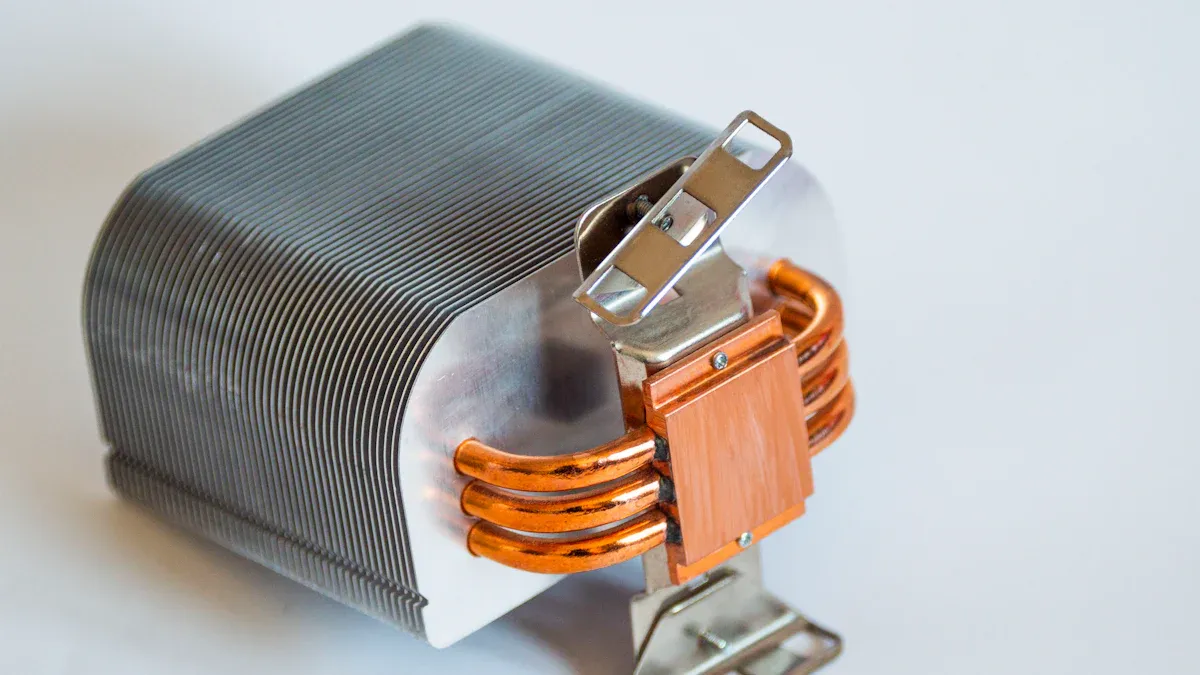
Selecting the right heating coil for your system demands careful attention to technical details. You must consider parameters like wire surface load, coil pitch, and the coil-to-wire diameter ratio, as these directly affect the performance and lifespan of your heating element. For example, a coil-to-wire diameter ratio between 5 and 12 ensures stability, while resistance adjustments of 10-30% are critical for metal-sheathed heating tubes. Properly matched heater elements not only deliver efficient heat but also help prevent costly failures.
Defining Your Heating Coil Application Needs
Choosing the right industrial heating coil starts with a clear understanding of your application’s unique demands. You must define temperature, power, and environmental factors before selecting a heating coil. This approach ensures your system operates safely and efficiently in any setting.
Setting Temperature Requirements
Maximum and Minimum Temperatures
You need to identify the highest and lowest temperatures your application will encounter. Industrial heating coil performance depends on these limits. For example, a process in a cleanroom requires strict temperature control, while a plant utilities room allows for broader ranges. The table below summarizes industry benchmarks for temperature and humidity control, based on ISPE and ASHRAE standards. These benchmarks help you validate your temperature requirements and ensure compliance with operational and regulatory needs.
Facility Space Type | Humidity Operating Range (%) | Notes on Temperature/Humidity Control and Validation |
---|---|---|
Clean utilities (technical) | Up to 60% | Temperature and humidity setpoints are based on ISPE and ASHRAE standards, adjusted for operator comfort and process needs, validating heating coil requirements. |
Raw materials warehouse (controlled) | 30–60% | Acceptance ranges reflect industry benchmarks and local conditions, supporting tolerance-based process validation. |
Controlled cleanroom grades (ISO 5 to ISO 8 / Grade A to D) | 30–60% | Tight environmental control aligns with industry guides and operator experience, confirming temperature requirement processes. |
Plant utilities room | Up to 80% | Broader humidity range reflecting less critical control, but still within recognized standards. |
Finished goods (refrigerated) | 20–80% | Extended ranges based on product and process needs, demonstrating flexibility validated by benchmarks. |
Temperature Uniformity
Uniform temperature distribution is essential for many applications. You must ensure the industrial heating coil delivers consistent heat across the entire area. Uneven heating can cause product defects or process inefficiencies. For example, in pharmaceutical or electronics manufacturing, even minor temperature fluctuations can impact quality. You should select a heating coil design that matches your system’s geometry and heat transfer needs.
