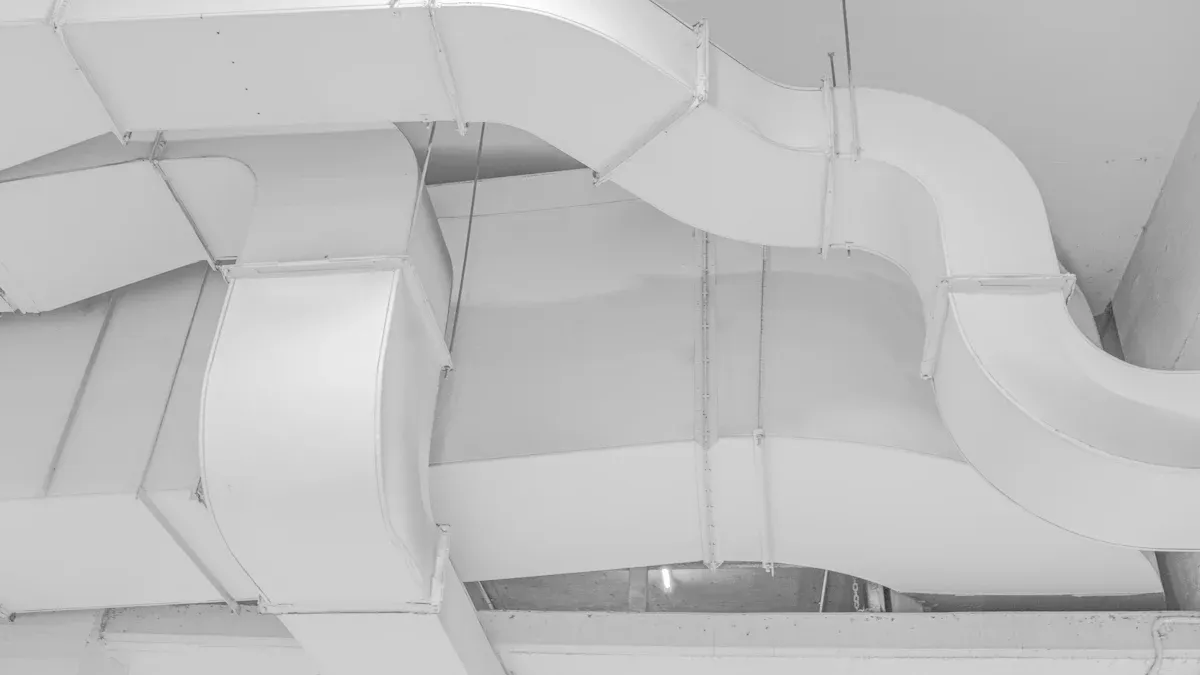
You rely on heat exchanger heating to maximize energy savings and comfort in your space. Essential components—such as heating tubes, heating elements, plate exchangers, and heater elements—deliver high efficiency and performance. Selecting the right élément chauffant or heating tubes can cut energy costs by up to 30% and significantly reduce carbon emissions. Efficient heat exchanger heating designs even shrink volume by 85% and boost heat transfer elevenfold, ensuring a compact and powerful solution.
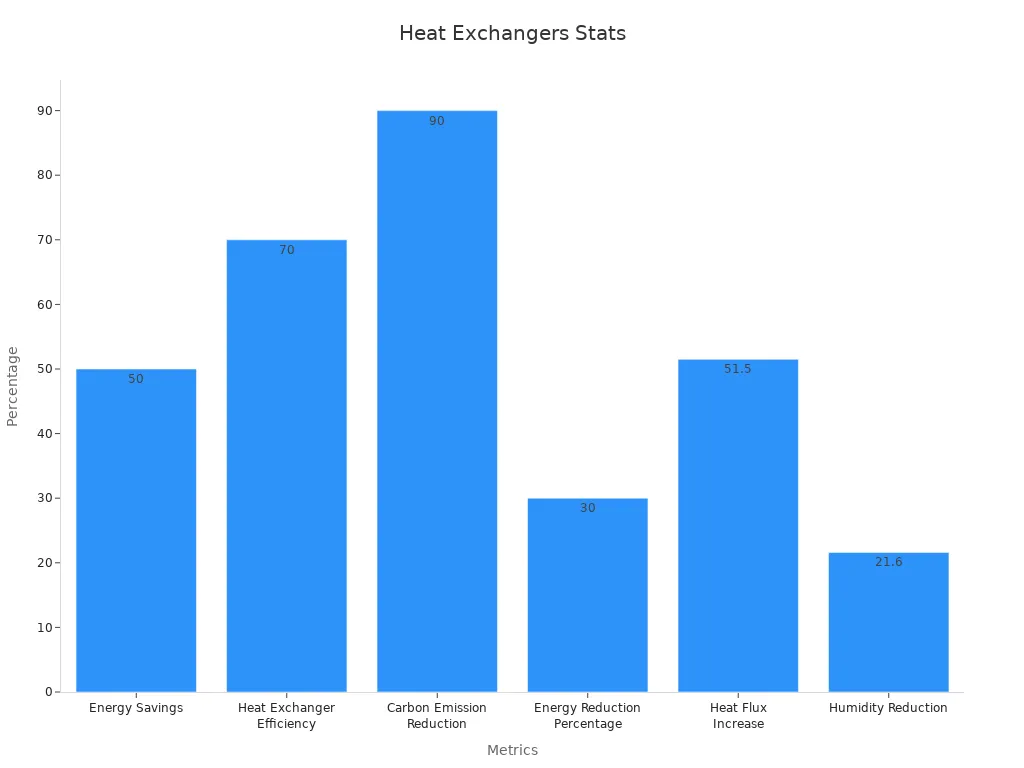
Metric / Parameter | Value / Range | Description / Context |
---|---|---|
Heating and cooling energy savings | Up to 50% | Percentage reduction in energy consumption for homes with improved thermal performance using heat exchanger heating. |
Heat exchanger efficiency | 70% | Typical efficiency rating of heat exchangers in heating systems utilizing heater elements and heating tubes. |
Energy cost reduction | 20-30% | Annual energy cost savings in commercial HVAC systems with heat exchanger heating and integrated heating elements. |
Carbon emission reduction | Up to 90% by 2050 | Projected cut in direct emissions by switching to low-carbon heating systems with efficient heat exchanger heating. |
Heat recovery | Up to 2190.43 kJ/h | Maximum heat recovered by heat pipe heat exchangers at optimal air velocity, enhanced by advanced heater elements. |
Effectiveness values | Up to 0.646 | Highest effectiveness of heat pipe heat exchangers under specific heat flux and air velocity conditions, supported by heating tubes. |
Energy reduction percentage | 30% | Reduction in energy consumption by adding wickless heat pipe heat exchangers and optimized heating elements to air conditioning equipment. |
Heat flux density increase | Up to 51.5% | Improvement in heat transfer rate on fin surfaces due to vibration technology in heat exchanger heating systems. |
Volume reduction and heat transfer | 85% volume reduction, heat transfer increased 11x | Improvements in heat exchanger heating design with advanced heating tubes and heater elements leading to compact size and higher performance. |
Economic payback period | ~3 years | Time to recover investment costs from electricity savings, with a service life of 20 years for heating elements and heat exchanger heating units. |
Humidity reduction | Up to 21.6% | Reduction in indoor humidity improving comfort and system performance through efficient heat exchanger heating. |
Comfort metrics | Maintains indoor temperatures within comfort range | Advanced HVAC systems with heat exchanger heating and integrated heater elements meet standards like ASHRAE 55 for thermal comfort. |
Understanding Heat Exchanger Heating
What Is a Heat Exchanger?
