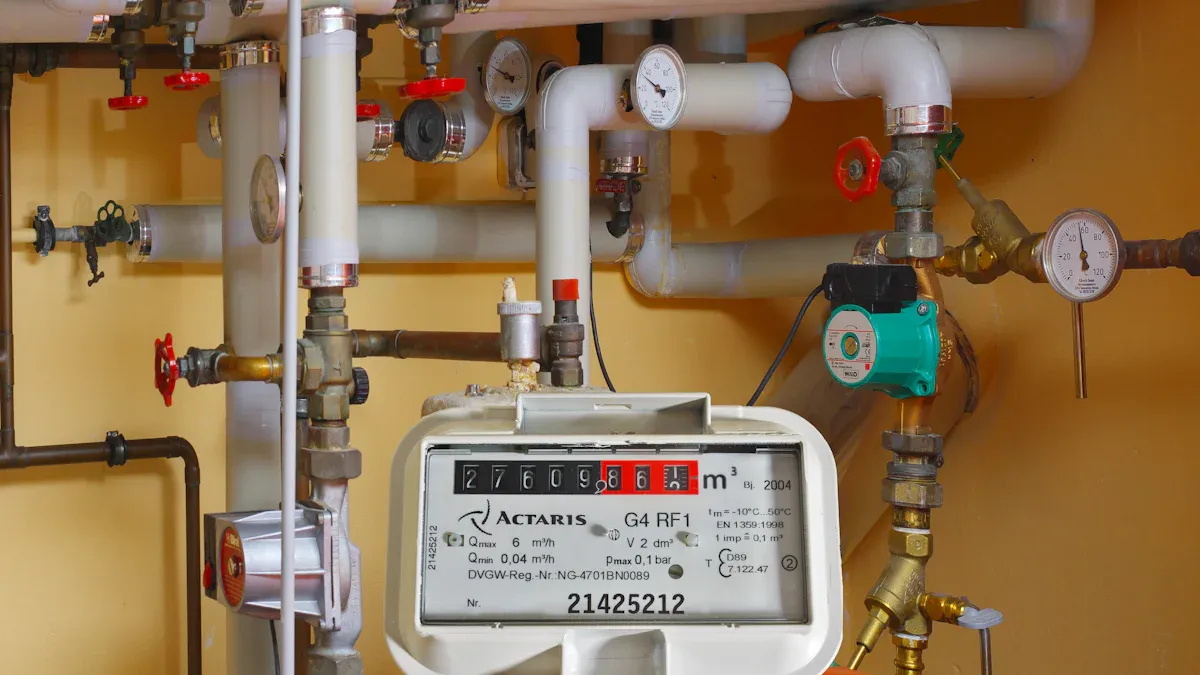
You depend on efficient heat exchanger heating to keep your system running at peak performance. Without a heat exchanger, up to 50% of primary energy in HVAC systems can be lost as waste heat, driving up your costs and reducing comfort. The table below shows how much energy and money you risk losing without proper heat recovery:
Example | Amount | Impact |
---|---|---|
Primary energy lost as waste heat | 50% | Major inefficiency and higher utility bills |
Potential annual energy savings (Europe) | 100 TWh | Massive cost savings with modern heat exchangers |
A quality heat exchanger also protects your home from harmful gases and system failures, making it essential for safety and reliability.
Understanding Heat Exchanger Heating
What Is a Heat Exchanger?
You rely on a heat exchanger to transfer heat efficiently between two or more fluids without mixing them. In heating systems, this process allows you to extract energy from one medium—such as hot water, steam, or air—and deliver it to another, like the air in your home or the water in your radiators. The design of a heat exchanger leverages thermodynamic principles. Heat moves from a higher temperature fluid to a lower temperature fluid, following the laws of thermodynamics. This process ensures that your system uses energy effectively and maintains safe operation.
注: Heat exchanger heating uses materials like copper or stainless steel to maximize heat transfer and resist corrosion, ensuring long-term reliability.
Types of Heat Exchangers Used in Heating
You encounter several types of heat exchangers in modern heating systems. Each type offers unique advantages for specific applications.
Plate Heat Exchangers
Plate heat exchangers use thin, corrugated metal plates to create channels for fluids. The large surface area and turbulence between plates provide high thermal performance. You benefit from their compact size and easy maintenance. These exchangers often use counterflow arrangements, which maximize heat transfer efficiency by maintaining a strong temperature gradient between fluids.
