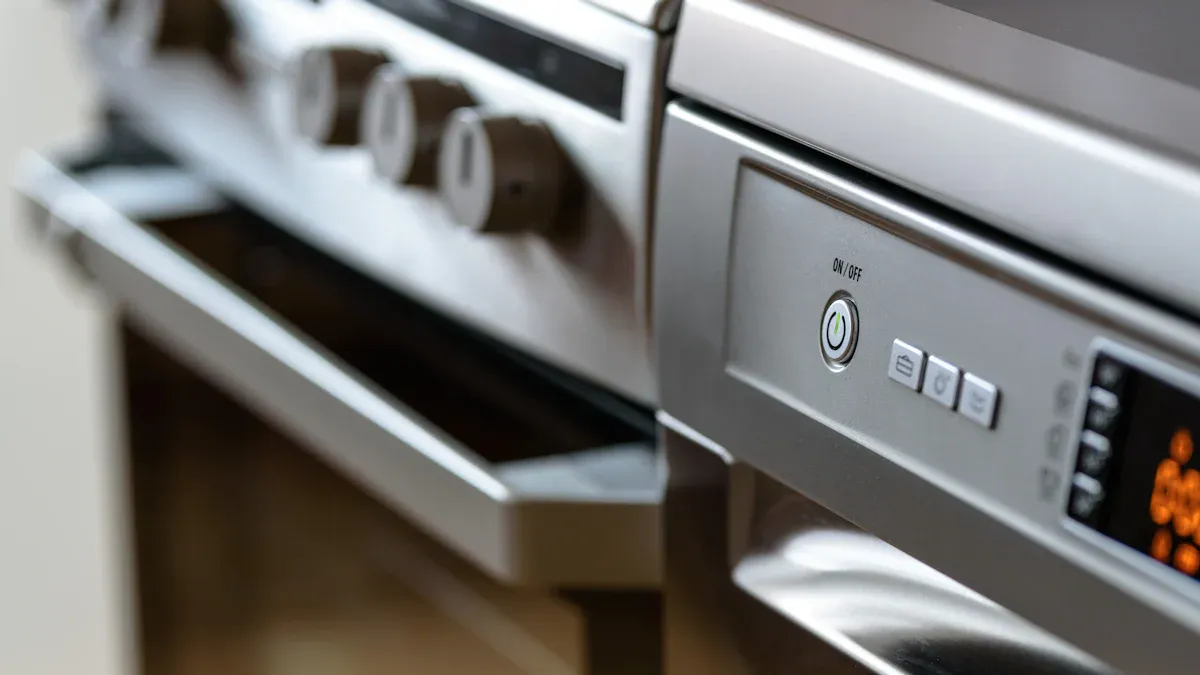
A élément chauffant definition refers to the part in appliances that converts electrical energy into heat. This process enables electric heating for daily tasks such as cooking, drying, or warming water. Many household devices, including heating tubes and the élément chauffant de l'eau in dishwashers, rely on this technology. Ceramic heating elements deliver more heat per watt than traditional types, which improves energy efficiency and lowers costs.
Consistent electric heating ensures optimal performance and reduces unnecessary energy use.
Statistic Description | Value/Result |
---|---|
Energy absorbed by tableware as heat in dishwasher | 35.7% of consumed energy |
Energy consumption reduction by increasing insulation thickness from 20mm to 40mm | 8.4% reduction |
Heating Element Basics in Household Appliances
What Is a Heating Element?
A heating element serves as the core component in electric heating devices. It transforms electrical energy into heat through a process called Joule heating. This process relies on the resistance of the material within the heating element. When an electric current passes through, the resistance causes the material to heat up, releasing thermal energy. This principle forms the foundation for most types of electric heating used in home appliances.
Material science research defines heating elements as substances engineered to convert electrical energy into thermal energy efficiently. For example, molybdenum disilicide (MoSi₂) demonstrates robust oxidation resistance at temperatures up to 1800°C by forming a protective silica layer. Silicon carbide (SiC) offers excellent thermal conductivity and mechanical strength, withstanding rapid temperature changes and corrosive environments. These advanced materials support the reliability and durability of electric heating devices in both residential and industrial settings.
Heating elements come in various types, each designed for specific applications. Some use metal alloys, while others rely on ceramics or carbon-based materials. The choice of material and design affects the efficiency, safety, and lifespan of the electric heater. Manufacturers select materials based on their ability to withstand high temperatures, resist oxidation, and provide consistent heat output.
Common Heating Elements Found at Home
Home appliances rely on several types of heating elements to perform everyday tasks. The most common electric heating devices include ovens, toasters, water heaters, and clothes dryers. Each appliance uses a specific type of heating element to deliver the required heat efficiently.
- Tubular heaters: These elements appear in water heaters, dishwashers, and electric ovens. Their design allows for even heat distribution and durability.
- Open coil heaters: Toasters and space heaters often use open coil elements. These provide rapid heating and are easy to replace.
- Ceramic heating elements: Space heaters and hair dryers frequently use ceramic elements. These offer improved energy efficiency and safety.
- Quartz heating elements: Infrared heaters and some electric fireplaces use quartz elements. These deliver focused, radiant heat.
- PTC (Positive Temperature Coefficient) elements: Modern electric heating devices, such as fan heaters, use PTC elements for self-regulating temperature control.