Determining Power and Voltage
Calculating Wattage
You must calculate the power requirements for your application. Start by determining the total heat load, which depends on the mass, specific heat, and desired temperature rise of the material or space. Industrial heating coil selection relies on accurate wattage calculations to avoid underheating or overheating. Always factor in heat losses to the environment and any process-specific demands.
Voltage Matching
Matching the voltage of your heating coil to your system’s supply is critical. Using the wrong voltage can reduce efficiency or damage the coil. Industrial heating coil manufacturers offer products in a range of voltages to suit different applications. Always verify compatibility with your facility’s electrical infrastructure before installation.
Assessing Environmental Factors
Moisture and Chemical Exposure
Environmental conditions play a major role in heating coil performance. Exposure to moisture or chemicals can lead to corrosion, reduced efficiency, or premature failure. Studies show that pollutant emissions and indoor air quality can change significantly during heating seasons, especially in environments with poor ventilation or high humidity. You should choose materials and coatings that resist corrosion and withstand harsh chemicals, especially in industrial or laboratory settings.
- Statistical and empirical models assess heat pumps’ energy consumption and CO2 emissions under various conditions.
- Studies highlight pollutant emissions (CO, CO2, NOx, SO2, PM2.5, PAHs) from various heating systems, especially solid-fuel heating in rural China, linking emissions to health risks.
- Life cycle assessment quantifies environmental impacts of 13 residential heating systems in a typical German dwelling. Biomass heating systems show the lowest environmental impacts assuming sustainable fuel supply.
Ambient Conditions
Ambient temperature, humidity, and air quality affect both the efficiency and longevity of your industrial heating coil. Meteorology and topography can influence pollutant dispersion and concentration, impacting system performance. You must consider local climate, ventilation, and even the operational cycle of your heating system. For example, regions with high humidity or frequent temperature swings may require specialized coil materials or designs.
- The environmental advantage of heat pumps depends heavily on the local electricity generation mix; e.g., nuclear-heavy France benefits more than fossil-fuel-dependent regions like the USA.
- Indoor air quality monitoring during heating seasons shows increased pollutants and health risks due to insufficient ventilation and thermal conditions.
- Eco-efficiency analysis identifies air-source heat pumps (with/without PV) and wood gasifier systems as most environmentally and economically efficient.
Tip: Always assess your application’s environment before finalizing your industrial heating coil selection. This step helps you avoid costly replacements and ensures reliable operation.
Physical and System Constraints
Space and Mounting
You must evaluate the available space in your system before selecting a heating coil. Each installation site presents unique challenges. Some systems offer generous room for mounting, while others require you to fit the coil into tight or irregular spaces. You should measure the dimensions of your installation area with precision. This step helps you avoid costly modifications or delays during setup.
Many applications demand compact heating solutions. For example, laboratory instruments or medical devices often require miniature coils that deliver precise heat in confined spaces. In contrast, industrial ovens or HVAC systems may accommodate larger, more robust coils. You should always check the manufacturer’s specifications for minimum bend radius, mounting orientation, and clearance requirements.
Tip: Create a checklist of your system’s spatial limitations. This practice ensures you select a heating coil that fits seamlessly and operates safely.
Mounting options also influence your decision. Some heating coils come with brackets, flanges, or threaded fittings for easy installation. Others require custom mounting hardware. You should confirm that your chosen coil supports the mounting method best suited to your system. Secure mounting prevents vibration, reduces wear, and extends the coil’s service life.
Integration and Compatibility
You must ensure that the heating coil integrates smoothly with your existing system. Compatibility issues can lead to operational failures or safety hazards. Start by reviewing your system’s electrical and mechanical interfaces. Check that the coil’s terminals, connectors, and wiring match your equipment’s requirements.
Mechanical compatibility matters as much as electrical fit. You should verify that the coil’s shape, size, and mounting features align with your system’s design. Some applications require custom-shaped coils to fit around pipes, tanks, or other components. Others benefit from standard designs that simplify replacement and maintenance.
A table can help you compare integration factors for different applications:
Integration Factor | Considerations for Selection | Example Applications |
---|---|---|
Electrical Connection | Terminal type, voltage, current rating | Process heaters, ovens |
Mechanical Fit | Shape, size, mounting hardware | Laboratory equipment |
Control Integration | Sensor compatibility, feedback options | HVAC, industrial controls |
You should also consider how the heating coil interacts with sensors, controllers, and safety devices. Many applications require precise temperature monitoring. Proper integration ensures accurate feedback and reliable operation.
Note: Always consult your system’s documentation and the heating coil manufacturer’s guidelines. This approach helps you avoid costly compatibility issues and ensures long-term reliability.