Shell and Tube Heat Exchangers
Shell and tube heat exchangers consist of a series of tubes enclosed within a larger shell. One fluid flows through the tubes, while another flows around them inside the shell. Baffles inside the shell direct the flow and increase turbulence, which improves heat transfer. You often find these exchangers in industrial and commercial heating systems due to their adaptability and robust construction.
Finned Tube Heat Exchangers
Finned tube heat exchangers add metal fins to the outside of tubes, increasing the surface area for heat transfer. This design enhances the efficiency of air-to-liquid or air-to-steam heating systems. You see these exchangers in applications where maximizing heat transfer from air is critical, such as in HVAC coils and baseboard heaters.
Common Applications in Residential and Commercial Heating
You use heat exchanger heating in a wide range of settings. In residential systems, plate and finned tube exchangers help deliver comfortable indoor temperatures while keeping energy use low. In commercial buildings, shell and tube exchangers handle larger loads and more complex requirements.
A four-year study by Berkeley’s Center for the Built Environment analyzed nine commercial buildings with radiant heating systems. These buildings, most built or renovated since 2010, achieved a median energy use intensity of 38 kBtu/ft² and high occupant satisfaction. Seven out of nine scored above 90 on EnergyStar, showing top-tier efficiency. Integrating radiant systems with heat exchangers led to both energy savings and improved comfort.
You also find specialized heat exchangers in many settings:
- Air-to-air heat pipe exchangers recover heat from exhaust air to preheat or precool incoming air, reducing heating and cooling loads.
- Wrap-around heat pipe exchangers enhance chilled water air handlers, providing energy savings and improved dehumidification.
- These systems serve high-rise offices, universities, retail spaces, healthcare facilities, and well-insulated homes.
By choosing the right type of heat exchanger heating, you ensure your system delivers reliable, efficient, and comfortable performance in any environment.
How Heat Exchanger Heating Works
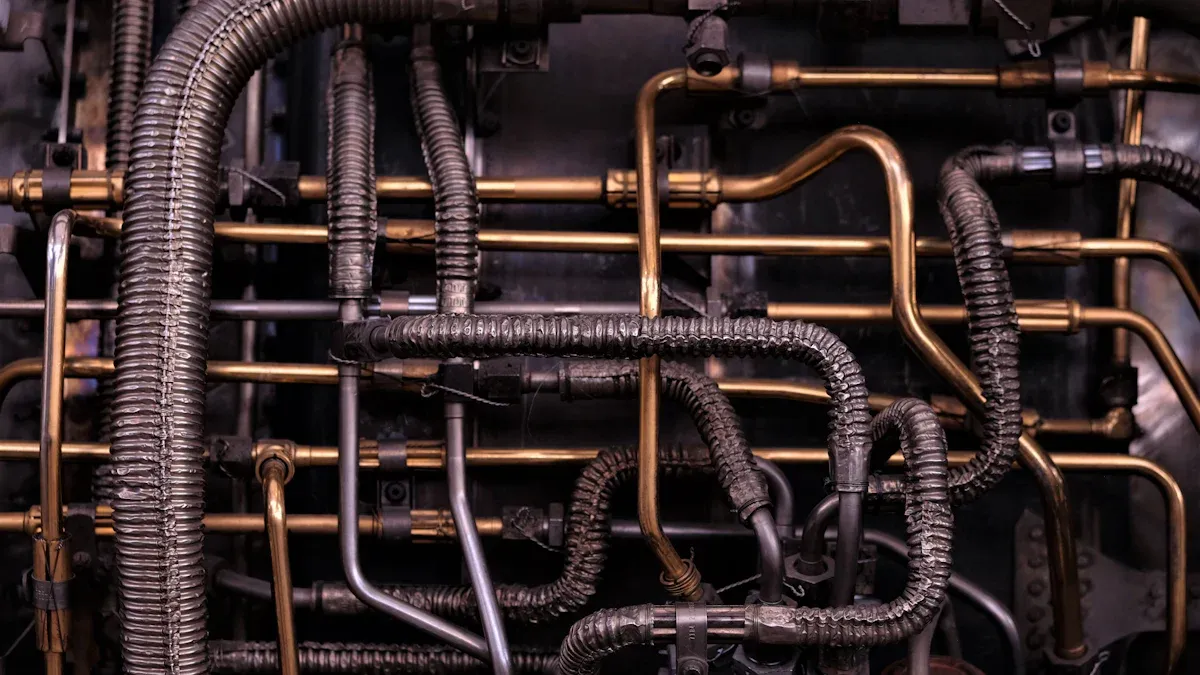
The Heat Transfer Process
Mediums Involved (Air, Water, Steam)
You encounter three main mediums in heat exchanger heating: air, water, and steam. Each medium has unique thermal properties that influence how efficiently your system transfers heat. Air is lightweight and easy to move, making it ideal for forced-air systems. Water offers high heat capacity, which allows you to store and distribute large amounts of energy efficiently. Steam, with its latent heat, delivers rapid and intense heating, especially in industrial or older residential systems.