You encounter heat exchangers in many modern heating systems. A heat exchanger is a device that transfers thermal energy between two or more fluids at different temperatures, without mixing them. Industry standards such as ASME, TEMA, and API 660 define the technical requirements for these devices, ensuring safety and performance across applications. You will find several types, including shell and tube, plate, and plate-and-shell designs. Each type offers unique features for specific pressure, temperature, and maintenance needs.
Remarque : Heat exchangers must comply with rigorous testing and certification, such as hydrostatic testing and non-destructive testing, to guarantee reliability and longevity.
Heat Exchanger Type | Description & Technical Clarification | Key Features & Applications |
---|---|---|
Shell and Tube | Tubes carry one fluid inside a shell with another fluid outside; includes baffles for flow control. | Robust, high-pressure, industrial processes. |
Plate | Thin, corrugated plates create multiple flow channels; allows counter-current flow. | Compact, efficient, used in HVAC and refrigeration. |
Plate and Shell | Welded plate pack inside a shell; no gaskets. | High heat transfer, compact, secure against leakage. |
The Role of Heat Exchangers in Heating Systems
You rely on heat exchanger heating to maximize energy efficiency and system performance. In heating systems, these devices recover waste heat, preheat incoming fluids, and maintain optimal temperatures. Empirical studies show that heat pipe heat exchangers offer high reliability, low pressure drop, and complete separation of working fluids. Baffles inside the exchanger improve thermal performance by promoting uniform fluid flow and forced convection. These features help you achieve better energy savings and system reliability.
Recent market research highlights the growing importance of heat exchanger heating in modern systems. The global market is expanding rapidly, driven by technological advancements, energy efficiency demands, and sustainability trends.
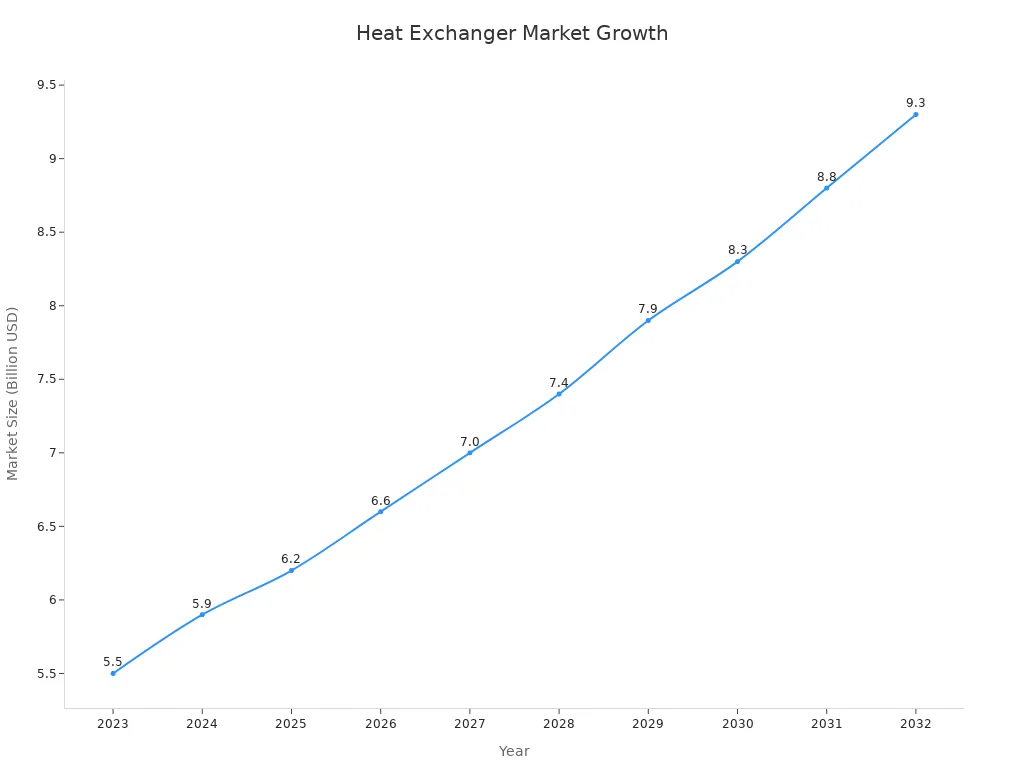
Year | Market Size (Billion USD) |
---|---|
2023 | 5.5 |
2024 | 5.9 |
2025 | 6.2 |
2026 | 6.6 |
2027 | 7.0 |
2028 | 7.4 |
2029 | 7.9 |
2030 | 8.3 |
2031 | 8.8 |
2032 | 9.3 |
You see this growth reflected in renewable energy projects, industrial processes, and green building trends. Heat exchangers now play a vital role in solar thermal collectors, geothermal systems, and fuel cell applications.
Key Performance Factors in Heat Exchanger Heating
When you evaluate heat exchanger heating systems, you must consider several critical performance metrics. These factors determine how effectively your system operates and how much energy you save.
Métrique | Definition | Significance |
---|---|---|
Heat Transfer Rate (Q) | Amount of heat transferred per unit time between fluids | Fundamental measure of heat exchanger capacity |
Effectiveness (ε) | Ratio of actual heat transfer to maximum possible heat transfer | Indicates how close the exchanger operates to theoretical maximum efficiency |
Overall Heat Transfer Coefficient (U) | Ability to transfer heat across exchanger surface considering resistances | Reflects efficiency of heat transfer through materials and fluids |
Pressure Drop (ΔP) | Difference in fluid pressure between inlet and outlet | High values indicate flow restrictions or fouling, affecting pumping power and efficiency |
Fouling Factor (R_f) | Accounts for reduction in heat transfer due to deposits on surfaces | Fouling degrades performance, increases pressure drop, and raises operational costs |
Thermal Efficiency (η) | Ratio of heat transferred to cold fluid over heat removed from hot fluid | Measures energy transfer efficiency |
You should also monitor approach temperature, capacity ratio, and number of transfer units (NTU) to optimize your system. Regular maintenance and monitoring help you prevent fouling and maintain high efficiency over time.