Types of Heating Coil and Flexible Heating Element Options
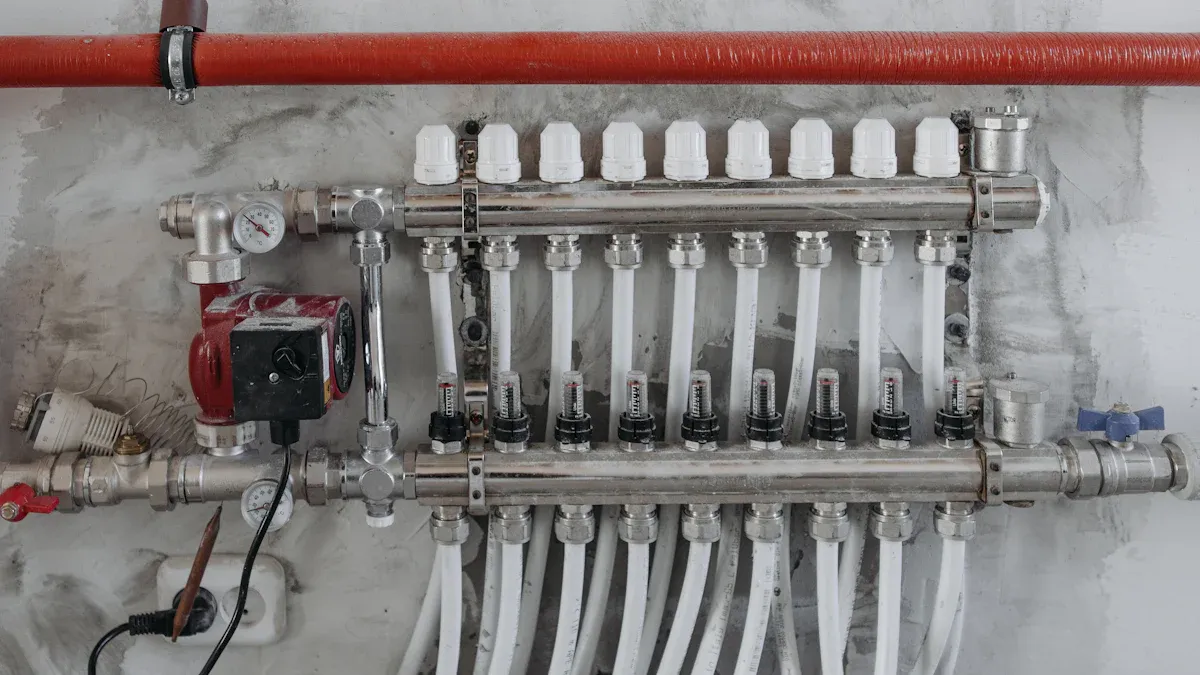
When you select a heating solution, you must understand the different types of heating coil and flexible heating element options available. Each type serves specific applications and environments, so your choice directly impacts system performance, reliability, and efficiency.
Common Heating Coil Types
Tubular Heating Coil
Tubular heating coils are among the most versatile options for both industrial and commercial applications. You find these coils in ovens, water heaters, and process equipment. Manufacturers design them with a metal sheath, often stainless steel or Incoloy, which protects the resistance wire inside. This construction allows you to use tubular coils in harsh environments, including those with moisture or chemical exposure. You can bend tubular coils into custom shapes, making them suitable for unique system layouts.
Finned Heating Coil
Finned heating coils increase the surface area for heat transfer. You often use these coils in air heating systems, duct heaters, and space heaters. The fins, usually made from aluminum or stainless steel, attach to the coil’s surface. This design improves efficiency by allowing more rapid heat dissipation into the surrounding air. Finned coils work well in HVAC systems and industrial heating coil applications where you need to heat large air volumes quickly.
Cartridge Heater
Cartridge heaters provide concentrated, high-density heat in a compact form. You insert these heaters directly into drilled holes in metal blocks, molds, or platens. Cartridge heaters deliver precise temperature control, making them ideal for plastics processing, packaging equipment, and die heating. Their robust construction ensures long service life, even in demanding industrial heating coil environments.
Open Coil Heater
Open coil heaters use exposed resistance wire, typically made from nickel-chromium alloys. You see these heaters in forced air heating systems, dryers, and some laboratory equipment. Open coil heaters offer rapid heat-up times and high efficiency. However, you should avoid using them in environments with high humidity or corrosive gases, as the exposed wire can degrade quickly.
Note: According to the Global Furnace Heating Coils Market Report, electric heating coils dominate the market due to their versatility and energy efficiency. Induction heating coils are gaining popularity in industrial sectors like automotive and aerospace, where rapid heating and sustainability are critical. Residential applications remain the largest segment, but industrial heating coil demand is rising as manufacturing expands and precise temperature control becomes more important.
Flexible Heating Element Solutions
Flexible heating element technology has transformed how you approach heating challenges in modern systems. These heaters adapt to complex shapes, surfaces, and environments, offering unmatched customization and performance.
Custom Shapes and Profiles
You can specify flexible heating elements in almost any shape or size. Manufacturers use materials like silicone, polyester, and polyimide (Kapton) to create heaters that conform to curved, irregular, or compact surfaces. For example, silicone flexible heating elements provide excellent durability, moisture resistance, and temperature stability. You often use them in freeze protection, medical devices, and food service equipment.