Empirical research shows that the choice of medium affects the heat transfer coefficient, friction factor, and overall system efficiency. Engineers rely on experimental data to determine how fluid velocity, viscosity, and passage geometry impact performance. For example, adding fins to tubes increases the heat transfer area, compensating for air’s higher convection resistance. These findings guide you in selecting the right medium for your application, ensuring optimal heat exchanger heating.
Flow Patterns (Counterflow, Parallel Flow)
You benefit from two primary flow patterns in heat exchanger heating: counterflow and parallel flow. In counterflow arrangements, hot and cold fluids move in opposite directions. This setup maintains a strong temperature gradient along the entire length of the exchanger, maximizing heat transfer. Parallel flow, where both fluids move in the same direction, offers simpler construction but lower efficiency.
Experimental investigations have produced formulas for predicting heat transfer in both configurations. Researchers analyze velocity distributions and flow angles to optimize performance. Counterflow designs consistently outperform parallel flow in terms of thermal efficiency, making them the preferred choice for most modern systems.
ヒント When you select a heat exchanger, prioritize counterflow designs for higher efficiency, especially in applications where maximizing energy recovery is critical.
Integration with Boilers, Furnaces, and Heat Pumps
You often integrate heat exchangers with boilers, furnaces, and heat pumps to create a complete and efficient heating system. This integration allows you to recover waste heat, balance loads, and reduce emissions. The table below summarizes research-based comparisons of different integration strategies:
Integration Type | Key Findings | Performance Metrics | Environmental/Economic Impact |
---|---|---|---|
Absorption Heat Pumps (AHP) in district heating | Recover waste heat, reduce pollutant emissions | 25.6% reduction in heating season pollutant emissions | Lower heating cost per unit distance (27.36 CNY/GJ) when optimized |
Thermal storage tanks with heat exchangers in CHP units | Peak shaving, load management | Electricity consumption per unit heat load decreases with increased heat load | Improves system economy, requires careful temperature control |
Distributed heating with multi-energy resources | Balances regional heating fluctuations | Large-scale waste heat utilization potential | Supports low-carbon economy and clean energy coupling |
Coupling AHP with solar energy | Clean energy integration | Enhances energy contribution and stability | Promotes sustainable heating system reform |
You see that integrating heat exchangers with these systems improves energy efficiency and reduces environmental impact. However, you must also manage operational challenges, such as heat loss and system complexity. Automated controllers and variable flow systems help you maintain optimal performance by adjusting flow rates and temperatures in real time.
Real-World Example: Home Heating System
You can observe the benefits of heat exchanger heating in real-world home heating systems. Studies from the Department of Energy and regional energy councils show that homes using heat pumps with heat exchangers achieve seasonal coefficients of performance (COP) ranging from 1.8 to 3.3. This means your system delivers up to three times more heat energy than the electrical energy it consumes, especially in mild climates or with high-quality installations.