Types of Heat Exchangers for Heating Applications
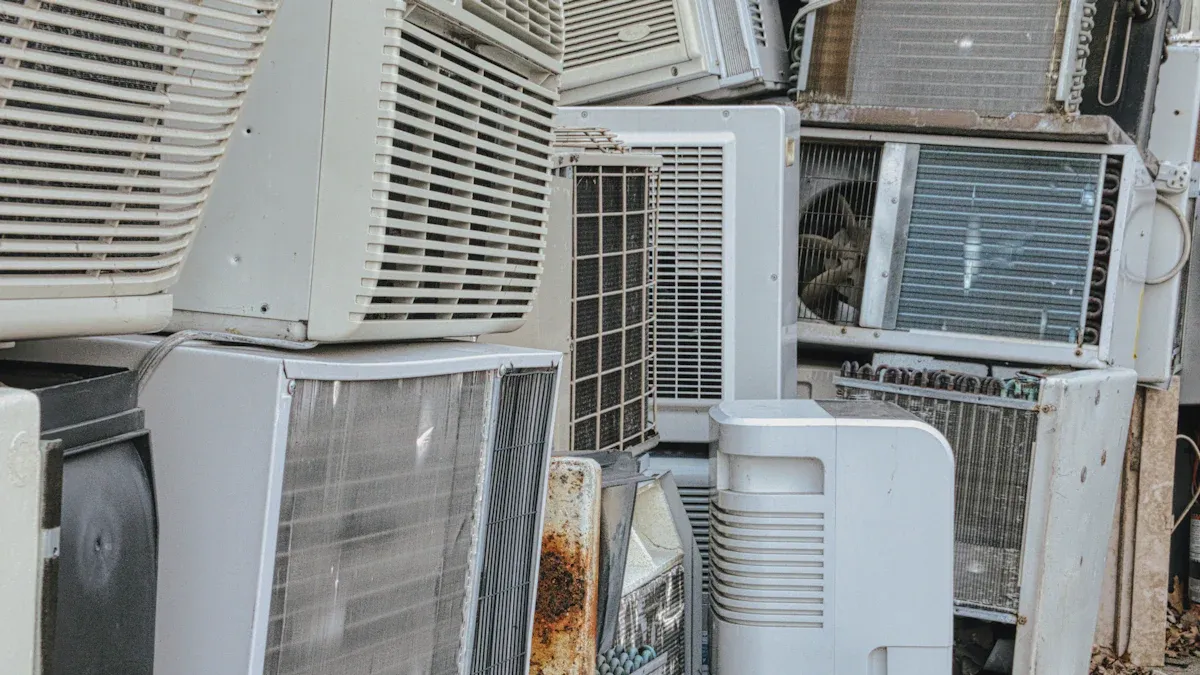
Modern heating systems rely on several types of heat exchangers to deliver precise temperature control, energy efficiency, and operational reliability. You need to understand the structure, operation, and advantages of each design to select the best solution for your application. Below, you will find an in-depth look at three essential heat exchanger types for heating applications.
Double Tube Heat Exchangers
Structure and Design
Double tube heat exchangers feature a simple yet robust construction. You will see two concentric tubes—one nested inside the other. The hot and cold fluids flow separately, one through the inner tube and the other through the annular space between the tubes. This arrangement allows you to achieve efficient heat transfer while keeping the fluids completely isolated.
- Inner tube: Carries one fluid (hot or cold).
- Outer tube: Contains the second fluid, flowing in the opposite direction.
- Materials: Typically stainless steel or copper for corrosion resistance and thermal conductivity.
Operation Principles
You operate double tube heat exchangers using either counter-flow or parallel-flow arrangements. In counter-flow, the fluids move in opposite directions, maximizing the temperature gradient and heat transfer efficiency. Parallel-flow means both fluids travel in the same direction, which results in a lower temperature difference and reduced efficiency.
Conseil : Counter-flow operation in double tube heat exchangers delivers higher thermal efficiency, making it the preferred choice for most heating applications.
Advantages
You benefit from several key advantages when you choose double tube heat exchangers:
- Compact size and straightforward design simplify installation and maintenance.
- High pressure and temperature tolerance make them suitable for demanding environments.
- Easy to clean and inspect, reducing downtime and operational costs.
Technical studies confirm that double tube heat exchangers handle high pressure and temperature, making them ideal for power plants and chemical processing. Experimental research also shows that adding twisted tape inserts and helical tape to the tubes can boost the Nusselt number by up to 315% and achieve a thermal performance factor of 3.06. These enhancements significantly improve heat transfer and energy efficiency.
Ideal Applications
You will find double tube heat exchangers in:
- Power generation plants
- Chemical processing facilities
- Industrial heating loops
- Applications requiring compactness and high-pressure operation
Their versatility and reliability make them a staple in many industrial heating systems.
Shell and Tube Heat Exchangers
Structure and Components
Shell and tube heat exchangers represent one of the most widely used types of heat exchangers in industrial and commercial heating. You will see a bundle of tubes housed within a cylindrical shell. One fluid flows through the tubes, while the other circulates around them inside the shell. Baffles direct the flow, increasing turbulence and improving heat transfer.
Component | Function |
---|---|
Tube bundle | Carries one of the fluids |
Shell | Contains the second fluid |
Baffles | Guide fluid flow, enhance turbulence |
Tube sheets | Secure tubes and prevent leakage |
How Shell and Tube Exchangers Work
You operate shell and tube heat exchangers by passing hot and cold fluids through separate pathways. The design allows for multiple passes of fluids, which increases the surface area for heat exchange. You can select different flow arrangements—counter-flow, parallel-flow, or cross-flow—depending on your efficiency requirements.
A comprehensive experimental comparison of four shell-and-tube heat exchangers demonstrates that finned designs can increase the heat transfer surface area by up to 9.4 times and improve efficiency by as much as 40%. Using water as the heat transfer fluid further enhances performance due to its high specific heat and thermal conductivity.
Key Benefits
You gain several benefits from shell and tube heat exchangers:
- High heat transfer rates support large-scale heating needs.
- Modular design allows for easy expansion and customization.
- Suitable for a wide range of pressures and temperatures.
- Finned tube options further boost efficiency.
Qualitative evaluations highlight that shell and tube heat exchangers excel in applications where you need robust construction, fouling resistance, and ease of maintenance. The ability to use different flow arrangements, such as counter-flow, enhances thermal efficiency and operational flexibility.
Best Uses in Heat Exchanger Heating
You will commonly use shell and tube heat exchangers in:
- District heating systems
- Industrial process heating
- Power plant condensers
- HVAC systems for large buildings
Their adaptability and proven performance make them a top choice for many heating applications.
Tube-in-Tube Heat Exchangers
Design Features
Tube-in-tube heat exchangers, a specialized variant among the types of heat exchangers, consist of one tube placed inside another. You will notice that the inner and outer tubes can feature surface enhancements, such as dimples or twisted inserts, to increase turbulence and heat transfer.
- Inner tube: Typically smooth or enhanced with surface features.
- Outer tube: Provides an annular space for the second fluid.
- Material selection: Focuses on thermal conductivity and corrosion resistance.
Working Mechanism
You operate tube in tube heat exchangers by directing two fluids through the concentric tubes, usually in a counter-flow arrangement. The design ensures a high temperature gradient and efficient heat transfer. Surface modifications, such as elliptical or teardrop dimples, disrupt the boundary layer and promote mixing, which further improves performance.