The prevalence of heating elements in home appliances reflects their essential role in modern living. The global market for heating elements reached USD 10.01 billion in 2023 and is projected to grow to USD 13.81 billion by 2030, with a compound annual growth rate (CAGR) of 4.7%. The home appliance industry represents the largest growing application segment, driven by technological advances, smart home trends, urbanization, and increasing disposable income. Tubular heaters remain the most widely used product category in residential sectors.
Statistic/Insight | Value/Description |
---|---|
Market value (2023) | USD 10.01 billion |
Projected market value (2030) | USD 13.81 billion |
Compound Annual Growth Rate (CAGR) (2024-2030) | 4.7% |
Largest growing application segment | Home appliance industry |
Key growth drivers for home appliance segment | Technological advances, smart home trends, urbanization, increasing disposable income |
Largest growing product category | Tubular heaters, widely used in residential sectors including home appliances |
Note: The diversity of heating elements in electric heating devices ensures that each appliance can meet specific performance and safety requirements. Selecting the right type of heating element improves energy efficiency and extends the lifespan of the appliance.
How Heating Elements Work: The Principle of Electric Heating
Joule Heating and Electrical Resistance
Conversion of Electrical Energy to Heat
Electric heating relies on a simple but powerful process. When an electric current passes through a heating element, the material resists the flow of electrons. This resistance causes the electrical energy to convert into heat. The working principle of éléments chauffants follows Joule’s first law, which states that the heat produced equals the resistance multiplied by the square of the current (P = I²R). Early experiments demonstrated this principle by submerging a wire in water and connecting it to a battery. As current flowed, the water’s temperature increased, providing direct evidence of heat generation. This process forms the foundation for all types of electric heating, from a basic heater to advanced appliances.
The Role of Resistance in Heating Elements
Resistance plays a critical role in the performance of heating elements. Materials with higher resistance generate more heat when current flows through them. The amount of heat produced depends on the material’s properties, such as resistivity and geometry. Manufacturers select specific alloys for heating elements to achieve the desired temperature and efficiency. For example, a heater in a toaster uses a wire with high resistance to reach the necessary temperature quickly. Consistent resistance ensures that electric heating devices operate safely and reliably. The temperature of the heating element must remain stable to prevent overheating and maintain appliance longevity.
Heat Transfer Methods in Appliances
Conduction, Convection, and Radiation Explained
Electric heating elements transfer heat to their surroundings using three main methods: conduction, convection, and radiation. Each method plays a unique role in household appliances.
- Conduction occurs when heat moves directly from the heating element to another solid object, such as a pan on a stove. The temperature difference drives this transfer, making conduction essential for cooking appliances.
- Convection involves the movement of heated air or liquid. In a space heater, the élément chauffant warms the air, which then circulates throughout the room. This method distributes heat evenly and efficiently.
- Radiation allows the heating element to emit infrared energy, which travels through space and heats objects directly. Quartz heaters and some ovens use radiation to achieve rapid temperature increases.
Studies comparing different cooktops and cookware materials show that the efficiency of heat transfer varies widely. For example, induction cooktops often outperform electric coil and gas stoves in energy efficiency. The type of electric heating and the material of the pan both influence how quickly and evenly heat transfers. Understanding these methods helps consumers and manufacturers choose the best heater for each application, optimizing both temperature control and energy use.
Tip: Selecting the right type of electric heating and cookware can improve energy efficiency and reduce cooking times.
Types of Heating Elements Used in Electric Heating Appliances
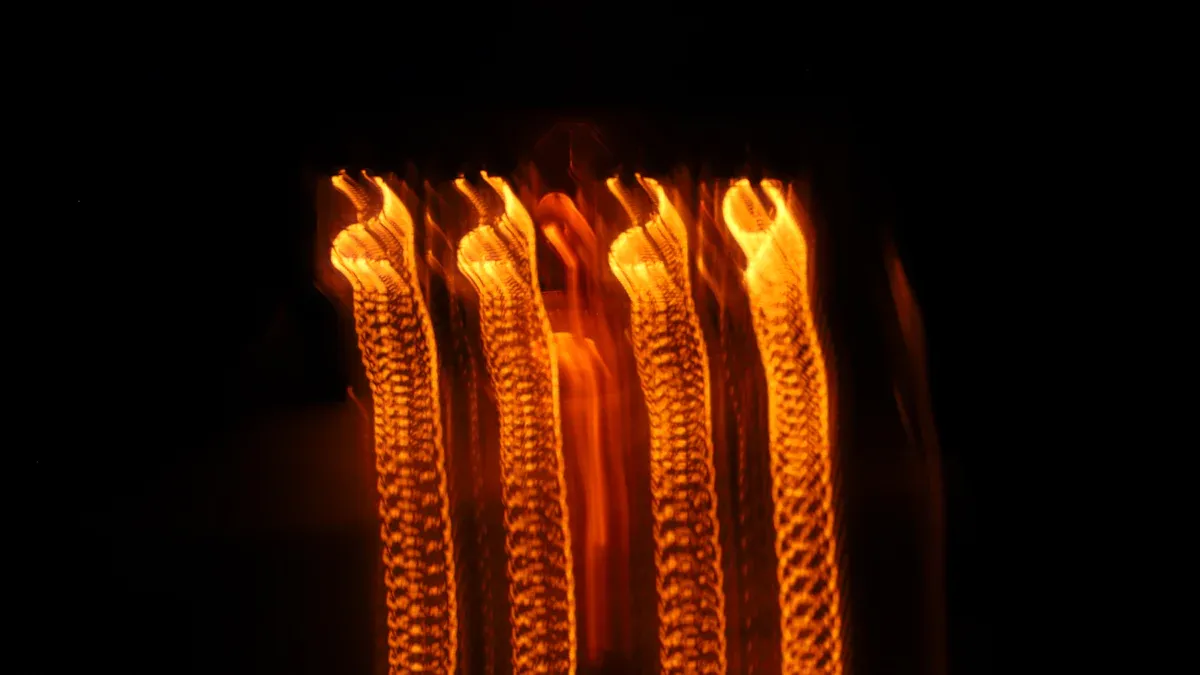
Heating elements appear in a wide range of electric heating appliances, each with unique designs and performance characteristics. The selection of the right type depends on the application, efficiency requirements, and safety considerations.