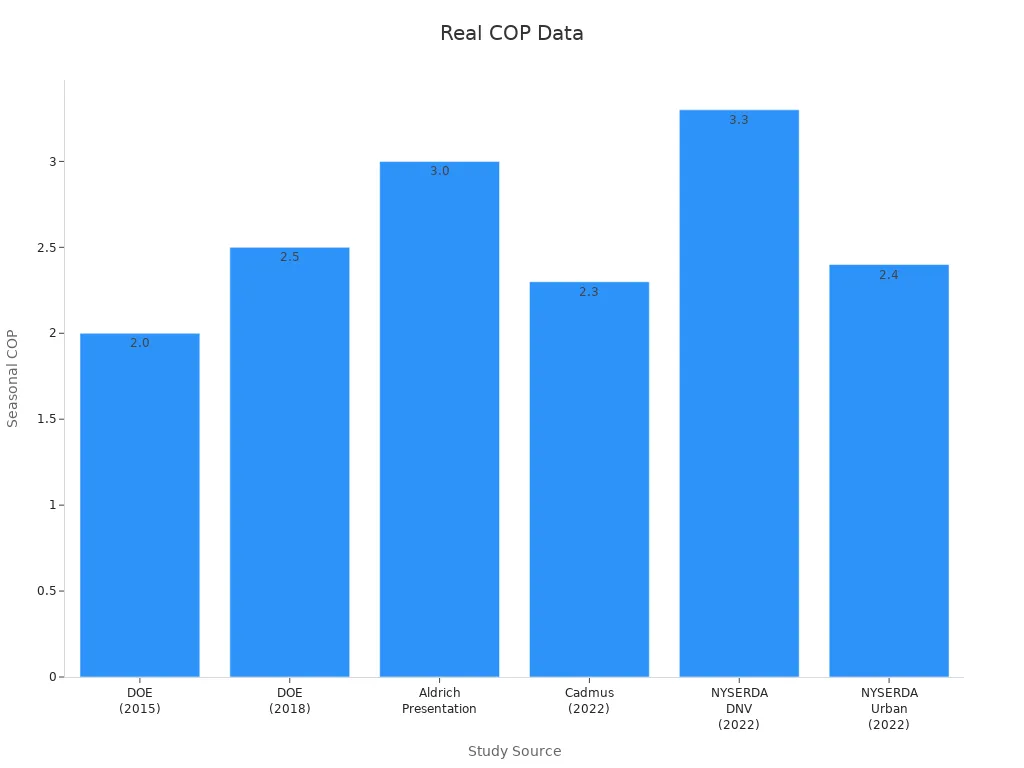
You notice that performance varies based on climate, installation quality, and system type. For example, cold-climate heat pumps in Vermont achieved up to 88% of their rated heating performance, while some systems in milder regions exceeded their nameplate ratings. Geothermal heat pumps, which use the stable temperature of the ground, can reach COPs around 3.5, providing even greater efficiency.
To ensure your system operates at peak efficiency, you should monitor temperature, flow rate, and pressure using sensors. Regular maintenance, such as cleaning and leak detection, helps you prevent unexpected failures and maintain consistent performance. Advanced technologies like computational fluid dynamics (CFD) simulations and automated controllers further optimize your system, adapting to changing load conditions and maximizing energy savings.
注: By understanding the operational process and integrating modern monitoring and optimization techniques, you ensure your heat exchanger heating system delivers reliable, efficient, and sustainable comfort year-round.
Benefits of Heat Exchanger Heating
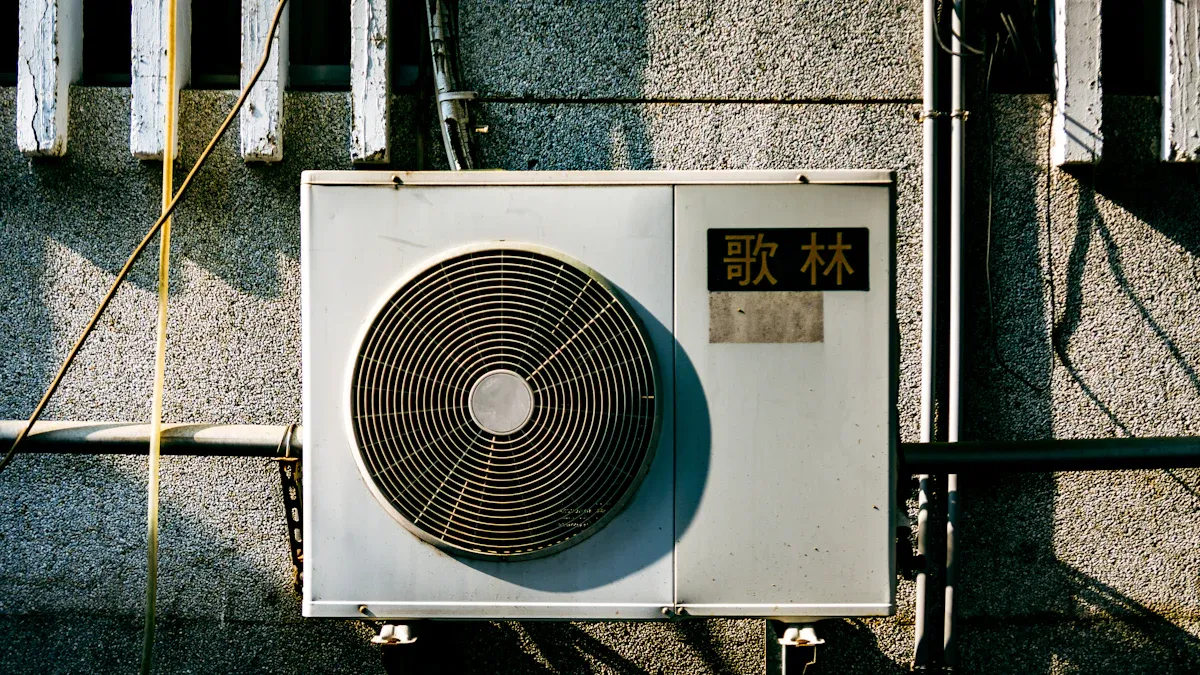
Improved Energy Efficiency
Maximizing Heat Utilization
You gain a significant advantage when you use heat exchanger heating in your system. The design of modern heat exchangers focuses on maximizing the transfer of thermal energy between fluids. By minimizing the temperature difference between the hot and cold sides, you ensure that more heat moves where you need it. Engineers use techniques like pinch minimization and surface structuring to increase the contact area and turbulence, which boosts the amount of heat transferred. When you select the right size and configuration, you achieve optimal thermal performance without excessive energy loss.