A case study on tube-in-tube and shell-and-tube configurations found that elliptical dimples improved performance evaluation criteria by up to 36.7%, while teardrop dimples increased it by as much as 51.5%. These enhancements demonstrate the significant impact of surface design on heat exchanger effectiveness.
Main Advantages
You benefit from several advantages when you use tube-in-tube heat exchangers:
- High thermal efficiency due to enhanced surface area and turbulence.
- Compact footprint, ideal for space-constrained installations.
- Simple construction allows for easy cleaning and maintenance.
- Effective for handling fluids with high fouling potential.
Experimental studies show that design modifications, such as twisted tape inserts, can increase the Nusselt number by up to 315% compared to plain pipes. This translates to substantial improvements in heat transfer and energy savings.
Suitable Heating Applications
You will find tube-in-tube heat exchangers in:
- Hot water generation systems
- Industrial process heating
- Oil and gas heating loops
- Applications requiring high efficiency in a compact form
Their ability to deliver high performance in demanding environments makes them a valuable option for modern heating systems.
Plate Heat Exchangers
Types of Plate Heat Exchangers (Gasketed, Brazed)
You encounter two main types of plate heat exchangers in modern heating systems: gasketed and brazed. Gasketed plate heat exchangers use elastomer gaskets to seal the plates and direct fluid flow. You can easily disassemble them for cleaning or maintenance. Brazed plate heat exchangers, on the other hand, use thin plates joined by brazing, usually with copper or nickel. This design creates a compact, leak-resistant unit that handles higher pressures and temperatures.
-
Gasketed Plate Heat Exchangers:
- Flexible and easy to maintain
- Suitable for applications with frequent cleaning needs
- Allow you to add or remove plates to adjust capacity
-
Brazed Plate Heat Exchangers:
- Compact and robust
- Ideal for high-pressure, high-temperature environments
- Require minimal maintenance
Plate Construction and Layout
You notice that plate heat exchangers consist of a series of thin, corrugated metal plates stacked together. The corrugations create turbulence, which increases heat transfer efficiency. Manufacturers use materials like stainless steel, copper, or aluminum for their high thermal conductivity and corrosion resistance. The plate thickness, corrugation angle, and pitch all influence the exchanger’s performance. You benefit from a large surface area in a compact footprint, which makes these exchangers highly efficient.
Remarque : Testing methods such as the guarded hot plate apparatus and Laser Flash Analysis (LFA) help ensure that the materials and design meet strict thermal performance standards.
How Plate Exchangers Operate
You operate plate heat exchangers by passing two fluids through alternating channels formed by the plates. The fluids flow in opposite directions, creating a counter-current arrangement. This setup maximizes the temperature difference between the fluids, which boosts heat transfer. The gaskets or brazed joints keep the fluids separate, preventing mixing and ensuring safety.
Benefits for Heat Exchanger Heating
You gain several advantages when you use plate heat exchangers in heating systems:
- High heat transfer efficiency due to large surface area and turbulent flow
- Compact size, which saves valuable space in mechanical rooms
- Easy maintenance for gasketed models, allowing you to clean or replace plates quickly
- Reliable operation at a wide range of temperatures and pressures
Industry benchmarks highlight the versatility of plate heat exchangers. You can use them with hot water (60–90°C) for stable, efficient heating. They also handle saturated steam (100–275°C) for precise temperature control and cost-effective operation. Hot oil (180–300°C) and molten salt (400–590°C) applications benefit from higher operating temperatures and reduced risk of overheating. When you recover waste heat from flue gas or hot air (750–1100°C), you improve boiler efficiency, though you must manage corrosion risks.
You should consider key performance metrics such as thermal conductivity, thermal resistance, and heat transfer efficiency. Materials like copper and aluminum enhance effectiveness. Geometric factors, including plate thickness and corrugation, further optimize performance. Application-specific standards focus on response time, durability, and operational temperature range, ensuring you maintain efficiency and reliability.
Where Plate Exchangers Excel
You find plate heat exchangers excel in:
- Residential and commercial HVAC systems
- District heating networks
- Industrial process heating
- Renewable energy systems, such as solar thermal collectors
Their adaptability and high efficiency make them a preferred choice among the types of heat exchangers for modern heating applications.
Air-Cooled Heat Exchangers
Design and Functionality
You see air-cooled heat exchangers use ambient air to cool or heat process fluids. The design features finned tubes or plates that increase the surface area for heat exchange. Fans or natural convection move air across the surfaces, transferring heat between the fluid and the air. This eliminates the need for water or other secondary coolants, making the system simpler and more sustainable.
Operation in Heating Systems
You operate air-cooled heat exchangers by circulating hot fluid through the finned tubes while air flows over the exterior. The heat transfers from the fluid to the air, lowering the fluid temperature. In heating applications, you can also use these exchangers to recover heat from exhaust gases or process streams, improving overall system efficiency.
Parameter | Earth Air Heat Exchanger (EAHE) | Seasonal Storage System (Underground Tank) |
---|---|---|
Outlet Temperature Range (°C) | 19 – 24 | 16 – 20 |
Determination Coefficient (R²) | 0.953 | 0.984 |
Root Mean Square Error (RMSE) | 0.093 | 0.406 |
Mean Squared Error (MSE) | 0.306 | 0.165 |
You notice that earth air heat exchangers (EAHE) deliver higher outlet temperatures compared to seasonal storage systems. Advanced modeling techniques, such as LSTM neural networks, accurately predict system temperatures, confirming the reliability and efficiency of air-cooled designs. Factors like pipe configuration, soil temperature, and climate also influence performance.
Advantages of Air-Cooled Exchangers
You benefit from several advantages when you choose air-cooled heat exchangers:
- No need for water, reducing operational costs and environmental impact
- Simple installation and low maintenance requirements
- Effective heat recovery from waste streams
- Reliable performance in a wide range of climates
Comparative studies show that air-cooled exchangers, especially EAHE systems, provide effective heat exchange and predictable performance, making them a strong option among the types of heat exchangers for sustainable heating.
Best-Fit Heating Applications
You find air-cooled heat exchangers best suited for:
- Industrial facilities with limited water resources
- Renewable energy systems, such as geothermal and solar air heating
- HVAC systems in arid or remote locations
- Waste heat recovery in manufacturing plants
Their versatility and low maintenance make them a practical solution for many heating challenges.
Spiral Heat Exchangers
Structure and Flow Arrangement
You recognize spiral heat exchangers by their unique spiral-shaped channels, formed by winding metal plates around a central core. This design creates a single, continuous flow path for each fluid, ensuring true counter-current flow. The large surface area and compact footprint set spiral exchangers apart from other heat exchanger types.
- Spiral Tube Heat Exchanger (STHE): Features single-channel counter-current flow, ideal for fouling resistance.
- Spiral Plate Heat Exchanger (SPHE): Uses welded plates for mechanical strength and durability.
How Spiral Exchangers Work
You operate spiral heat exchangers by directing two fluids through separate spiral channels. The counter-current arrangement maximizes the temperature gradient, which increases heat transfer efficiency. The single-channel design handles viscous or fouling-prone fluids effectively, reducing maintenance needs and downtime.
