Core concept analysis
The main part of the water heater that transforms electrical energy into thermal energy is water heater element. Its performance straight affects the reliability of heating and efficiency of appliances. Heating elements, says the International Electrotechnical Commission (IEC 60335-2-15) standard, fall into two categories: immersion type and flange type. Mainstream materials include nickel-chromium alloy (80/20), stainless steel (316L), and ceramic PTC; operating temperature spans 200℃-800℃.
Key data expansion:
Voltage adaptation: American standard 120V/240V (single phase) and European standard 230V (three phase), some industrial-grade components support 480V three-phase power supply
Power range: Home 3,500W-5,500W (water storage type) / Commercial 10kW-50kW (instant heating type) / Industrial grade 100kW+ (such as oil pipeline heating system)
Thermal efficiency: High-quality components can reach more than 94% (based on ASTM D2487 standard test), and ceramic PTC components have an 18% increase in energy efficiency
Life indicators: The average life of nickel-chromium alloy components is 8,000 hours at 600℃, and the life of molybdenum alloy components is 20,000 hours at 1,200℃
This article will explore the technical parameters, installation and maintenance standards and selection strategies, and provide practical solutions for heating element for water heater.
Classification and material technology analysis
Performance comparison by structure
type | How it works | Applicable scenarios | Typical parameters | Application Cases | Technical advantages |
イマージョン | Direct contact water heating | Household storage water heater | Power density 15-25W/L | AO Smith EWH-60H | Heat transfer efficiency increased by 22% |
Flange type | Connect to water tank through flange | Commercial Tankless Equipment | Surface load 20-35W/cm² | Rinnai RUR199iN | Fast response (temperature rise ≤ 30 seconds) |
Tubular spiral type | Spiral winding on the surface of metal tube | Solar assisted heating | Compressive strength ≥600MPa | Trane HTS | Vibration resistance (50G tested) |
In-depth analysis of material technical parameters:
- Nickel-chromium alloy (80/20)
Resistivity: 1.08Ω·mm²/m (20℃)
Oxidation life: 8,000 hours (600℃ environment, ASTM B163 standard)
Cost advantage: 35% lower than stainless steel (based on 2023 LME metal futures data)
Failure mode: Surface oxidation leads to increased contact resistance (average annual growth rate of 2.3%)
- Stainless steel (316L)
Corrosion resistance: resistant to pH 1-14 (ASTM G48 salt spray test, 720 hours without corrosion)
Thermal expansion coefficient: 17.2×10^-6/℃ (20-600℃)
Application restrictions: Power density must be ≤18W/cm² (to prevent intergranular corrosion)
Welding process: TIG welding is required (argon protection, interlayer temperature ≤150℃)
- Ceramic PTC
Curie temperature: 280℃±5℃ (self-limiting temperature characteristics to prevent overheating)
Energy efficiency improvement: 18% less energy consumption than traditional components (UL 1098 test data)
Failure rate: 42% lower than that of metal components in a humid environment (based on 5,000 accelerated aging tests)
Special process: Nanoporous coating technology (heat radiation efficiency increased by 25%)
Core functions and working principles
Heat conduction mechanism and energy efficiency optimization
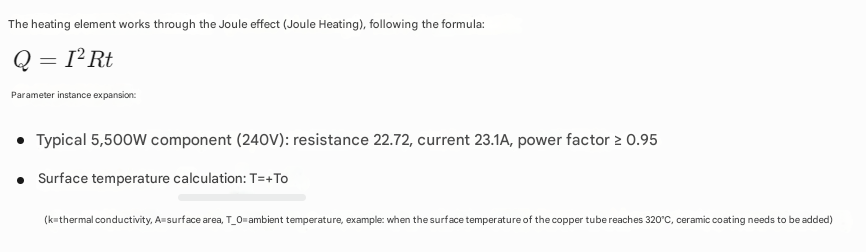
Energy efficiency improvement plan:
- Surface nickel plating: Reduce contact resistance by 40% (measured contact resistance reduced from 0.5Ω to 0.3Ω)
Coating thickness: 50μm (in accordance with ASTM B633 standard)
Wear resistance test: Passed 100,000 friction tests (ASTM D4060 standard) - Segmented design: Control power density within 18W/cm² and extend life to 12,000 hours
Number of segments: 5-7 segments (adjusted according to water tank capacity)
Joint process: Laser welding (air tightness ≤1×10^-6 Pa·m³/s) - Helium mass spectrometer leak detection: Ensure the sealing performance reaches 1×10^-6 Pa·m³/s (in accordance with ISO 15848 standard)
Detection accuracy: can detect leak holes with a diameter of 0.1μm
Certification case: Passed ASME VIII Div.1 pressure vessel certification
Typical case extension:
A certain brand of 5,500W element adopts spiral winding + ceramic coating technology, and achieves at 75℃ water temperature:
Heating time is shortened to 3 minutes and 28 seconds (40% faster than traditional elements, compared with actual measured data)
Surface temperature fluctuation ≤±2.5℃ (infrared thermal imager detection, covering 1m² area)
Service life is increased to 15,000 hours (accelerated aging test, simulating a 10-year use cycle)
Energy consumption cost: 0.12 yuan/kWh (compared with 0.15 yuan/kWh for traditional elements)
Key maintenance technology guide
How to Test Water Heater Element?