Reducing Energy Waste
You can see the impact of these improvements in real-world energy consumption statistics. The following table highlights how heat exchanger heating systems reduce energy use and improve efficiency:
Metric | Value/Range | Description |
---|---|---|
Energy consumption reduction | 22% to 31% | Average reduction in energy needed for hot water preparation using new horizontal heat exchanger prototypes in single-family buildings |
Commercial device efficiency | 23.4% to 41.0% | Efficiency range of commercially available heat recovery devices depending on size |
Payback period (electric water heater) | 4 to 9 years | Time to recover investment costs with a heat exchanger system |
Payback period (gas water heater) | At least 12 years | Time to recover investment costs with a gas water heater and heat exchanger |
Payback period sensitivity | 2 to 6 years | Reduced payback period with increased energy prices (2 years for electric, 6 years for gas heaters) |
You notice that these systems not only cut energy waste but also offer a clear financial return, especially as energy prices rise. Properly designed heat exchangers control pressure losses and auxiliary power consumption, so you get the most out of every unit of fuel or electricity.
Cost Savings and Sustainability
Lower Utility Bills
You benefit from lower utility bills when you integrate heat exchanger heating into your building. Ground source heat pump (GSHP) systems, for example, deliver cost-effective heating and cooling across many climates. Hybrid GSHP systems further reduce installation costs by shortening the ground heat exchanger length and balancing energy sources. You see the savings in both upfront capital costs and ongoing energy expenses.
- GSHP systems provide cost-effective heating and cooling compared to conventional methods.
- Hybrid GSHP systems show the lowest lifecycle total cost per unit of thermal load.
- Reducing drilling length for ground heat exchangers lowers upfront costs.
- Hybrid configurations enhance system viability and long-term savings.
Reduced Greenhouse Gas Emissions
You also contribute to a more sustainable future. GSHPs and hybrid systems offer higher coefficients of performance and lower carbon emissions than traditional heating methods. When you factor in carbon taxation, the savings-to-investment ratio improves by up to 60%. Sustainability reports confirm that integrating these systems leads to significant reductions in both energy use and greenhouse gas emissions.
- GSHPs have higher capital costs but deliver lower carbon emissions.
- Economic benefits increase with carbon taxation and environmental incentives.
- Carbon payback periods for GSHP systems can be less than one year, depending on climate and configuration.
Enhanced Safety and Comfort
Preventing Cross-Contamination
You protect your indoor environment by using heat exchanger heating. The design keeps the heating medium and the air you breathe separate, which prevents harmful gases or contaminants from entering your living space. This separation is critical for maintaining healthy indoor air quality, especially in systems that use combustion or industrial heat sources.
Managing High Temperatures Safely
You also enjoy a safer and more comfortable home. Research shows that using advanced heat exchangers with nanofluids and optimized flow conditions can improve heat transfer performance by up to 73%. These improvements help regulate indoor temperatures more precisely. In thermally activated building systems, increasing the cooling water inlet velocity can lower indoor temperatures by about 3°C. This precise control over surface and air temperatures enhances comfort and reduces the risk of overheating.
By optimizing flow parameters and heat transfer surfaces, you maintain a stable and comfortable indoor environment while protecting against temperature extremes.
Risks and Inefficiencies Without Heat Exchanger Heating
When you operate a heating system without a properly designed heat exchanger, you expose yourself to significant risks and inefficiencies. These issues affect your energy bills, safety, and the long-term reliability of your equipment.