Numerical and experimental studies confirm that spiral heat exchangers achieve higher Nusselt numbers, indicating superior heat transfer rates. Oval cross-section designs further enhance performance, while square cross-sections reduce entropy generation and improve thermodynamic efficiency.
Key Benefits for Heating
You gain several key benefits from spiral heat exchangers:
- High thermal efficiency due to true counter-current flow and large surface area
- Excellent handling of dirty, viscous, or fouling-prone fluids
- Reduced maintenance costs and downtime
- Enhanced operational safety with minimal risk of fluid mixing or leakage
Technical analyses show that spiral exchangers provide compact design, improved thermal performance, and cost-effectiveness. You can optimize design and reliability using advanced modeling and decision-making methods, ensuring productivity in energy-efficient heating systems.
Ideal Applications
You find spiral heat exchangers widely used in:
- Sludge processing and wastewater treatment
- Food and beverage production
- Petrochemical and pharmaceutical industries
- Combined heat and power (CHP) systems
Their ability to handle challenging fluids and deliver high efficiency makes them a valuable addition to your heating system toolkit.
Finned Tube Heat Exchangers
Design and Surface Area Enhancement
You will notice that finned tube heat exchangers use extended surfaces, or “fins,” attached to the outside of tubes. These fins increase the surface area available for heat transfer between the tube and the surrounding air or gas. Manufacturers offer a variety of fin shapes, including wavy, louvered, offset strip, and perforated designs. Each geometry aims to maximize heat transfer while minimizing pressure drop. By optimizing parameters such as fin pitch, fin height, fin thickness, and tube diameter, you can achieve a heat transfer rate nearly five times higher than with plain tubes. Internal fins and helically finned tubes further enhance performance, especially at higher flow rates.
- Finned tubes with more fins can improve heat transfer up to 3.56 times compared to smooth tubes at higher Reynolds numbers.
- Perforated fins boost airflow and reduce thermal resistance, leading to better heat dissipation.
- Helically finned tubes reach efficiency indexes up to 2.1, outperforming many traditional designs.
- Geometric optimization can improve the performance index by 2.9 times.
Conseil : When you select a finned tube heat exchanger, always consider the trade-off between increased heat transfer and the resulting pressure drop.
Operation in Air and Gas Heating
You operate finned tube heat exchangers by passing hot or cold fluid through the tubes while air or gas flows over the finned surfaces. The fins act as bridges, transferring heat efficiently from the tube wall to the air or gas. This design is especially effective in air and gas heating, where the low thermal conductivity of air makes surface area enhancement critical. You can arrange the tubes in staggered or in-line patterns to further optimize heat transfer and airflow. The system’s thermal–hydraulic performance is often evaluated using the Colburn factor, friction factor, and Nusselt number. These metrics help you balance heat transfer improvement against the energy required to move air or gas through the exchanger.
Advantages in Heat Exchanger Heating
You gain several advantages when you use finned tube heat exchangers in heating systems:
- Superior heat transfer performance compared to plain tube designs.
- Compactness, allowing you to achieve the same heating or cooling effect with a smaller unit.
- Flexibility in design, with a wide range of fin geometries and arrangements to suit different needs.
- Enhanced energy efficiency, as improved heat transfer reduces the amount of energy required for heating or cooling.
Studies show that enhanced fins can increase heat transfer coefficients by 50–150% over plain fins. You also benefit from reduced equipment size and lower operational costs. However, you must carefully consider the balance between heat transfer and pressure drop, as excessive resistance can increase pumping or fan power requirements.
Common Applications
You will find finned tube heat exchangers widely used in:
- HVAC systems for heating and cooling air in buildings.
- Process gas heating in chemical plants.
- Waste heat recovery from exhaust gases in industrial applications.
- Air preheaters in power generation and boiler systems.
Their ability to deliver high efficiency and compactness makes them a preferred choice for air and gas heating, especially in industrial applications where space and energy savings are critical.
Regenerative Heat Exchangers
Static vs. Dynamic Designs
You can choose between static and dynamic regenerative heat exchangers. Static designs use a fixed matrix of heat-absorbing material, such as ceramic or metal, which alternately stores and releases heat as the flow direction changes. Dynamic designs feature a rotating matrix or wheel that continuously moves through hot and cold streams, transferring heat from one to the other. Both types aim to maximize heat recovery and improve overall system efficiency.
Working Principle
You operate a regenerative heat exchanger by alternating the flow of hot and cold fluids through the same heat storage medium. In static designs, you periodically switch the direction of flow, allowing the matrix to absorb heat from the hot stream and then release it to the cold stream. In dynamic designs, the rotating wheel or matrix moves between the two streams, continuously absorbing and releasing heat. This cyclical process enables you to recover a significant portion of waste heat that would otherwise be lost.
Benefits for Heat Recovery
You benefit from several key advantages when you use regenerative heat exchangers for heat recovery:
- Improved energy efficiency, with energy savings ranging from 20% to 50% depending on the application.
- Reduced operating costs, as you recover and reuse heat that would otherwise escape.
- Lower environmental impact, with significant reductions in CO2 and NOx emissions.
- Enhanced performance and durability, thanks to advances in materials and design.
For example, a slab-type heating furnace with regenerative burners achieved a thermal efficiency of 72% and fuel savings of 15% compared to conventional burners. In the steel industry, regenerative heat exchangers can deliver up to 30% energy savings. Combined cycle power plants have documented efficiency improvements of up to 5% using these systems. You will also find that heat recovery devices like economizers can recover 10–25% more waste heat than non-condensing types.
Remarque : While challenges such as fouling and maintenance exist, current technology and material advances make these issues manageable.
Applications in Modern Heating
You will find regenerative heat exchangers in a wide range of modern heating systems, including:
- Power generation plants, where they recover heat from exhaust gases.
- Chemical processing facilities, improving process efficiency and reducing fuel consumption.
- HVAC systems, where they preheat incoming air using exhaust air.
- Industrial applications in sectors such as petrochemical, food, cement, glass, and steel.
These exchangers play a vital role in reducing energy consumption and emissions across many industries. As you look to the future, ongoing research focuses on high-temperature applications and the development of advanced materials for even greater durability and efficiency.