Coil and Wire Heating Elements
Coil and wire heating elements represent some of the most common types of heating elements in household and industrial appliances. Manufacturers often use high-resistance alloys such as nickel-chromium (nichrome) or iron-chromium-aluminum (FeCrAl) for these elements. These materials provide high electrical resistivity, excellent oxidation resistance, and mechanical durability. The design of heating element coils allows for efficient heat production and manageable energy consumption.
Open Coil Heating Elements
Open coil heating elements consist of resistance wire heating elements wound into coils and exposed to air. This configuration enables rapid heat transfer and quick temperature rise. Toasters, hair dryers, and space heaters frequently use open coil designs due to their fast response and ease of replacement. The open structure allows air to flow freely around the coil, maximizing heat dissipation. However, exposure to air can increase the risk of oxidation, so manufacturers select alloys that form protective oxide layers.
Enclosed Coil Heating Elements
Enclosed coil heating elements feature resistance wires encased within a protective sheath, often made of stainless steel or other corrosion-resistant materials. This design shields the coil from direct contact with air, moisture, and contaminants, improving safety and extending lifespan. Water heaters, ovens, and dishwashers commonly use enclosed coil elements. The sheath also enables the element to operate in harsh environments without degrading performance.
Performance Parameter | Coil and Wire Heating Elements Characteristics |
---|---|
Electrical Resistivity | High resistivity materials ensure efficient heat production and manageable energy consumption. |
Oxidation Resistance | Alloying elements form protective oxide layers, enhancing lifespan and performance. |
Temperature Coefficient of Resistance (TCR) | Lower TCR provides stable and predictable heating output. |
Mechanical Properties | High creep resistance, tensile strength, and ductility allow fabrication into coils and mats. |
Melting Point | High melting points enable operation at elevated temperatures. |
Surface Load | Rated in watts per square centimeter of sheath; critical for design and durability. |
Wire Temperature | Influences lifespan; lower wire temperature extends element life. |
Lifespan | Dependent on wire thickness, operating temperature, and surface load management. |
Coil and wire heating elements stand out for their stable electrical resistance, mechanical strength, and adaptability to various appliance designs. Lower surface loads and thicker wires generally increase the lifespan of these resistive heating elements.
Ribbon and Strip Heating Elements
Ribbon and strip heating elements use flat, rectangular strips of resistive material, often nichrome or FeCrAl alloys. These types of heating elements provide excellent surface contact, making them ideal for applications requiring efficient conduction. Manufacturers bolt or clamp these elements to surfaces, ensuring even heat distribution.
Testing shows that ribbon heating elements achieve a maximum steady-state temperature of 160°C within 100 seconds at a 10 V driving voltage. They heat up about three times faster than traditional Ni-Cr alloy wires. Mechanical durability remains high, with performance stable after 120 bending or twisting cycles. The broad radiation wavelength range (2.5–25 μm) makes them suitable for applications like underfloor heating and industrial drying.
Note: Ribbon and strip heating elements excel in applications where rapid heating and efficient conduction are critical.
Ceramic and Quartz Heating Elements
Ceramic and quartz heating elements belong to a class of resistive heating elements that use advanced materials for specialized applications. Ceramic elements, often made from positive thermal coefficient (PTC) materials, self-regulate their temperature, enhancing safety and energy efficiency. Quartz heating elements use a resistance wire encased in a quartz tube, emitting infrared radiation for direct heating.
These types offer several advantages:
- High maximum operating temperatures
- Excellent oxidation resistance
- Stable performance in harsh or corrosive environments
Ceramic and quartz heating elements appear in space heaters, hair dryers, and infrared heaters. Their ability to deliver focused, radiant heat makes them valuable for both residential and industrial uses.
Tip: Selecting the appropriate type of heating element ensures optimal appliance performance, safety, and energy efficiency.
PTC Heating Elements
PTC heating elements, or Positive Temperature Coefficient heating elements, represent a modern approach to electric heating in both household and industrial applications. These elements use materials whose electrical resistance increases as temperature rises. This self-regulating property allows PTC heaters to automatically limit their maximum temperature, which enhances safety and energy efficiency.
Manufacturers often construct PTC heating elements from advanced ceramics or conductive polymers. When current flows through the element, it heats up. As the temperature climbs, the resistance increases, causing the current to decrease. This process naturally stabilizes the temperature without the need for complex control systems. The result is a heating element that can prevent overheating and reduce the risk of fire or damage to the appliance.
PTC heating elements offer several operational advantages:
- Self-regulation: The element adjusts its power output based on temperature, providing consistent and safe heating.
- Energy efficiency: As the element reaches its target temperature, it draws less power, reducing overall energy consumption.
- Reliability: The simple design and lack of moving parts contribute to long service life and low maintenance requirements.
- Versatility: Manufacturers can produce PTC elements in various shapes and sizes, including flexible and ultra-thin profiles.