Energy Loss and Increased Costs
Direct Heat Loss
Without a heat exchanger, your system cannot efficiently transfer heat from the energy source to the target medium. Heat escapes into the environment instead of warming your space. This direct loss means you need to run your system longer to achieve the same comfort level. You waste valuable energy, and your heating costs rise as a result.
Increased Fuel Consumption
To compensate for lost heat, your system burns more fuel or uses more electricity. This increased consumption not only drives up your utility bills but also puts extra strain on your equipment. Over time, you face higher operational costs and a larger carbon footprint. Inefficient systems contribute to unnecessary greenhouse gas emissions, which harm the environment and may lead to regulatory penalties.
Safety Hazards
Exposure to Harmful Gases
A missing or faulty heat exchanger can allow dangerous gases, such as carbon monoxide, to enter your living or working space. Proper separation of combustion gases from the air you breathe is essential for your health. When this barrier fails, you risk exposure to toxic substances that can cause serious illness or even death.
System Overheating
Heat exchangers help regulate temperatures within safe limits. Without this control, your system can overheat. Overheating increases the risk of fires, equipment damage, and sudden breakdowns. In severe cases, catastrophic failures can occur.
The 2010 Tesoro Anacortes Refinery incident demonstrates the dangers of inadequate heat exchanger design. A shell and tube heat exchanger ruptured, causing an explosion and fire that resulted in seven fatalities. Investigations by the US Chemical Safety Board revealed that such failures can happen even after a few months of service. These incidents often lead to explosions, toxic releases, and significant plant damage.
- Shell and tube heat exchangers fail more frequently than other process equipment.
- Failures can result in production loss, injuries, and fatalities.
- Safety studies recommend using Quantitative Risk Assessment (QRA) and Hazard and Operability Analysis (HAZOP) to identify and mitigate risks.
- Inherently Safer Design (ISD) strategies and new safety indices help prevent these hazards when applied early in the design process.
Reduced System Longevity and Reliability
When you operate without a reliable heat exchanger, your system experiences more wear and tear. Components must work harder to deliver the required heat, which accelerates aging and increases the likelihood of breakdowns. Frequent repairs and unexpected failures disrupt your comfort and productivity. Over time, you face higher maintenance costs and may need to replace your system sooner than expected.
Regular safety assessments and design improvements protect your investment and ensure your heating system operates safely and efficiently for years to come.
Identifying and Addressing Heat Exchanger Heating Failure
Warning Signs of Failure
Unusual Noises
You should pay close attention to any new or strange sounds coming from your heating system. Banging, popping, or rattling noises often signal metal fatigue or cracks forming in the heat exchanger. These sounds may result from thermal expansion and contraction, which weaken the metal over time. If you hear these noises, you need to investigate further, as they can indicate early-stage failure.
Reduced Heating Performance
A drop in heating performance provides another clear warning sign. You might notice that your system struggles to maintain set temperatures or produces uneven heating throughout your space. Insufficient hot air, longer run times, or cold spots often point to a compromised heat exchanger. Changes in furnace flame color—from blue to yellow or orange—also suggest improper combustion, possibly caused by air intrusion through cracks. Soot or corrosion buildup around the unit further confirms incomplete combustion and potential damage.
ヒント If your carbon monoxide alarm activates, treat it as an urgent warning. Cracks in the heat exchanger can allow toxic gases to escape, posing immediate health risks.
To identify these issues early, you should monitor key performance indicators such as pressure drops, flow rates, and outlet temperatures. Tracking these variables helps you detect fouling, blockages, or leaks before they escalate.
Safety Risks of a Faulty Heat Exchanger
A faulty heat exchanger exposes you to serious safety hazards. Cracks and leaks can allow carbon monoxide and other toxic gases to enter your living or working environment. Even small defects may go unnoticed but still cause dizziness, nausea, or life-threatening poisoning. Mechanical and chemical stresses—such as corrosion, scaling, and vibration—can accelerate deterioration, increasing the risk of catastrophic failure. In severe cases, leaks or ruptures may lead to fires, explosions, or structural damage.
Research shows that corrosion and erosion, especially in areas with water accumulation or suspended solids, create cavities and weaken tube walls. These conditions make leaks more likely and threaten operational safety. Proper ventilation, timely repairs, and regular inspections are essential to prevent these risks.