Flow Arrangements in Heat Exchanger Heating
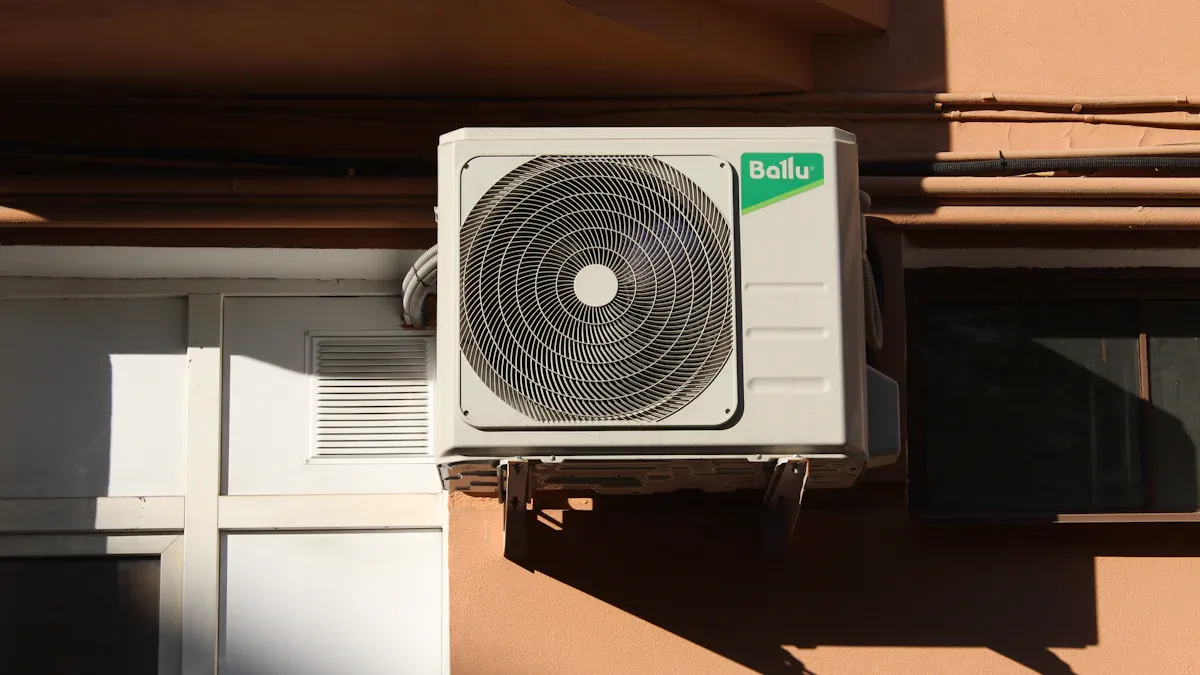
Understanding how fluids move through a heat exchanger helps you maximize efficiency and performance. The flow arrangement determines how heat transfers between fluids, affecting temperature gradients, pressure drops, and overall system effectiveness. You will encounter three main flow patterns: parallel flow, counter flow, and cross flow. Each offers unique benefits and challenges for heating applications.
Parallel Flow
In a parallel flow heat exchanger, both fluids enter the exchanger at the same end and move in the same direction. You will notice that the temperature difference between the fluids is highest at the inlet and decreases along the length of the exchanger. This arrangement often results in a lower average temperature gradient, which can limit heat transfer efficiency.
Industry research and experimental data provide valuable insights into parallel flow performance. For example, studies on thermosiphon and heat pipe heat exchangers show effectiveness values ranging from 35.6% to 57.7% in waste heat recovery. In air conditioning retrofits, parallel flow designs demonstrate enhanced efficiency, especially when using advanced heat pipe configurations. One study found that a parallel-flow heat pipe heat exchanger achieved up to 98% heat transfer efficiency with minimal thermal resistance, making it highly effective for energy-saving applications. Another numerical study revealed that parallel-flow configurations can deliver about 6% higher net heat transfer efficiency than counter flow in certain double-pipe evaporative systems.
Study / Author(s) | Heat Exchanger Type | Key Experimental Data / Findings | Application / Context |
---|---|---|---|
Gedik et al. | Thermosiphon heat exchangers | Effectiveness ranged from 35.6% to 57.7% | Waste heat recovery from industrial flue gas |
Lu et al. | Parallel-flow heat pipe heat exchanger | Heat transfer efficiency up to 98%; minimum thermal resistance 0.06 K/W | Energy saving in air conditioning systems |
Abishek | Double-pipe evaporative heat exchanger | Parallel-flow configuration has ~6% higher net heat transfer efficiency than counter flow | Flow configuration effect on heat transfer |
You will find parallel flow arrangements suitable for applications where you need moderate heat transfer and simple construction, such as small-scale heating or cooling systems.
Counter Flow
Counter flow heat exchangers direct the two fluids in opposite directions. You will see that this arrangement maintains a higher temperature difference between the fluids throughout the exchanger’s length. As a result, counter flow designs achieve greater thermal efficiency and higher heat transfer rates compared to parallel flow.
Research on helical tube and chaotic heat exchanger designs highlights the advantages of counter flow. Numerical and experimental studies show that modifying coil geometry or introducing chaotic advection can significantly boost mixing and heat transfer. For example, chaotic flow arrangements enhance hydro-thermal performance across a wide range of flow conditions, outperforming traditional helical coils. These findings confirm that counter flow remains the preferred choice for maximizing efficiency in most heating applications.
You should select counter flow when you require high effectiveness, such as in industrial process heating, district energy systems, or applications with strict temperature requirements.
Cross Flow
Cross flow heat exchangers position the two fluids so they move perpendicular to each other. You will often use this arrangement in systems where one fluid is a gas and the other is a liquid, such as air-to-water or air-to-refrigerant exchangers. Cross flow designs offer flexibility and compactness, making them popular in HVAC and process industries.
Technical evaluations and performance metrics reveal how cross flow arrangements influence heating system efficiency:
- Experimental studies and numerical modeling examine the impact of air and liquid flow rates, temperatures, and humidity on heat transfer coefficients.
- Advanced modeling techniques, such as Adaptive Neuro-Fuzzy Inference Systems, improve performance prediction and optimize operational parameters.
- Key metrics include air outlet temperature, heat transfer coefficient, total heat transfer capacity, and thermal efficiency.
- Sensitivity analyses show that changes in inlet conditions, like air temperature or solution concentration, directly affect system output.
- Comparative studies highlight the advantages of cross-flow closed-type heat-source towers, especially under low ambient temperatures, where they deliver improved thermal efficiency and frost-free operation.
- Artificial intelligence methods help you predict performance and understand how input variables influence outcomes, supporting better system design and control.
You will benefit from cross flow arrangements in applications that demand reliable performance under varying conditions, such as air handling units, heat-source towers, and energy recovery ventilators.
Conseil : Choosing the right flow arrangement allows you to balance efficiency, cost, and operational needs for your specific heating application.
Impact on Efficiency and Application Suitability
When you select a heat exchanger for your heating system, you must consider how flow arrangement and configuration affect both efficiency and suitability for your application. The way fluids move through the exchanger—whether in parallel, counter, or cross flow—directly shapes the amount of heat transferred, the energy consumed, and the stability of your system.
You will notice that advanced flow arrangements often deliver higher efficiency. For example, multi-stage and serial configurations in absorption heat pumps (AHP) integrated with organic Rankine cycle (ORC) systems can significantly improve heat source utilization. A two-stage absorption heat exchanger coupled with an ORC system (AHEORC-HP) reduces the temperature of the heat source and boosts both thermoelectric and temperature efficiencies. These improvements mean you can extract more usable heat from the same energy input, which leads to lower operating costs and better system performance.