Polyester flexible heaters offer a lightweight, cost-effective solution for lower temperature applications. You find them in electronics, battery warming, and display panels. Kapton flexible heating element designs excel in environments that demand high temperature resistance, chemical stability, and electrical insulation. These heaters serve aerospace, medical, and electronics industries where reliability and precision matter most.
Tip: When you need a heater for a unique surface or a tight space, consider a flexible heating element. You can order custom shapes, wattages, and voltages to match your exact requirements.
Specialized Applications
Flexible heating elements excel in specialized and demanding applications. Silicone rubber heaters, for example, withstand harsh environments and repeated flexing. You use them for pipe tracing, tank heating, and freeze protection in industrial heating coil systems. Types of silicone rubber heaters include etched-foil and wire-wound designs, each offering specific benefits for heat distribution and durability.
Polyimide (Kapton) flexible heating elements deliver rapid, uniform heat transfer and resist chemicals and moisture. You rely on these heaters in aerospace for de-icing, in medical devices for patient warming, and in automotive systems for battery and fuel line heating. Mica surface heaters, another flexible option, provide high-temperature capability and uniform heat, making them suitable for plastics processing and semiconductor manufacturing.
You also find silicone flexible heating elements in food service, electronics manufacturing, and renewable energy systems. For example, you use them to prevent condensation in wind turbines or to maintain battery temperatures in solar-powered devices. Polyester flexible heaters offer a solution for consumer goods like heated clothing, vehicle seats, and pet warming pads.
A table below summarizes the key features of common flexible heating element materials:
Material | Temperature Range | Key Properties | Typical Applications |
---|---|---|---|
Silicone | -60°C to 230°C | Flexible, moisture resistant | Pipe tracing, tank heating, food service |
Polyester | -40°C to 150°C | Lightweight, cost-effective | Electronics, displays, battery warming |
Polyimide (Kapton) | -269°C to 260°C | Chemically resistant, thin, durable | Aerospace, medical, electronics |
Mica | Up to 600°C | High-temp, uniform heat | Plastics, semiconductors, industry |
Callout: Flexible heating elements such as silicone, polyester, and Kapton flexible heating element designs allow you to solve heating challenges in almost any industry. Their adaptability, rapid heat transfer, and customizability make them essential for modern system design.
You should always match the flexible heating element material and construction to your application’s temperature, chemical, and mechanical requirements. This approach ensures safety, efficiency, and long-term reliability.
Matching Heating Coil Materials and Construction
Material Selection for Durability
Stainless Steel and Alloys
You must select the right material for your heating coil to ensure long-term durability. Stainless steel stands out as a popular choice because it resists rust and maintains strength at high temperatures. Many industrial systems use stainless steel for its ability to handle harsh environments. You may also encounter alloys designed for specific needs, such as improved heat transfer or resistance to certain chemicals. When you compare materials, you notice that stainless steel often outperforms basic metals in both lifespan and reliability.
In applications where you use silicone or polyester as part of the system, you must ensure the coil material does not react with these components. For example, silicone rubber heaters often pair with stainless steel coils to provide robust, flexible heating in demanding settings. Polyester-based systems may require different alloys to avoid unwanted chemical interactions. You should always check compatibility charts before making your final selection.
Corrosion and Oxidation Resistance
Corrosion and oxidation can shorten the life of your heating coil. You need to choose materials that resist these threats, especially if your system operates in humid or chemically aggressive environments. Stainless steel offers excellent protection against both corrosion and oxidation. In some cases, you may need to select a special alloy if your application involves exposure to acids, bases, or saltwater.
Silicone and polyester both play roles in protecting heating elements. Silicone rubber heaters use silicone as an outer layer, shielding the coil from moisture and chemicals. Polyester insulation can also help prevent corrosion, especially in low-temperature applications. You should inspect your system regularly to catch early signs of corrosion and replace any damaged parts promptly.
Tip: Always match your coil material to the environment and the other materials in your system, such as silicone or polyester, to maximize durability.
Construction and Shape Considerations
Standard vs. Custom Designs
You face a choice between standard and custom heating coil designs. Standard coils offer quick availability and proven performance for common applications. Custom designs, however, allow you to match the coil exactly to your system’s geometry and heating needs. For example, you may need a coil that fits around a complex shape or delivers uniform heat to a specific area.
Recent engineering studies show that coil shape has a major impact on performance. Researchers used Finite Element Analysis to compare traditional double-spiral heaters with coils shaped like space-filling fractal curves. They found that certain fractal shapes, such as Hilbert and Moore curves, provide better temperature uniformity and use metal more efficiently. You can use this information to guide your decision when you need precise heat control.
Silicone and polyester both adapt well to custom coil designs. Silicone rubber heaters can be molded into almost any shape, making them ideal for unique system layouts. Polyester-based heaters offer flexibility for low-profile or lightweight applications. You should consult with manufacturers to explore custom options that fit your requirements.