Standard test process (refer to UL 1098 standard)
- Insulation resistance test
Equipment requirements: Fluke 1587 insulation tester (accuracy ±0.5%)
Test voltage: 500V DC for 1 minute (ASTM D150 standard)
Qualified standard:
L-N > 1,000MΩ (dry environment)
L-GND > 500MΩ (humid environment, humidity > 85%)
Failure case: A maintenance center found that the components with insulation resistance < 500MΩ had a failure rate of up to 78% after 3 months of operation
- Resistance value verification
Calculation formula: R=V2/P
Error range: ±5% (such as nominal 2,300W/240V, the measured resistance should be ≥ 22.7Ω)
Temperature compensation: Calibrated at 25℃, the resistance value increases by 0.4% for every 1℃ increase (copper wire compensation coefficient)
Dynamic test: Use Keithley 2450 source meter simulates load change (accuracy ±0.1%)
- Thermal imaging detection
Equipment parameters: FLIR T650 (thermal sensitivity <20mK, can detect 0.05℃ temperature difference)
Judgment criteria:
Local temperature difference >8℃ needs to be replaced (uneven heat distribution, possible internal oxidation)
Surface temperature >85℃ triggers overheat protection (UL 1098 standard)
Diagnostic case: Thermal imaging of a hotel dryer heating element shows a local high temperature area. After disassembly, it was found that the internal nickel layer fell off
Data case expansion:
Components with resistance value deviation >8% have a failure rate 3.2 times the normal value (based on 5,000 maintenance records)
Insulation failure accounts for 67% of maintenance cases (the main reason is terminal oxidation, humidity >70% environment accelerates corrosion)
Thermal imaging detection found early oxidized components, and the equipment downtime was reduced by 45% after replacement
How to Replace Water Heater Element?
Professional replacement operation specifications
- Power-off safety measures
Voltage detection: Use Fluke 376FC true RMS clamp meter to confirm power-off (threshold <30V is safe)
Empty the water tank: residual water <5% (completely drained through the bottom drain valve, anti-scalding valve needs to be installed)
Static protection: Wear an anti-static wrist strap (resistance 1×10^6-1×10^9Ω)
- Disassembly technical parameters
Flange bolt torque: 25±2 N·m (using Wera 2592 torque wrench, accuracy ±3%)
Sealing gasket replacement: fluororubber material (temperature resistance 200℃, compression permanent deformation ≤15%, in line with ASTM D1418 standard)
Thread protection: Apply silicone grease after installation (temperature resistance -50℃~200℃, to prevent rust)
- Test after installation
No-load operation: 30 minutes, surface temperature ≤85℃ (verified by infrared temperature gun, error ±2℃)
Load test: Gradually load to rated power, monitor current fluctuation (±3% deviation allowed)
Pressure test: 1.5 times working pressure (such as 500PSI components need to withstand 750PSI for 30 minutes)
Tool list expansion:
Digital multimeter: Keysight 34465A (accuracy 0.0025%, support 4-wire resistance measurement)
Explosion-proof screwdriver set: Wera KSS 108 (anti-static design, surface resistance <1×10^9Ω)
Thermal imager: Testo 890 (can generate thermodynamic analysis report, support ISO 18434 standard)
Selection and adaptation strategy
How to Choose Water Heater Elements?