Recent developments in flexible PTC heating elements have expanded their use in electric mobility. For example, companies have created ultra-thin, flexible PTC heaters that fit into narrow or curved spaces, making them ideal for electric vehicle battery packs. These heaters use conductive carbon pastes with temperature-dependent resistance. As the battery warms, the heater’s resistance increases, which reduces power consumption and enhances safety. High mechanical resistance and reliability under bending stress help extend battery life, improve low-temperature operation, and enable faster recharge times. The manufacturing process also benefits the environment by using additive printing technology that produces no toxic waste.
PTC heating elements play a crucial role in maintaining optimal temperatures in electric vehicle batteries. They address challenges such as slower recharge times and reduced efficiency at low temperatures. By ensuring uniform temperature distribution, these elements help extend battery service life and improve overall performance in electric vehicles, trains, and industrial machines like forklifts and ships.
Despite their advantages, PTC heaters have operational limits. Research shows that in cold climates, PTC heaters in electric vehicles can cause significant range loss. At 20°F, a PTC heater may result in a 42.8% reduction in driving range, with much of this loss due to resistive heating inefficiency. Heat pumps offer a more energy-efficient alternative in such conditions, increasing range by up to 31%. However, PTC heaters remain popular because of their reliability and simplicity.
In industrial settings, PTC thermal collectors provide a reliable source of heat for processes like drying. These systems can supply up to 81% of the daily heat requirement, significantly reducing CO2 emissions and offering economic benefits. When combined with renewable energy sources, PTC systems further improve energy efficiency and shorten the investment return period.
Note: PTC heating elements combine safety, efficiency, and adaptability, making them a preferred choice for many modern electric heating applications. Their self-regulating nature and flexible design continue to drive innovation in both household and industrial sectors.
Materials for Heating Elements: Nichrome, Kanthal, and More
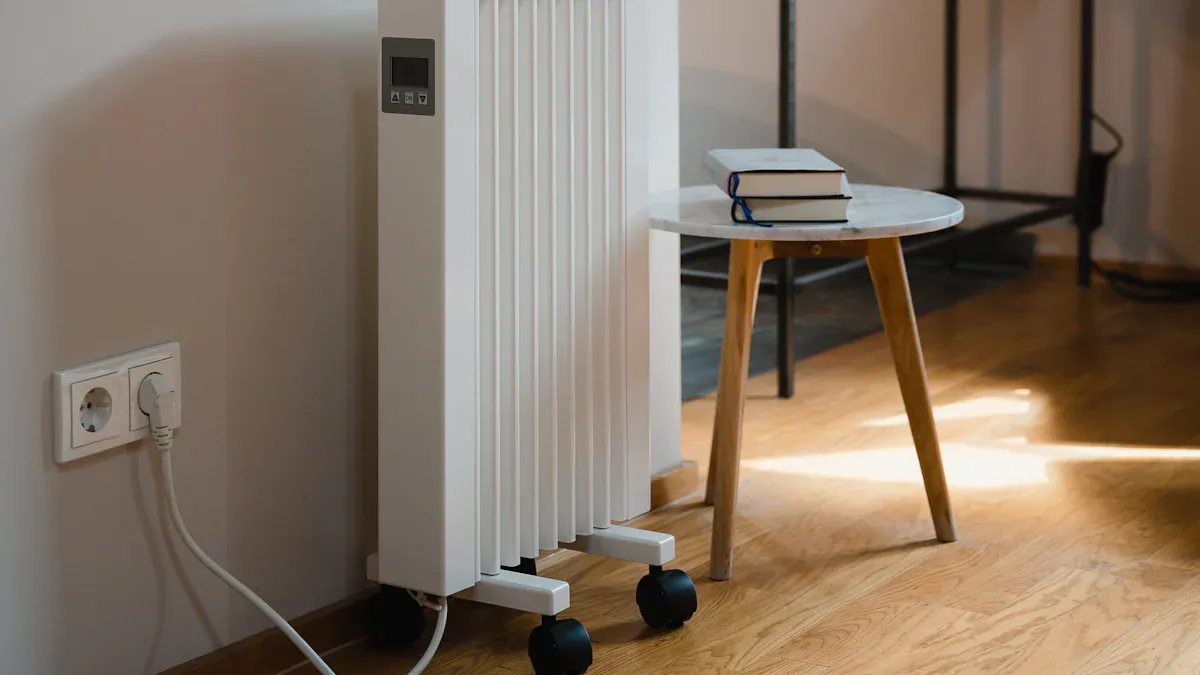
Nichrome Alloys in Heating Elements
Nichrome stands as one of the most recognized heating element materials in household and industrial appliances. Engineers select nichrome for its unique combination of high electrical resistivity, stable performance, and strong oxidation resistance. The properties of nichrome include a composition of approximately 80% nickel and 20% chromium, with trace amounts of iron, manganese, and silicon. These characteristics allow nichrome to operate efficiently at temperatures up to 1200°C, making it suitable for high-temperature applications such as tube furnaces and electric ovens.
The properties of nichrome also include the formation of a protective chromium oxide layer when heated. This layer enhances the alloy’s resistance to oxidation, which extends the lifespan of the heating element. The applications of nichrome range from toasters and hair dryers to laboratory furnaces and industrial heaters. Studies comparing nichrome to ceramic heating elements reveal that, while nichrome remains widely used, ceramics can offer faster response times and longer lifespans. However, nichrome’s higher density and heat capacity provide reliable performance in many electric heating devices.