Sizing for Heat Distribution
Proper sizing ensures your heating coil delivers even heat across your target area. You must consider factors such as coil diameter, pitch, and spacing. Simulation analyses have shown that adjusting these parameters can improve heat transfer efficiency. For example, vertical helical coils with optimized spacing and diameter achieve better performance in many thermal systems.
Silicone and polyester both influence sizing decisions. Silicone rubber heaters allow you to create large or small heating zones, depending on your needs. Polyester heaters work well in compact spaces where you need gentle, even heat. You should always calculate the required wattage and match the coil size to your application.
A table can help you compare sizing considerations for different materials:
Material | Best For | Typical Applications |
---|---|---|
Silicone | Flexible, high-temp | Silicone rubber heaters, medical |
Polyester | Lightweight, low-temp | Battery warming, electronics |
Note: Always balance coil size, material, and shape to achieve the best heat distribution for your system.
Heater Performance and Energy Efficiency
When you select a heater for your system, you must focus on both performance and energy efficiency. These factors determine how well your heater meets your process needs and how much energy you consume over time. Careful planning helps you avoid wasted energy and ensures reliable temperature regulation.
Power Density and Heat Output
Calculating Power Needs
You should always start by calculating the power needs for your application. Power density, which measures the amount of power delivered per unit area or volume, plays a key role in heater selection. For example, technical studies on thermoelectric generators show that power densities can range from 0.9 W/cm² up to 3 W/cm², with maximum efficiencies reaching 8.5%. Another study on stacked thermoelectric generator designs demonstrates a power density of 48.22 W/L and a power output of 848.37 W at high temperatures. These benchmarks help you understand what to expect from modern heating coil technology.
To determine your required power, consider the size of the area you need to heat, the desired temperature rise, and the heat losses to the environment. Use the formula:
Power (W) = Mass × Specific Heat × Temperature Rise / Time
This calculation ensures your heater delivers enough energy to reach and maintain your target temperature.
Avoiding Overheating
Overheating can damage your heater and your system. You must size your heater correctly and use controls that prevent excessive temperatures. Always check the maximum allowable power density for your specific heater type. Exceeding these limits can cause hot spots, reduce lifespan, or create safety hazards. Install sensors and thermal cutoffs to monitor and protect your system.
Tip: Use a heater with built-in safety features, such as thermal fuses or automatic shutoff, to reduce the risk of overheating.
Energy Efficiency Strategies
Minimizing Energy Consumption
You can minimize energy consumption by selecting a heater that matches your application’s needs. Avoid oversizing, as this leads to wasted energy and higher operating costs. Insulate your system to reduce heat loss and maintain stable temperatures. Choose materials with good thermal conductivity to improve heat transfer and reduce warm-up times.
- Use programmable controllers to adjust heater output based on demand.
- Schedule regular maintenance to keep your heater operating at peak efficiency.
Optimizing Heat Transfer
Optimizing heat transfer ensures your heater delivers energy where you need it most. Position your heater close to the target area and use designs that maximize surface contact. For example, finned heaters increase surface area and improve air heating efficiency. Flexible heaters conform to complex shapes, providing even heat distribution.
A table below summarizes key strategies for improving heater efficiency:
Strategy | Benefit |
---|---|
Proper Sizing | Reduces energy waste |
Good Insulation | Maintains temperature |
Efficient Placement | Improves heat transfer |
Regular Maintenance | Extends heater lifespan |