Importance of Regular Maintenance
You can prevent most failures by following a structured maintenance plan. Regular inspections—during operation, shutdowns, or overhauls—help you catch problems early. Industry standards like ASME and NBIC recommend using non-destructive testing methods, such as ultrasonic or eddy current testing, to detect hidden defects without damaging equipment. Well-trained and certified inspectors ensure reliable results.
Keep detailed records of all maintenance activities, repairs, and replacements. Accurate documentation supports compliance, helps you plan future work, and extends equipment lifespan. Routine cleaning, leak checks, and pressure monitoring further reduce the risk of breakdowns. Neglecting maintenance allows dirt and debris to accumulate, restricting airflow and causing overheating. Overheated exchangers may crack, leading to dangerous gas leaks.
注: Annual professional inspections and the use of carbon monoxide detectors provide an extra layer of safety. If you discover a cracked heat exchanger, replace it immediately to protect your health and property.
Selecting the Right Heat Exchanger Heating Solution
Key Factors to Consider
Choosing the right heat exchanger for your heating system requires careful evaluation of several technical and operational factors. You need to match the equipment to your building’s needs and the characteristics of your heating application.
System Size and Capacity
You must ensure that your heat exchanger matches the heat load and fluid flow rates of your system. Oversizing or undersizing leads to inefficiency, wasted energy, or even equipment damage. Uniform fluid distribution and optimized flow velocities help prevent hotspots, fouling, and erosion. When you select the right size, you maintain consistent heat transfer and extend the life of your system.
The table below compares common heat exchanger types based on expert evaluations:
Criteria | Plate-and-Frame Heat Exchanger | Shell-and-Tube Heat Exchanger | Scraped-Surface Heat Exchanger |
---|---|---|---|
Heat Transfer Efficiency | High (up to 5x shell-and-tube) | ミディアム | ミディアム |
Footprint | Smallest, space-saving | Largest | ミディアム |
Ease of Maintenance | Easy plate access | More labor-intensive | High maintenance cost |
Capacity Adjustment | Modular, easy to expand | Fixed at installation | Limited flexibility |
Capital Expense | Lowest | Low, less efficient | Highest |
Operating Pressure | Low pressure | Handles high pressure | Handles high pressure |
Use with Particulates | Poor | Good to excellent | Excellent |
Fouling Potential | Moderate, easy to clean | Lower, easy to clean | High, harder to clean |
Expandability | Excellent modularity | Limited | Limited |
You see that plate heat exchangers offer high efficiency and flexibility, making them ideal for space-limited or modular systems. Shell-and-tube designs work well for high-pressure or particulate-laden fluids. Scraped-surface types handle viscous or challenging fluids but come with higher costs.
Type of Heating Medium
The properties of your heating medium—such as viscosity, particulate content, and corrosiveness—directly affect your choice. For low-to-medium viscosity fluids, plate heat exchangers provide excellent performance. If your system uses fluids with particulates or operates under high pressure, shell-and-tube or scraped-surface models are more suitable. You should also consider the compatibility of fluids with exchanger materials to prevent corrosion or degradation. Regular fluid analysis and timely replacement help maintain efficiency and protect your investment.
ヒント Proper insulation using materials like fiberglass or mineral wool minimizes heat loss and improves energy efficiency. Both external and internal insulation stabilize temperatures and protect your system from environmental influences.
Professional Assessment and Installation
You benefit from a professional HVAC assessment before installation. Certified technicians identify the best solution for your needs and address safety concerns, such as carbon monoxide leaks. They use detailed checklists to inspect for cracks, soot buildup, and abnormal noises. These inspections help you catch early signs of trouble, maintain efficiency, and comply with warranty or insurance requirements.
A thorough installation process includes:
- Tagging each heat exchanger with location, type, and model for easy identification.
- Hydrostatic pressure testing to verify integrity and detect leaks.
- Visual inspections with borescope imaging to assess scale buildup.
- Measuring leak volumes and temperatures to calculate energy losses.
- Evaluating thermal efficiency to ensure effective heat transfer.
- Documenting valve status and tube bundle condition for ongoing monitoring.
Regular maintenance schedules and cleaning procedures keep your system running safely and efficiently. By working with professionals, you ensure your heat exchanger delivers reliable performance and long-term value.
The Future of Heat Exchanger Heating
Advances in Heat Exchanger Technology
You will see rapid innovation shaping the next generation of heating systems. Manufacturers now focus on making heat exchangers smarter, lighter, and more efficient. Many new models feature sensors and IoT connectivity, allowing you to monitor performance in real time and predict maintenance needs before problems arise. This digital integration helps you reduce downtime and extend equipment life.