A systematic analysis of nichrome coatings shows that oxidation can affect resistivity and phase composition, impacting both durability and efficiency. Manufacturers continue to optimize nichrome for self-regulating and high-temperature applications, ensuring it remains a staple among heating element materials.
Alloy | Composition | Resistivity (µΩ-cm) | Melting Point (°C) | Operating Temp. (°C) | Oxidation Resistance |
---|---|---|---|---|---|
Nichrome | Ni ~80%, Cr ~20%, Fe, Mn, Si | 40 | 1400 | Up to 1200 | High |
Tip: The applications of nichrome benefit from its stable electrical resistance and ability to withstand rapid heating and cooling cycles.
Kanthal and Other High-Resistance Alloys
Kanthal represents another leading choice among heating element materials. The properties of kanthal include a composition of iron, chromium, and aluminum, which enables operation at temperatures up to 1400°C. Kanthal forms a robust aluminum oxide layer on its surface, providing exceptional oxidation resistance and thermal shock stability. These properties make kanthal ideal for high-temperature applications such as industrial furnaces, kilns, and specialty ovens.
Experimental data highlights kanthal’s superior performance. For example, a pizza oven equipped with porcupine-shaped kanthal elements reached 900°C and baked a Neapolitan pizza in under 40 seconds. The design of kanthal coils increases radiant heat output and temperature uniformity. Studies also show that kanthal alloys form protective α-Al2O3 oxide scales during high-temperature use. However, repeated thermal cycling can induce stress and cracking in the oxide layer, which may affect long-term mechanical integrity.
Cupronickel, another high-resistance alloy, consists mainly of copper and nickel. The properties of cupronickel include high electrical resistivity, a melting point of 1280°C, and strong oxidation resistance. The applications of cupronickel focus on environments where moderate temperatures and corrosion resistance are essential, such as marine heating systems and some water heaters. Platinum, though less common due to cost, offers unmatched stability and oxidation resistance for specialized high-temperature applications, including laboratory and medical devices.
Alloy | Composition | Resistivity (µΩ-cm) | Melting Point (°C) | Operating Temp. (°C) | Oxidation Resistance |
---|---|---|---|---|---|
Kanthal | Fe ~72%, Cr ~22%, Al ~6% | 145 | 1500 | Up to 1400 | High |
Cupronickel | Cu ~75%, Ni ~23%, Fe, Mn | 50 | 1280 | Up to 600 | High |
Platinum | Pure Pt | 10.6 | 1768 | Up to 1700 | Very High |
Note: The heating element properties of kanthal, cupronickel, and platinum ensure efficiency, safety, and longevity in demanding environments.
Ceramic and Carbon-Based Heating Elements
Ceramic and carbon-based heating element materials have gained popularity for their advanced performance in high-temperature applications. Ceramic matrix composites (CMCs) and carbon/carbon composites deliver high strength and stability at temperatures above 1000°C. These materials use fibers such as silicon carbide or carbon, embedded in a ceramic or inorganic matrix. The result is a heating element with excellent mechanical properties and resistance to thermal shock.
A comparative analysis shows that CMCs and carbon/carbon composites require specialized, high-temperature processing and expensive fibers, which increases cost. Polysialate-based composites offer a cost-effective alternative, curing at lower temperatures and using less expensive fibers. These composites retain about 63% of their strength after exposure to 800°C and do not produce smoke, making them attractive for aerospace, automotive, and naval applications.
Aspect | Ceramic Matrix Composites | Carbon/Carbon Composites | Polysialate Composites |
---|---|---|---|
Processing Temp. | >1000°C | >1000°C | <150°C |
High Temp. Stability | Excellent | Excellent | Good |
Cost | High | High | Low |
Environmental Impact | Not specified | Potential fumes | No smoke |
Platinum also finds use in some ceramic heating elements, especially where precise temperature control and chemical resistance are required. The heating element properties of ceramics and carbon-based materials include rapid response, long lifespan, and high energy efficiency, often surpassing traditional metal alloys in demanding applications.
Block Quote: Ceramic and carbon-based heating element materials continue to expand the possibilities for efficient, durable, and environmentally friendly electric heating.
Choosing the Right Heating Element for Appliance Efficiency and Safety
Energy Efficiency in Electric Heating
Selecting the right heating element plays a crucial role in the energy efficiency of electric heating. Engineers design electric heating devices to maximize heat output while minimizing energy consumption. Proper sizing of equipment prevents oversizing, which can lead to wasted energy and higher operational costs. Programs that promote efficient sizing and straightforward incentive structures help users achieve optimal energy efficiency without unnecessary complexity.
A Multi-Criteria Decision Analysis (MCDA) framework evaluates electric heating technologies by considering energy efficiency ratings, carbon emissions per kilowatt-hour, technology readiness, installation complexity, and lifespan. Heat pumps and mechanical vapor recompression systems consistently rank highest in efficiency and reliability. These metrics guide manufacturers and consumers in choosing technologies that deliver effective temperature control and sustainable performance.
Metric Category | Description | Example/Application |
---|---|---|
Energy Efficiency | Heating elements designed to maximize heat output while minimizing energy consumption | Polymer PTC and quartz halogen elements |
Wattage Requirements | Selecting wattage based on application needs to balance heating speed and safety | High wattage for ovens; low wattage for heated seats |
Self-Regulating Safety | Polymer PTC elements increase resistance with temperature, preventing overheating | Electric radiators, heated seats |
Material Durability | Use of nickel-chromium and silicon carbide for oxidation resistance and high temperature tolerance | Industrial heating elements |
Design & Configuration | Shape, size, and placement tailored for optimal heat distribution | Tubular elements for water heaters; flat elements for griddles |
Integration Ease | Design that facilitates easy assembly and replacement, reducing costs and improving reliability | Custom-designed elements for specific appliances |
Tip: Efficient electric heating depends on matching the element’s wattage and design to the appliance’s intended use, ensuring precise temperature control and reduced energy waste.