In district heating, the choice of flow arrangement becomes even more critical. A case study comparing two- and three-stage vertical absorption heat exchangers for independent heating in three zones found that the three-stage process, which used multiple absorption heat pumps and plate heat exchangers, achieved 20.3% to 27.7% higher efficiency than the simpler two-stage process. You also gain better self-regulation and more stable operation throughout the heating season. Although the three-stage system costs 26.4% more, the improved performance and reliability often justify the investment, especially in large-scale or mission-critical applications.
The physical arrangement of tubes and fins inside the heat exchanger also plays a major role. For instance, a comparative analysis of H-type finned tube heat exchangers showed that a column staggered tube bundle improves heat transfer compared to an in-line arrangement. This layout also reduces the high pressure drop seen in row staggered designs. The honeycomb arrangement, which builds on the column staggered concept, can match the thermal performance of in-line setups under certain conditions. By optimizing the internal structure, you can achieve better thermal-hydraulic efficiency, especially in flue gas heat recovery and other demanding environments.
Conseil : Always match the flow arrangement and internal configuration to your specific heating needs. A well-chosen design maximizes efficiency, reduces energy consumption, and ensures reliable operation.
Flow Arrangement / Configuration | Efficiency Impact | Best Application Areas |
---|---|---|
Multi-stage (serial) | Highest efficiency, stable | District heating, industrial processes |
Column staggered tube bundle | Improved heat transfer | Flue gas recovery, HVAC |
In-line tube bundle | Lower pressure drop | General heating, moderate loads |
Honeycomb | Balanced performance | Space-constrained systems |
By understanding these impacts, you can select a heat exchanger that not only meets your technical requirements but also delivers long-term value and sustainability for your heating system.
Choosing the Right Heat Exchanger Heating Solution
Factors to Consider (Capacity, Space, Fluid Type)
When you select a heat exchanger, you must evaluate several critical factors to ensure optimal performance. Capacity determines how much heat your system can transfer. You need to match the heat exchanger’s capacity to your heating or cooling load. Space constraints often influence your choice. Plate heat exchangers offer a compact footprint, occupying about 10% of the space required by shell-and-tube models. If you have limited room, modular plate designs allow you to adjust capacity by adding or removing plates.
Fluid type also plays a major role. For low to medium viscosity fluids, plate-and-frame exchangers provide high efficiency. Shell-and-tube designs handle higher pressures and fluids with particulates more effectively. Scraped-surface exchangers work best for very viscous or particulate-laden fluids, though they come with higher costs and maintenance needs.
Proper fan placement and the use of a plenum help maximize performance by distributing air evenly and reducing pressure drop. You should also consider air density, which affects mass flow and heat transfer capacity. At higher altitudes or temperatures, lower air density can reduce system effectiveness.
Characteristic | Plate-and-Frame | Shell-and-Tube | Scraped-Surface |
---|---|---|---|
Efficiency | High | Medium | Medium-High |
Footprint | Small | Large | Large |
Capacity Adjustment | Modular | Fixed | Fixed |
Use with Particulates | Poor | Good | Excellent |
Operating Pressure | Low-Medium | High | High |
Maintenance Ease | Easy | Modéré | Difficult |
Cost | Low | Low-Medium | High |
Fluid Viscosity Handling | Low-Medium | Medium-High | Very High |
Matching Types of Heat Exchangers to Applications
You need to match the right heat exchanger to your specific application. Shell-and-tube exchangers dominate in industries that require high pressure and temperature, such as petrochemical and power generation. Plate-and-frame models excel in HVAC, food and beverage, and applications where space and efficiency matter most. Air-cooled exchangers suit facilities with limited water resources or where environmental regulations restrict water use. Scraped-surface units handle thick or particulate-rich fluids in food processing or specialty chemical production.
Market research highlights several decision factors:
Decision Factor Category | Key Factors / Insights |
---|---|
Energy Efficiency | Minimize energy use and costs; optimize heat transfer without fluid mixing. |
Regulatory Compliance | Meet emissions and sustainability standards. |
Industrial Growth | Support expanding sectors needing precise temperature control. |
Heat Exchanger Type | Choose based on pressure, temperature, and efficiency needs. |
Material Selection | Use stainless steel for corrosion resistance; carbon steel for cost savings. |
End-Use Industry | Match to chemical, petrochemical, HVAC, food, power, or pulp sectors. |
Operational Considerations | Ensure temperature control, corrosion resistance, and real-time monitoring. |
Technological Advances | Integrate sensors for proactive maintenance and efficiency. |
Energy Efficiency and Cost Considerations
Energy efficiency remains a top priority when you invest in heat exchanger heating systems. Recent data from ground source heat pump systems shows a 14.1% increase in average coefficient of performance after optimization. AI-based control strategies can further boost energy savings by up to 7.84%. However, you must balance efficiency gains with long-term costs. For example, units with smaller diameters and longer lengths achieve higher exergetic efficiency but may cost $10,000–$12,000 over ten years, compared to $2,000–$2,600 for larger, shorter units.
You can use metrics like the Energy Efficiency Index (EEI) to compare plate heat exchangers. EEI considers both heat transfer performance and flow resistance, helping you select models that deliver energy savings without excessive pressure drop. Closed-form sizing methods and the effectiveness-NTU approach simplify design and ensure your system operates close to its theoretical optimum.
- Efficiency is the ratio of actual to optimal heat transfer.
- The EEI grades exchangers for energy efficiency, guiding your selection.
- Material choices, such as phase change materials in ground source systems, affect both efficiency and operational stability.
- Latent Heat Thermal Energy Storage (LHTES) units with phase change materials can improve thermal performance and reduce auxiliary equipment needs, supporting cost-effective, sustainable solutions.
Tip: Always weigh the trade-off between upfront investment and long-term operational savings. Prioritize systems that combine high efficiency with manageable costs for the best value.
Maintenance and Longevity
You play a crucial role in ensuring the long-term performance of your heat exchanger system. Regular maintenance keeps your equipment running efficiently and prevents unexpected breakdowns. When you invest in planned maintenance, you can reduce operational costs by up to 30%. This happens because clean and well-maintained heat exchangers transfer heat more effectively, which lowers energy consumption and improves system reliability.
Heat exchangers typically require less maintenance than pumps, fans, or compressors. You benefit from fewer moving parts, which means less wear and tear over time. However, you should not overlook routine inspections. Over time, fouling and scaling can build up on heat transfer surfaces. These deposits restrict flow, increase pressure drops, and reduce heat transfer efficiency. If you ignore these issues, your system will work harder, leading to higher energy bills and potential equipment failure.
Conseil : Schedule regular cleaning and inspection of your heat exchanger surfaces. Use recommended cleaning agents and follow manufacturer guidelines to avoid damaging sensitive components.
You should also monitor for leaks, corrosion, and gasket wear. Early detection of these problems helps you avoid costly repairs and unplanned downtime. Many modern systems include sensors and monitoring tools that alert you to changes in performance, such as rising pressure drops or declining heat output. By responding quickly, you can address minor issues before they become major problems.