You benefit from miniaturized and lightweight designs, which fit into compact spaces without sacrificing performance. Companies use sustainable materials like recycled aluminum and copper, reducing environmental impact and supporting circular economy goals. Advanced plate-fin and microchannel heat exchangers deliver higher thermal performance and improved compactness, making them ideal for modern buildings.
Smart controls, data analytics, and automation now play a key role in optimizing system efficiency and reliability.
Industry leaders such as Alfa Laval, SPX Flow, and Carrier invest heavily in research and development. They expand their product lines and acquire new technologies to stay ahead. The market grows as stricter environmental regulations, urbanization, and demand for energy-efficient solutions drive adoption. You may face challenges such as high initial costs and regulatory complexity, but ongoing innovation continues to address these barriers.
The table below highlights a recent comparison between two advanced heat exchanger types:
パラメータ | Heat Pipe Heat Exchanger (THEX) | Rotary Regenerative Heat Exchanger (RHEX) | Comparative Advantage |
---|---|---|---|
Effectiveness | Baseline | 24.7% lower than THEX | THEX is 24.7% more effective |
Fan Power Requirement | Baseline | ~45 times higher | THEX uses much less fan power |
Mass | Baseline | ~16 times heavier | THEX is significantly lighter |
Material Cost | Baseline | ~4 times higher | THEX is more cost-effective |
You can see that heat pipe heat exchangers offer clear advantages in efficiency, weight, and cost, making them a strong choice for future heating applications.
Role in Sustainable and Green Heating Solutions
You play a vital role in advancing sustainability when you choose modern heat exchangers. Life cycle assessments show that eco-designed heat exchangers improve energy efficiency and reduce greenhouse gas emissions throughout their lifespan. These systems integrate seamlessly with renewable energy sources, such as geothermal and solar, to further lower your carbon footprint.
Ground source heat pumps (GSHPs) use geothermal heat exchangers to tap into stable underground temperatures. By doing so, you achieve significant reductions in carbon emissions compared to traditional heating systems. GSHPs help preserve natural resources and decrease reliance on fossil fuels. Government incentives and ongoing technological improvements make these systems more accessible and efficient for you.
- GSHPs adapt to various climates and offer long-term savings, even with higher upfront costs.
- Environmental impact tools, like life cycle analysis, help you measure the green benefits of your heating system.
- Adoption of GSHPs supports job creation in the renewable energy sector and raises environmental awareness in your community.
- Future developments promise even greater sustainability and efficiency.
By selecting advanced heat exchangers and integrating them with renewable energy, you support a cleaner, more sustainable future for everyone.
You secure reliable, efficient heating when you choose a quality heat exchanger for your system. By recovering over 7 million Btu of heat energy annually, you reduce fuel use and save hundreds of dollars each year. Advanced optimization methods help you balance investment and operating costs, ensuring long-term value. Neglecting this component leads to higher expenses and safety risks. For dependable comfort and cost savings, a well-designed heat exchanger remains essential.
よくあるご質問
What does a heat exchanger do in a heating system?
A heat exchanger transfers heat from one fluid to another without mixing them. You use it to move energy efficiently, which helps you save fuel and maintain safe indoor air quality.
How often should you maintain your heat exchanger?
You should schedule professional maintenance at least once a year. Regular inspections help you catch leaks, corrosion, or blockages early. This routine keeps your system safe and efficient.
Can a heat exchanger improve energy efficiency?
Yes. You increase energy efficiency by maximizing heat transfer and reducing waste. Modern heat exchangers help you lower utility bills and minimize environmental impact.
What are the signs of a failing heat exchanger?
Look for these warning signs:
- Unusual noises
- Reduced heating output
- Soot or corrosion
- Changes in flame color
If you notice any, contact a professional immediately.
Is it safe to repair a cracked heat exchanger yourself?
No. You should never attempt to repair a cracked heat exchanger on your own. Only certified technicians have the tools and expertise to ensure safe repairs and prevent dangerous gas leaks.
Which type of heat exchanger suits residential heating best?
Plate and finned tube heat exchangers work well for most homes. You benefit from their compact size, high efficiency, and easy maintenance. Always consult a professional to match the right type to your system.
How does a heat exchanger prevent harmful gas exposure?
A heat exchanger keeps combustion gases separate from indoor air. This design protects you from carbon monoxide and other toxic substances, ensuring a safe and healthy environment.