Note: Efficient heater operation not only saves energy but also supports consistent temperature regulation and long-term reliability.
Installation, Maintenance, and Safety for Heating Coils
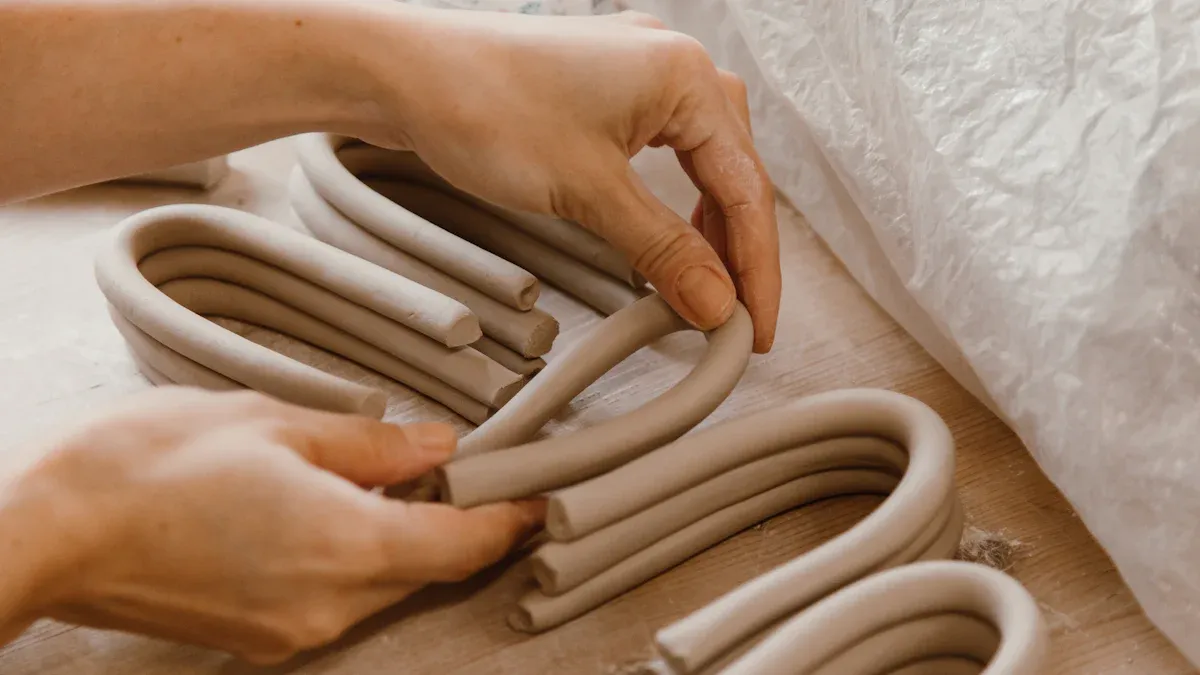
Installation Best Practices
Mounting and Electrical Connections
You must follow precise steps when installing a heater to ensure safe and reliable operation. Always secure the heater firmly to prevent movement or vibration. Use manufacturer-approved brackets or mounting hardware. Check that all electrical connections are tight and free from corrosion. Loose wires can cause overheating or electrical faults. Use the correct wire gauge and insulation for your voltage and current requirements. Never bypass safety devices or grounding connections.
Tip: Double-check all connections before powering up your heater. This simple step can prevent many common installation issues.
Sensor Placement
Proper sensor placement is critical for accurate temperature control. Position sensors close to the heating coil or the area you want to monitor. Avoid placing sensors near drafts or heat sinks, as these can cause false readings. Secure sensors firmly to prevent movement during operation. Use shielded cables if your system operates in an area with electrical noise.
Maintenance and Inspection
Cleaning and Service Intervals
Regular maintenance keeps your heater running efficiently. Clean the heating coil and surrounding components to remove dust, debris, and buildup. Schedule inspections at least once a year, or more often in demanding environments. Inspection reports help you track system performance and spot early signs of wear. These reports often highlight conditions, needed repairs, and recommendations. This structured approach helps you prevent breakdowns, improve energy efficiency, and extend the life of your equipment.
Routine maintenance tasks include:
- Cleaning coils and removing debris
- Checking for unusual noises or vibrations
- Inspecting electrical connections
- Verifying thermostat and control operation
Professional evaluations and annual inspections ensure your heater operates at peak efficiency. These steps also help you detect issues before they become costly problems.
Replacement Guidelines
Replace your heater or heating coil if you notice reduced performance, visible damage, or frequent failures. Follow the manufacturer’s guidelines for service life and replacement intervals. Always use approved replacement parts to maintain system safety and efficiency. Keep detailed records of all maintenance and replacements for future reference.
Safety and Compliance
Overheat Protection
Install overheat protection devices to safeguard your system. Use thermal cutoffs, fuses, or temperature limiters to prevent dangerous temperature rises. These devices shut down the heater if it exceeds safe limits. Regularly test safety devices to ensure they function correctly.
Standards and Certifications
You must comply with industry standards and certifications to ensure safe operation. Safety protocols address hazards such as electrical shocks, burns, and chemical exposure. The table below summarizes key safety aspects for heating coil systems:
Safety Aspect | Details |
---|---|
Common Hazards | Electrical shocks, burns, chemical exposure, falls |
Safety Checklist | PPE use, Lockout/Tagout, equipment inspection, emergency response |
Training Topics | Electrical safety, refrigerant handling, fall protection |
Certifications | MSP, CSD, ANSI/ANAB ISO/IEC 17024:2012 |
Regulatory Compliance | EPA, OSHA standards |
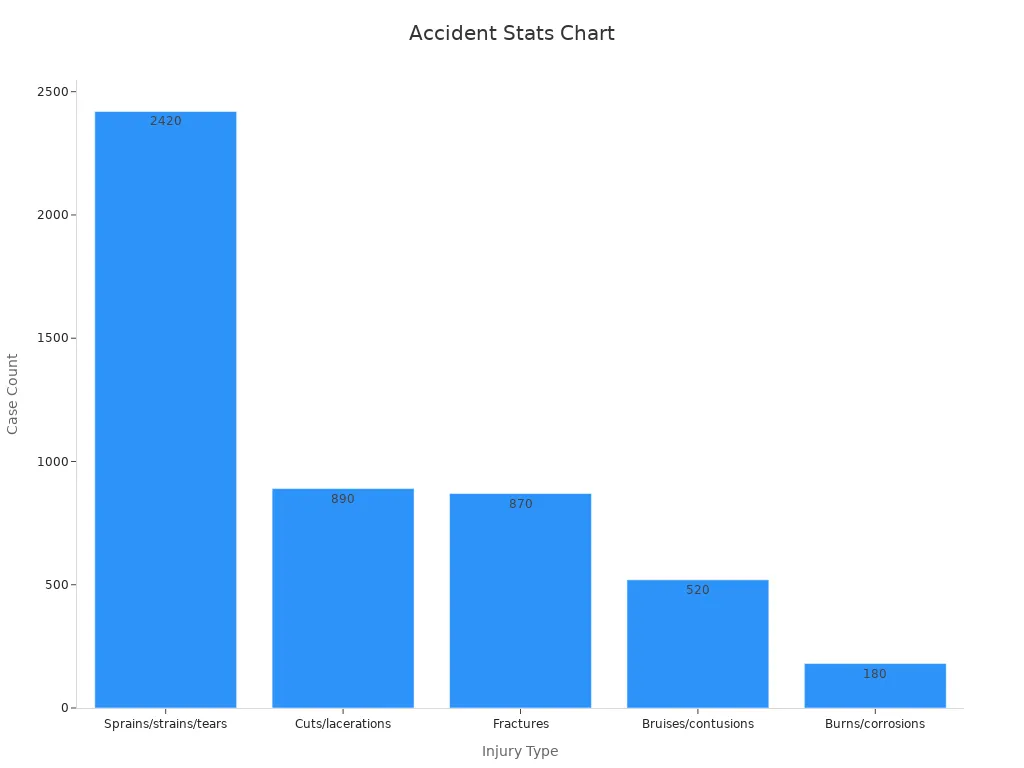
Recent safety standards and incident data highlight the risks of improper installation or maintenance. Documented injuries and fatalities, including carbon monoxide poisoning, reinforce the need for strict safety protocols. Certifications such as Master Safety Professional (MSP) and Certified Safety Director (CSD) show formal recognition of safety expertise. You should always follow regulatory requirements and keep up with the latest safety practices.
Note: Safety management software can help you track checklists, training, and compliance for your heater system.