Safety Features of Heating Elements
Safety remains a top priority in the design of electric heating elements. Engineers select materials that form protective oxide layers, such as nickel-chromium and silicon carbide, to resist oxidation and withstand high temperatures. Self-regulating elements, like polymer PTC, automatically adjust resistance as temperature rises, which prevents overheating and enhances user safety. Lowering watt density by increasing wire length or improving airflow can reduce coil temperature, extending heater life and minimizing failure risks.
Comparing copper and Incoloy heating elements highlights the importance of material choice for safety. Copper elements suit low-temperature, rapid-heating applications but require regular maintenance due to moderate corrosion resistance. Incoloy elements, with excellent corrosion resistance and high-temperature tolerance, offer greater durability and stability in demanding environments.
Factor | Copper Heating Elements | Incoloy Heating Elements |
---|---|---|
Temperature Resistance | Suitable for low to moderate temperatures (up to ~200°C) | Ideal for high-temperature applications (up to 1350°C) |
Résistance à la corrosion | Moderate; requires regular maintenance | Excellent; minimal maintenance required |
Durability | Moderate; prone to oxidation and corrosion | High; resistant to deformation and corrosion |
Note: Self-regulating and corrosion-resistant materials provide reliable temperature control and reduce the risk of overheating or failure in electric heating systems.
Durability and Lifespan Considerations
Durability and lifespan depend on both material selection and design. Alloys that form stable oxide layers, such as nickel-chromium and Incoloy, resist oxidation and thermal expansion, which extends service life. High watt density can cause excessive coil temperature, leading to premature failure. Redesigning heaters with more wire and improved airflow lowers watt density, reduces operating temperature, and increases longevity.
Manufacturers also consider ease of integration and replacement. Custom-designed elements simplify assembly and maintenance, reducing downtime and costs. In applications where temperature control and reliability are critical, durable materials and thoughtful design ensure electric heating devices operate safely and efficiently for years.
Callout: Balancing watt density, material durability, and temperature control leads to safer, longer-lasting electric heating solutions.
Matching Heating Elements to Appliance Needs
Selecting the right élément chauffant for each household appliance ensures optimal performance, safety, and energy efficiency. Engineers evaluate several factors before choosing a heating element, including the desired temperature range, the method of heat transfer, and the level of temperature control required. Each appliance presents unique demands, so manufacturers tailor heating elements to meet those needs.
Key Considerations for Matching Heating Elements:
- Operating Temperature Range: Appliances such as ovens and water heaters require elements that can reach and maintain high temperatures. In contrast, heated blankets or seat warmers need elements that operate safely at much lower temperatures.
- Temperature Control Precision: Devices like electric kettles and thermostatic irons demand precise temperature control. Engineers often select PTC or ceramic elements for these applications because these materials self-regulate and prevent overheating.
- Heat Transfer Method: The method of heat transfer—conduction, convection, or radiation—affects the choice of heating element. For example, radiant heaters use quartz or infrared elements to deliver focused heat, while convection ovens rely on enclosed coil elements for even air heating.
- Safety Requirements: Appliances exposed to moisture, such as dishwashers or water heaters, benefit from enclosed coil or sheathed elements. These designs protect the heating element from corrosion and electrical hazards.
- Durability and Maintenance: High-use appliances, such as clothes dryers, require robust elements like nichrome or kanthal alloys. These materials withstand frequent heating cycles and resist oxidation.
Tip: Matching the heating element to the appliance’s specific requirements not only improves efficiency but also extends the lifespan of the device.
Examples of Appliance-Element Pairing:
Appliance | Typical Heating Element Type | Reason for Selection |
---|---|---|
Electric Oven | Enclosed Coil (Nichrome/Kanthal) | High temperature, even heat distribution |
Hair Dryer | Open Coil (Nichrome) | Rapid heating, lightweight design |
Space Heater | Ceramic/PTC | Safe, self-regulating temperature control |
Water Heater | Sheathed Coil (Incoloy) | Corrosion resistance, moisture protection |
Infrared Heater | Quartz | Focused radiant heat, quick response |
Manufacturers also consider the ease of integration and replacement. Custom-shaped elements fit specific appliance designs, ensuring efficient heat transfer and reliable temperature control. Flexible PTC elements, for instance, adapt to curved surfaces in automotive or wearable applications.
Note: Properly matched heating elements help appliances maintain consistent temperature, reduce energy waste, and enhance user safety.
The Impact of Heating Elements on Appliance Performance
Functionality and Effectiveness
Heating elements play a central role in determining how well an appliance performs its intended function. The effectiveness of a heater depends on how efficiently it converts energy into usable heat and how consistently it maintains the desired temperature. Engineers use several operational performance metrics to evaluate these aspects. For example, Annual Fuel Utilization Efficiency (AFUE) measures the ratio of annual heat output to the total energy consumed by furnaces and boilers. A higher AFUE indicates that the heater delivers more heat for each unit of energy used. However, real-world efficiency often differs from laboratory ratings due to factors such as installation quality, house insulation, and maintenance practices.