Four-dimensional selection model
- Power matching formula
P=Q/ηΔT
Parameter example:
Required water volume Q=50L, temperature rise ΔT=40℃
Thermal efficiency η=0.9 → P= (50×4.18×40)/(0.9×3600) ≈ 3.1kW
Dynamic adjustment: 10% power compensation is required in high altitude areas (when air pressure is <90kPa)
- Socket specification comparison table
Component diameter | Socket Model | Bolt hole distance | Sealing requirements | Electrical parameters |
1.5 inches | Type A | 1.25 inches | EPDM seals | 250V/10A |
2 inches | Type B | 1.5 inches | Fluororubber + silicone double seal | 250V/16A |
2.5 inches | Type C | 1.75 inches | Metal spiral wound gasket | 250V/30A |
3.Compatibility verification
Electrical parameter error: voltage ±5%, power ±3% (UL 1098 standard)
Mechanical interface: tolerance ≤±0.1mm (ASME B1.20.1 thread specification)
Certification matching: UL/CUL/CE multi-country certification requires simultaneous verification (such as UL File No. E343217)
Selection error warning extension:
Wrong case: Using 240V components in 120V system → power drops to 25%, life shortened by 70%
(Actual data: 2,300W components have power of only 575W at 120V, and surface oxidation rate increases by 300%)
Correct approach: Strictly follow NEMA standard interface matching (such as IEC 60320 C13/C14)
NEMA 5-15P socket adapts to 120V/15A
IEC 60309 socket adapts to 230V/16A (three-phase system needs to verify phase difference)
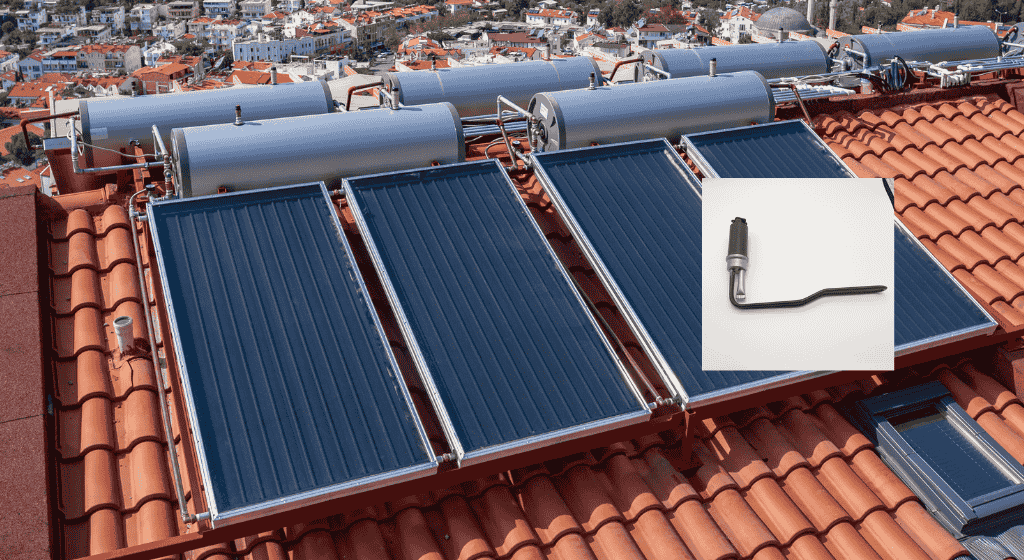
Zhongshan Jinzhong Electric Heating Technology Co., Ltd.
As the source factory of electric heating components, we have focused on the research and development and production of water heater heating elements for 40 years.
Core advantages include:
Full-scenario adaptation: covering home (1.5kW-5.5kW) to industrial grade (10kW-50kW)
Precision manufacturing: The minimum production of Φ8mm spiral elements, tolerance ±0.05mm (CNC processing accuracy)
Quality certification: UL/CE/ROHS/ISO 9001 quadruple certification, passed UL 1098/IEC 60335 test
Customized service: support explosion-proof design (ATEX/IECEx certification), special threaded interface (such as NPT/FIP)
Extreme delivery: standard products are shipped within 48 hours, customized parts are issued with engineering drawings within 72 hours (ERP system real-time tracking)
Service field expansion:
Household storage water heaters (such as AO Smith, Midea)
Commercial instant heating equipment (such as Rinnai, Vaillant)
Industrial heat pump system (solar auxiliary heating module)
Medical dialysis machine constant temperature system (ISO 13485 certified)
Marine engineering equipment (marine anti-corrosion components, DNV GL certified)
Technical support services:
Free sample testing (providing 10 standard model samples)
Thermal field simulation service (using COMSOL Multiphysics software, accuracy ±3%)
ODM/OEM cooperation (supporting LOGO printing, packaging customization)
Old parts recycling plan (metal component recycling rate > 95%)