Avoiding Common Heating Coil Selection Mistakes
When you select a heating coil, you must avoid common mistakes that can compromise your system’s safety, efficiency, and reliability. Many failures stem from overlooking compatibility, environmental factors, or maintenance needs. By understanding these pitfalls, you can make informed decisions and protect your investment.
System Compatibility Issues
Electrical and Physical Mismatches
You need to ensure that your heating coil matches your system’s electrical and physical requirements. Electrical mismatches, such as incorrect voltage or current ratings, can cause overheating, reduced performance, or even equipment failure. Physical mismatches, like improper fit or incompatible mounting, may lead to mechanical stress and premature wear.
- Technical documentation and failure case studies highlight several issues:
- Stress corrosion cracking in Incoloy 800 water immersion heating elements often results from chloride-containing water.
- Pitting corrosion, sheath tube failure, fatigue, and overheating frequently occur due to metallurgical incompatibility and thermal stresses.
- Incompatibility between sheath and wire materials, or between materials and environmental conditions, can cause corrosion and mechanical breakdowns.
- Case studies show that thermal stresses exceeding material yield strength, especially in Incoloy 800HT pipes, lead to failure.
- Acid dew point condensates in steel heating elements can trigger corrosion-induced failures.
You should always verify that the coil’s materials, electrical ratings, and design align with your system’s specifications. Simulation and modeling tools, such as finite element analysis, can help you predict and prevent these issues.
Environmental Oversights
Corrosion and Moisture Risks
You must consider the environment where your heating coil will operate. Moisture, chemicals, and airborne contaminants can accelerate corrosion and degrade performance. Many failures occur when you overlook these risks during selection.
- Common environmental oversights include:
- Using materials that cannot withstand exposure to chlorides, acids, or high humidity.
- Failing to account for condensation or chemical vapors that attack coil surfaces.
- Ignoring the need for protective coatings or specialized alloys in harsh environments.
You can prevent these problems by choosing corrosion-resistant materials and ensuring proper sealing. Regular inspection helps you catch early signs of corrosion before they cause major failures.
Tip: Always match your coil’s material and construction to the specific environmental conditions of your application.
Maintenance Underestimation
Access and Serviceability
You should never underestimate the importance of maintenance when selecting a heating coil. Poor access or difficult service procedures can lead to neglected equipment and increased risk of failure.
- Maintenance performance statistics and service reports reveal:
- Heating equipment ranks as the second leading cause of fires in industrial settings.
- Facilities without preventive maintenance programs experience a 300% increase in equipment failure rates.
- Delaying maintenance until failure occurs leads to higher costs and greater hazards.
- Proactive maintenance can prevent over two-thirds of equipment failures, improving both safety and efficiency.
You need to design your system for easy access to coils and connections. Schedule regular inspections and cleaning to extend the life of your equipment. By prioritizing serviceability, you reduce downtime and avoid costly repairs.
Note: Investing in preventive maintenance not only protects your system but also ensures compliance with safety standards and reduces long-term costs.
When to Consult Experts or Manufacturers for Heater Solutions
Custom and Complex Applications
Unique System Requirements
You may encounter situations where standard heating coils cannot meet your system’s demands. Custom and complex applications often require you to consult with experts or manufacturers. These professionals help you navigate technical challenges and ensure your heating solution matches your exact needs.