Metric / Factor | Description | Notes / Impact on Performance |
---|---|---|
Annual Fuel Utilization Efficiency (AFUE) | Ratio of annual heat output to total annual fossil fuel energy consumed by furnaces and boilers. | Higher AFUE means more efficient heat delivery. Real-world values may differ from lab ratings. |
Oversizing Factor | Percentage by which heating system capacity exceeds estimated maximum demand. | Oversizing leads to more cycling and energy losses, reducing efficiency. |
Uniform Energy Factor (UEF) | Efficiency metric for water heaters considering usage patterns and standby losses. | Reflects real-world water heating efficiency; typical UEF ranges 50-60%. |
Oversizing a heater by 100% can reduce AFUE to the high 50s, while oversizing by 300% may drop it to as low as 44%. Frequent cycling and energy losses during idle periods further impact performance. These metrics highlight the importance of selecting the right heating element and properly sizing the heater for each application.
Note: Real-world efficiency depends on installation, usage patterns, and regular maintenance, not just laboratory ratings.
User Experience and Convenience
Heating elements directly influence how users interact with appliances. Flexible heating modes and adjustable temperature settings allow users to tailor their experience for comfort, speed, or energy savings. Recent user preference data shows that 72.7% of users favor a normal heating mode, which balances energy efficiency and heating speed. Continuous heating mode, preferred by 57.2%, ensures hot water is always available, enhancing convenience. Quick heating mode appeals to 17.8% of users who need immediate warmth.
User Preference Aspect | Percentage | Explanation |
---|---|---|
Continuous heating mode | 57.2% | Hot water available anytime, increasing convenience. |
Normal heating mode | 72.7% | Balances energy saving and heating speed for daily use. |
Quick heating mode | 17.8% | Immediate warm water for urgent needs. |
Temperature setting below 55°C | 32.2% | Preference for energy saving and safety. |
Temperature setting 55–60°C | 26.3% | Balances comfort and efficiency. |
Temperature setting 65°C and above | 22.2% | Prioritizes warmth. |
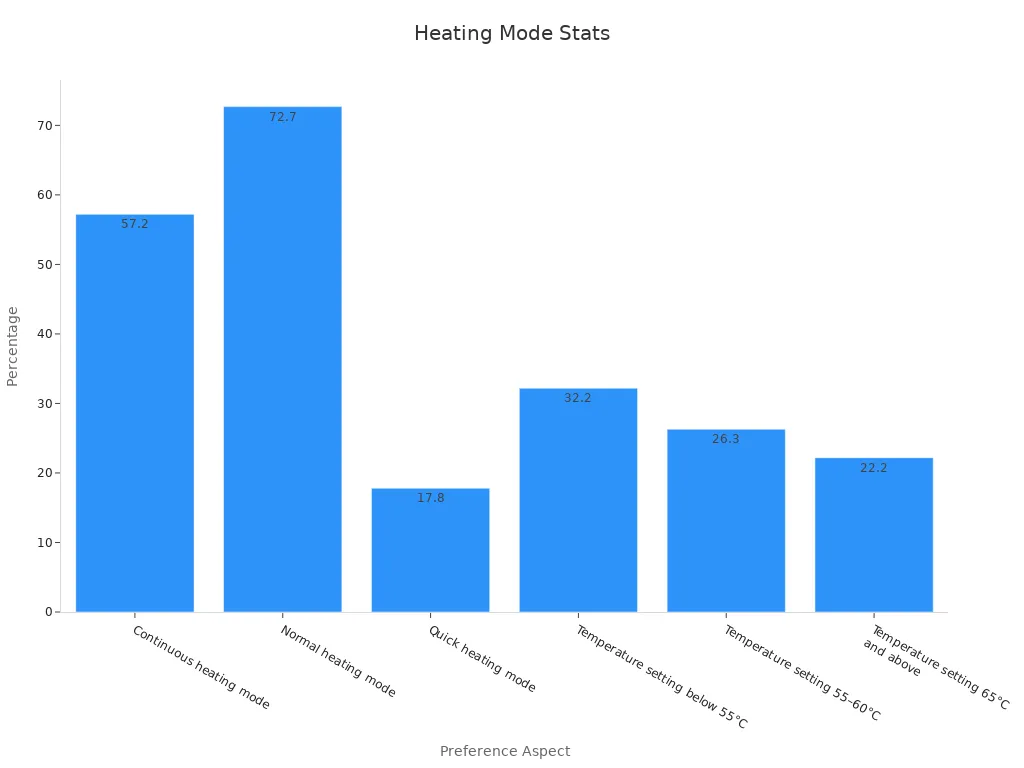
Heating elements that offer multiple modes and precise temperature control improve user satisfaction. Appliances with advanced heater technology provide both convenience and adaptability for different household needs.
Maintenance and Replacement of Heating Elements
Regular maintenance ensures that heating elements continue to operate safely and efficiently. Over time, mineral buildup, corrosion, or mechanical wear can reduce the effectiveness of a heater. Many modern appliances feature accessible designs that simplify the inspection and replacement of heating elements. Users benefit from clear indicators, such as reduced heating speed or uneven temperature, which signal when a replacement may be necessary.
- Schedule periodic inspections to check for visible damage or buildup.
- Clean or descale water heaters to prevent mineral deposits from affecting performance.
- Replace faulty heating elements promptly to maintain appliance efficiency and safety.
Tip: Proactive maintenance extends the lifespan of heating elements and helps avoid unexpected appliance failures.
