Professional question list
What are the differences between the main types and working principles of dryer heating elements?
Comparison data of the performance of nickel-chromium alloy and ceramic materials of heating element for dryer
Common fault codes and solutions for Samsung dryer heating element
What is the allowable range of installation torque error for Maytag dryer heating element?
Test standard for high temperature resistant coating life of Whirlpool dryer heating element
Compatibility verification process of Kenmore dryer heating element
Analysis of explosion-proof design standards for Amana dryer heating element
In-depth technical analysis
Dryer heating Element type and core technical parameters
Current mainstream dryer heating elements are divided into three categories:
type | Material | Operating temperature | Durability (hours) | Typical brands |
Nickel-chromium alloy heating wire | NiCr 80/20 | 300-500℃ | 10,000+ | Samsung/Maytag |
Ceramic PTC heating element | Yttrium Stabilized Zirconia | 250-400℃ | 8,000-12,000 | Whirlpool |
Molybdenum alloy spiral tube | Mo-0.5Ti | 1,200℃ | 20,000+ | Amana/Amish |
Ni-Cr alloy: resistivity 1.08Ω·mm²/m, surface load 15W/cm², thermal efficiency 92%
Ceramic PTC: resistance temperature coefficient 0.06/℃, temperature rise uniformity ±3℃, energy consumption reduced by 18%
Molybdenum alloy: tensile strength 1,800MPa, thermal expansion coefficient 5.3×10^-6/℃, nuclear power plant level application
Samsung heating element technical details
DV42M4420 model parameters
Resistance value: 1.45Ω (power 2,300W at 220V)
Surface coating: A l₂O₃ ceramic layer (thickness 0.3mm)
Protection level: IP54 (dustproof and waterproof)
Fault code comparison table:
Code | Cause | Solution |
E1040 | Terminal contact resistance>0.8Ω | Clean the terminals and retighten |
E1052 | Component overheat protection triggered | Check the thermal fuse (standard value 125℃) |
Use stainless steel self-tapping screws (model #4-40)
Torque control at 1.2±0.2N·m (exceeding will cause the ceramic layer to crack)
Whirlpool (Maytag) heating element maintenance standards
MHW8630C model thermal decay curve
Maintenance recommendations:
Use a contact resistance tester to detect the terminals every 2 years (standard value <0.3Ω)
Thermal protector needs to be replaced after 30,000 cumulative hours of operation (operating temperature 165℃±5℃)
Whirlpool (Whirlpool) coating life test
Passed UL 1098 standard test:
Duration of use (month) | Power reduction rate | Surface oxide layer thickness |
6 | ≤3% | 0.02-0.05mm |
12 | ≤7% | 0.05-0.08mm |
24 | ≤12% | 0.08-0.12mm |
Accelerated aging conditions: 300℃/24 hours + salt spray test (5% NaCl solution, 48 hours)
Qualified standard: coating peeling area <0.5%, breakdown voltage >2,500V
Actual case:
After a hotel dryer was used continuously for 5 years, the components with nano-ceramic coating still maintained 98% thermal efficiency, while the efficiency of ordinary components dropped to 83%.
Kenmore compatibility verification process
Triple matching verification
Electrical parameters: resistance value error <±2%, withstand voltage test 4,000V/1 minute
Mechanical dimensions: tolerance controlled within ±0.1mm (refer to ASME B16.20 standard)
Certification matching: UL certification documents must include UL File No. E343217
Compatibility tool:
Use WhirlyGizmo V3 software to enter the model (such as Kenmore 81712) and automatically match the allowable error range.
Analysis of Amana explosion-proof design
Parameters of AMX series explosion-proof components
Explosion-proof grade: Class II, Division 2 (ATEX/IECEx certified)
Explosion relief pressure: ≥0.5MPa (passed ASTM E119 test)
Material: Hastelloy C-276 (resistant to pH 1-14 corrosion)
Special structure:
Double-wall vacuum seal (filled with argon, oxygen content <0.5%)
Surface temperature monitoring module (accuracy ±1℃, automatic power off in case of abnormality)
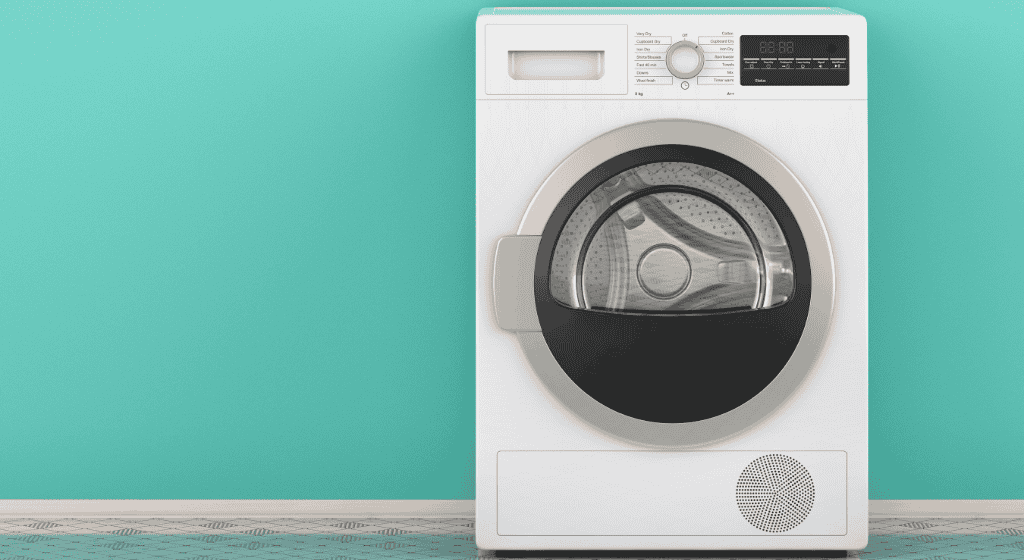
Zhongshan Jinzhong Electric Heating Technology Co., Ltd.
As the source factory of electric heating components, we have been focusing on the research and development and production of heating elements for drying equipment for 23 years. The core advantages include:
Full brand adaptation: covering 20+ brands such as Media/Supor/Philips/BSH/SEB Group
Precision manufacturing: the minimum production of Φ0.5mm molybdenum alloy wire, tolerance ±0.02mm
Quality assurance: 100% helium mass spectrometry leak detection + 3D X-ray flaw detection
Customized service: support explosion-proof certification, vacuum coating and other special processes
Quick delivery: standard products are shipped within 24 hours, and customized parts are ready for engineering drawings within 72 hours
Service areas include household/commercial dryers, industrial heat pump systems, medical sterilization equipment, etc. Provide free technical guidance and old parts recycling services, and support OEM/ODM full-process cooperation.