- Custom-formed tubular heating elements serve specialized equipment such as laboratory instruments, testing chambers, medical devices, and pilot plants. You benefit from nearly limitless formability and configurable wattage in these cases.
- Selecting the right sheath material—stainless steel, Incoloy, titanium, or copper—ensures durability and corrosion resistance. Manufacturer guidance becomes essential when you face harsh or unique environments.
- Watt density must match your application’s intensity. Proper selection prevents overheating and maximizes efficiency.
- You may need custom shapes and mounting styles, such as straight, U-shaped, hairpin, immersion, flange-mount, screw-in, or clamp-on. Manufacturer collaboration helps you address space, heat distribution, and installation needs.
- Advanced safety features, including explosion-resistant designs, overheat protection, timing controls, and temperature sensors, become critical in hazardous environments.
- Insulation materials like magnesium oxide and coatings such as ceramics, fluoropolymers, or polyimides balance thermal transfer, electrical insulation, and chemical resistance.
- Environmental factors—high temperatures, corrosive media, or chemical exposure—impact element design. Detailed consultation ensures performance and longevity.
- Manufacturer support provides engineering expertise and customization capabilities. You meet industry requirements and comply with quality and safety standards.
If you work with a custom silicone rubber heater, you gain flexibility in design and performance. These heaters adapt to complex shapes and deliver reliable heat in demanding environments.
Technical Support and Troubleshooting
Assistance and Warranty Options
You may face technical issues with heating coils during operation. Manufacturer technical support helps you resolve these problems quickly and efficiently. Support teams guide you through troubleshooting steps and provide solutions tailored to your system.
- Dirty filters and clogged coils often cause heat pump malfunctions. You should clean and replace filters regularly to prevent these issues.
- Proper sizing and installation play a key role in efficient heating coil operation. Manufacturer support ensures you select and install the right components.
- Some problems, such as refrigerant leaks or electrical failures, require professional intervention. Manufacturer assistance helps you address these complex issues safely.
A systematic approach to troubleshooting improves your results. For example, when diagnosing heating coil issues in walk-in coolers, you should:
- Check if both evaporator and condenser fans operate correctly.
- Inspect for evaporator coil freeze-up.
- Ensure coils remain clean and free of debris.
This method, known as the ABC (Airflow Before Charge) principle, prioritizes airflow and coil condition checks before adjusting refrigerant levels. You save time and avoid unnecessary repairs by following this strategy.
Manufacturers also offer warranty options that protect your investment. You receive coverage for defects and technical support for installation or operational questions. Applications that benefit from silicone rubber heating elements often require this level of support due to their specialized nature.
Tip: Always reach out to your manufacturer’s technical support team when you encounter persistent or complex heating coil issues. Their expertise ensures safe, efficient, and long-lasting operation.
Selecting the right heating coil for your system ensures optimal performance and long-term reliability. You must consider temperature, power, environment, and compatibility for the best results. Case studies highlight the benefits of careful selection:
- A Canadian oil reservoir increased production by 25% with optimized heating elements.
- A U.S. oil field reduced energy use by 30% through precise temperature and power control.
Consult experts for custom or complex needs. Proper selection protects your investment and supports safe, efficient operation.
FAQ
What factors should I consider when choosing a heating coil material?
You should evaluate temperature range, corrosion resistance, and compatibility with your system. Stainless steel works well for most environments. For harsh chemicals or high humidity, select specialized alloys. Always match the material to your application’s needs.
How do I calculate the correct wattage for my heating coil?
Use this formula:
Power (W) = Mass × Specific Heat × Temperature Rise / Time
You must also account for heat losses and process requirements. Accurate calculations ensure efficient and safe operation.
Can I use a standard heating coil in a custom-shaped system?
Standard coils fit many applications. For unique shapes or tight spaces, you should request a custom-designed coil. Manufacturers can create coils that match your system’s geometry and mounting needs.
How often should I inspect or maintain my heating coil?
You should inspect your heating coil at least once a year. In demanding environments, increase inspection frequency. Regular cleaning and maintenance extend the coil’s lifespan and prevent unexpected failures.
What are the signs that my heating coil needs replacement?
Common signs include reduced heating performance, visible damage, frequent tripping of safety devices, or unusual noises. If you notice any of these, replace the coil promptly to maintain system safety.
Do flexible heating elements work in high-temperature applications?
Flexible heating elements, such as silicone or polyimide (Kapton), handle a wide temperature range. Always check the manufacturer’s specifications for maximum temperature ratings before installation.
Why is voltage matching important for heating coils?
Voltage mismatches can cause overheating, reduced efficiency, or coil failure. You must always match the coil’s voltage rating to your system’s supply for safe and reliable operation.
When should I consult a heating coil manufacturer or expert?
Consult an expert if your application involves custom shapes, harsh environments, or complex control requirements. Manufacturer support ensures you receive the right solution and technical guidance.