Innovations and Trends in Heating Element Technology
Advances in Nichrome, Kanthal, and Other Materials
Recent years have seen remarkable progress in heating element materials. Researchers have enhanced nichrome by developing braided wire microprobes, which show up to 21 times greater mechanical compliance than single wires. This advancement supports flexible, durable devices for biomedical and industrial applications. Nichrome also plays a key role in thermal annealing for optical resonators, reducing surface stresses and improving quality. Scientists have used bulk nichrome alloys to catalyze the growth of carbon nanofibers, expanding its use in nanomaterial fabrication. Plasma nanocomposite coatings, created with nichrome powders, now offer improved surface performance for protective and functional applications.
Kanthal continues to lead in high-temperature electric heating. Its unique composition enables operation at temperatures up to 1400°C, making it ideal for industrial furnaces and specialty ovens. Engineers have improved kanthal’s oxidation resistance and thermal shock stability, ensuring reliable performance in demanding environments. Cupronickel, with its high electrical resistivity and corrosion resistance, remains a preferred choice for marine and water heating systems. Platinum stands out for its unmatched stability and chemical resistance, supporting precise temperature control in laboratory and medical devices. Recent research on oxide dispersion strengthened nichrome alloys highlights improved creep resistance and mechanical properties, driven by nanoscale particle spacing and stable subgrain structures.
Smart and Energy-Efficient Heating Elements
The integration of smart technology has transformed electric heating. AI-enhanced thermostats, such as the latest Nest Learning Thermostat, use machine learning to optimize heating schedules based on occupancy and weather. These systems achieve significant energy savings and reduce greenhouse gas emissions by up to 7.25 gigatons of CO2 equivalent globally. Lifetime operational cost savings can reach over US$2 trillion, demonstrating the economic benefits of smart controls.
Engineers design custom heating elements with high-performance materials, such as kanthal and platinum, to achieve higher heat transfer rates and uniform heating. Smart energy management features enable automatic power adjustments, reducing energy waste. Strategic placement and configuration of heating elements ensure even heat distribution and minimize loss. In wearable technology, heated jackets now use carbon fiber and micro coils, providing lightweight, flexible, and efficient heat generation. Conductive fabrics and printed heating elements with conductive inks offer further customization and comfort. Power sources have advanced to rechargeable batteries and USB power banks, enhancing portability and user control.
Smart integration allows real-time adaptation to operational needs, supporting sustainability and productivity across industries.
Environmental Impact of Modern Electric Heating
Modern electric heating methods have shifted toward sustainability and reduced environmental impact. Traditional electric resistance heating, while simple, consumes more electricity and leaves a larger carbon footprint. In contrast, heat pump systems, including water-source and ammonia-based models, transfer heat rather than generate it. These systems achieve efficiencies up to 400% and significantly lower emissions. For example, large-scale heat pumps in Germany reduce CO2 emissions by 3,200 metric tons annually and cut heating costs by 40%.
Retrofitting HVAC systems with smart controls and advanced heating elements, such as kanthal and platinum, further improves energy efficiency and reduces emissions. Life cycle assessments emphasize the importance of combining purification technologies and recovering waste heat. Projects like Energy Hub Aalsmeer demonstrate how waste heat from data centers can supply heating to other facilities, supporting net-zero carbon goals. The transition to heat pumps and smart electric heating supports equity by lowering energy burdens and improving health outcomes, especially in underserved communities.
Technology | Efficiency | Emissions Reduction | Notable Materials Used |
---|---|---|---|
Heat Pumps | Up to 400% | High | Kanthal, Platinum |
Electric Resistance | Low | Low | Nichrome, Cupronickel |
Smart HVAC | High | High | Kanthal, Platinum, Nichrome |
The adoption of advanced materials and smart controls in electric heating marks a significant step toward sustainable, efficient, and equitable energy solutions.
Heating elements convert electrical energy into heat, powering essential household appliances like ovens and heaters. Their design and material innovations, such as metal alloys and PTC technology, improve efficiency and temperature control. Research shows that optimizing heating element layout can boost startup speed but may affect temperature consistency. Ongoing advancements in heating elements reflect the broader trend of continuous R&D and collaboration in sustainable energy, ensuring reliable and safe performance for modern homes.
FAQ
What is the main purpose of a heating element in household appliances?
A heating element converts electrical energy into heat. This process enables appliances to perform tasks such as cooking, drying, or warming water efficiently and safely.
Which materials are most commonly used for heating elements?
Manufacturers often use nichrome, kanthal, and ceramic materials. These materials provide high resistance, durability, and stability at elevated temperatures.
How can users identify a faulty heating element?
Common signs include uneven heating, slow performance, or the appliance not producing heat. Visual inspection may reveal discoloration, breaks, or corrosion on the element.
Are heating elements safe to touch during operation?
Heating elements reach very high temperatures during use. Direct contact can cause burns or injury. Always allow the appliance to cool before handling or performing maintenance.
Can heating elements be replaced at home?
Many appliances allow users to replace heating elements with basic tools. Always follow manufacturer instructions and disconnect power before attempting any repairs.
What factors affect the lifespan of a heating element?
Material quality, operating temperature, watt density, and maintenance frequency all impact lifespan. Proper use and regular cleaning help extend service life.
Do all heating elements use the same method to transfer heat?
No. Heating elements transfer heat through conduction, convection, or radiation. The method depends on the appliance’s design and intended function.
Why do some appliances use PTC heating elements?
PTC (Positive Temperature Coefficient) elements self-regulate their temperature. This feature improves safety, prevents overheating, and increases energy efficiency in modern appliances.