Long-term studies of ground source heat pump (GSHP) systems, which rely on heat exchangers, show that while the initial investment is higher—sometimes 51.5% to 84.7% more than conventional systems—you save significantly on annual operating costs. These savings range from 20.8% to 33.1% each year. You also help the environment by reducing annual CO2 emissions by nearly half. The design and quality of your heat exchanger directly affect these outcomes. A well-designed system with proper maintenance will last longer and perform better.
Here are some best practices to maximize the longevity of your heat exchanger:
- Inspect and clean heat transfer surfaces regularly.
- Monitor system performance for early signs of fouling or leaks.
- Replace gaskets and seals as needed to prevent leaks.
- Use corrosion-resistant materials suited to your application.
- Keep detailed maintenance records for future reference.
Maintenance Task | Frequency | Benefit |
---|---|---|
Surface cleaning | Quarterly | Maintains heat transfer |
Leak inspection | Monthly | Prevents fluid loss |
Gasket replacement | Annually | Reduces risk of leaks |
Corrosion check | Semi-annually | Extends equipment lifespan |
Performance monitoring | Continuous | Detects issues early |
By following these steps, you ensure your heat exchanger operates efficiently for years. You protect your investment, lower your energy costs, and support a more sustainable heating system.
You gain the most value by selecting heat exchanger heating solutions tailored to your system’s demands. Counterflow heat exchangers consistently deliver higher thermal efficiency and better temperature control than parallel flow types, as shown in the table below and the chart.
Parameter | Counterflow Heat Exchanger | Parallel Flow Heat Exchanger | Notes |
---|---|---|---|
Thermal Enhancement Efficiency | ~76.23% at Re=1 | ~70.07% at Re=1 | Counterflow consistently shows higher thermal enhancement efficiency. |
Performance Index (η) at Re=1 | ~33972 (predicted), 34020 (actual) | ~30908.57 | Counterflow outperforms parallel flow in overall performance index. |
Temperature Drop (Hot Fluid) | 17.22 K decrease (325 to 308.88 K) | 13.64 K decrease (325 to 312.34 K) | Greater temperature drop in counterflow indicates better heat transfer. |
Temperature Rise (Cold Fluid) | 9.2 K increase (295 to 304.24 K) | 8.84 K increase (295 to 304.16 K) | Counterflow provides more effective heat gain for cold fluid. |
Thermal Enhancement Efficiency Trend | Decreases with increasing Re (0.77 at Re=1 to 0.168 at Re=60) | Decreases similarly (0.7 at Re=1 to 0.15 at Re=60) | Counterflow maintains slightly better efficiency across Reynolds numbers. |
Performance Index Trend | Decreases with increasing Re (33465.97 at Re=1 to 110.78 at Re=60) | Decreases similarly (30908.57 at Re=1 to 101.98 at Re=60) | Both types show reduced performance at higher flow rates, highlighting design trade-offs. |
Pumping Power | Increases with Re (0.0004 W at Re=1 to 1.5 W at Re=60) | Similar trend | Higher Re requires more pumping power, affecting energy efficiency considerations. |
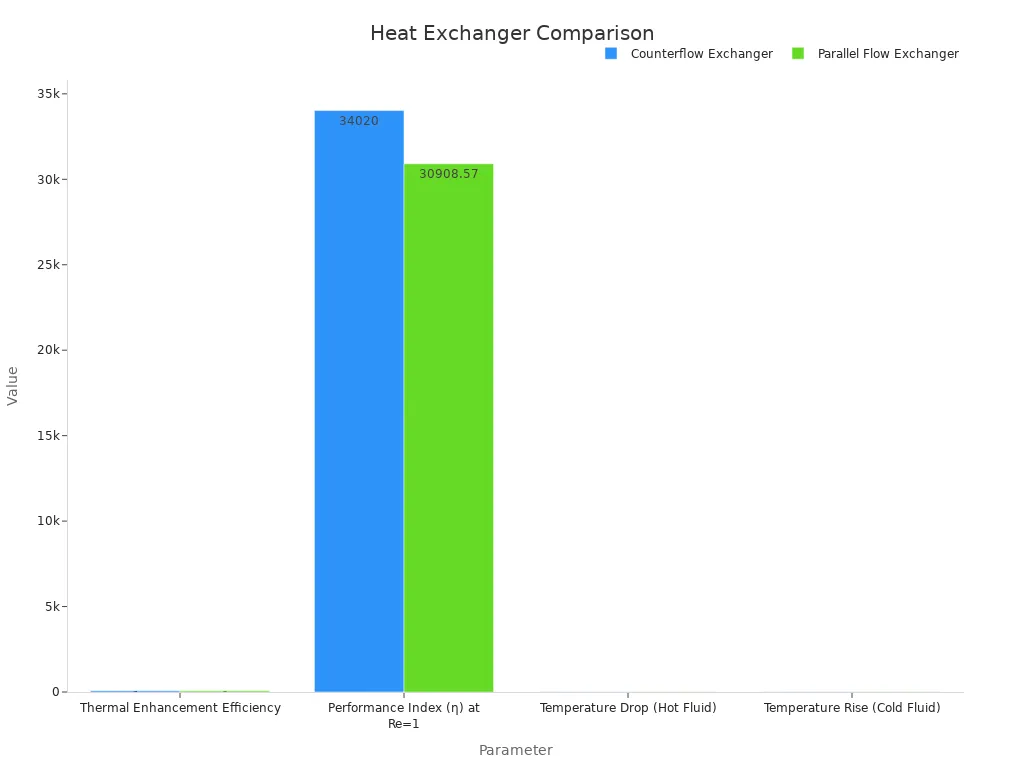
You should always match the heat exchanger type to your application, considering efficiency, cost, and operational requirements for the best results.
FAQ
What is the main purpose of a heat exchanger in a heating system?
You use a heat exchanger to transfer heat between two fluids without mixing them. This process improves energy efficiency and helps maintain precise temperature control in your heating system.
How do you choose the right heat exchanger for your application?
You should consider factors like required capacity, available space, fluid type, and operating pressure. Matching the heat exchanger type to your system’s needs ensures optimal performance and longevity.
How often should you maintain your heat exchanger?
You should inspect and clean your heat exchanger at least once every three months. Regular maintenance prevents fouling, improves efficiency, and extends the equipment’s service life.
What are the signs that your heat exchanger needs servicing?
You may notice reduced heat output, increased energy consumption, or unusual noises. Leaks, visible corrosion, or higher pressure drops also indicate that your heat exchanger requires immediate attention.
Can you use a plate heat exchanger for both heating and cooling?
Yes, you can use plate heat exchangers for both heating and cooling applications. Their design allows efficient heat transfer in either direction, making them versatile for many HVAC and industrial systems.
What materials work best for heat exchangers in corrosive environments?
You should select materials like stainless steel, titanium, or specialized alloys. These materials resist corrosion and ensure reliable operation when handling aggressive or corrosive fluids.
Do flow arrangements affect heat exchanger efficiency?
Yes. Counter flow arrangements usually provide the highest efficiency. Parallel and cross flow designs offer benefits for specific applications, but you should always match the flow pattern to your system’s requirements.