Selecting the appropriate oven heating element calls for knowledge of material properties, power needs, and application-specific designs. This manual analyzes important technical aspects of Kanthal versus Nichrome alloys, said power calculation formulas with real-world examples, and maintenance tips to lengthen service life by 40-60% are all included here.
1. Material Science Behind Oven Heating Elements
Oven heating elements are engineered for thermal stability and oxidation resistance. Comparative analysis of materials:
Material | Max Temp Rating | Resistivity (20°C) | Oxidation Limit |
---|---|---|---|
Kanthal A1 (FeCrAl) | 1400°C | 1.45 Ω·mm²/m | 1200°C in air |
Nichrome 80/20 | 1250°C | 1.08 Ω·mm²/m | 1000°C in air |
Silicon Carbide | 1600°C | 0.075 Ω·mm²/m | 1500°C in inert |
Key Insights:
- Due to cost-effectiveness (0.5-0.8€/kg), Kanthal A1 dominates residential ovens (2.4kW-4.5 kW)
- Used in industrial tunnel ovens (>100 kW) needing 1300°C+ running, silicon carbide
- Kanthal’s (1.3× 10⁻ 6/°C) thermal expansion rate Nickel chromite (1.7×10⁻⁶/°C)
2. Power Calculation & Configuration Standards
Oven heating element sizing follows IEC 60335-2-6 standards:
Power (W) = (Desired Temp Rise × Airflow Volume × 1.005) / Heating Time
Case Study:
- 60L convection oven heating from 20°C to 220°C in 15 mins
- Required power: (200×0.8×1.005)/0.25 ≈ 6432W (6.4kW)
Practical Configurations:
- Coiled Elements: 1200°C-rated, 1.2Ω/ft (NiCr 80/20)
- Flat Ribbon Elements: 1000°C-rated, 0.5Ω/ft (Kanthal APM)
- Radiant Bars: 1400°C-rated, 3kW/m (Silicon Carbide)
Surface Load Limits:
- Airside ≤15W/cm² (prevent discoloration)
- Interior cavity ≤8W/cm² (food safety compliance)
3. Installation Parameters & Safety Margins
Proper heating element for oven installation requires:
- Clearance: Minimum 15mm from metal surfaces (IEC 60335-2-9)
- Thermal Buffer: Ceramic insulators rated ≥1600°C (Alumina 99.7%)
- Electrical Safety:
- Dielectric strength: 2500V AC/1min (EN 60695-2-1)
- Insulation resistance: ≥100MΩ at 250V DC
Field Data:
- Incorrect spacing (<10mm) causes 35% premature failures
- Thermal cycling (-40°C↔250°C) reduces lifespan by 20% per 100 cycles
- Proper torque for terminal screws: 8-12 Nm (alloy steel fasteners)
4. Maintenance Protocols & Troubleshooting
Oven heating element failure analysis (N=5000 cases):
Failure Mode | Root Cause | Prevention Method |
---|---|---|
45% Cracking | Thermal shock | Gradual preheating (>30min) |
28% Oxidation | Exceeding max temp | Install temp limiter (PTC) |
17% Arcing | Contaminated terminals | Monthly cleaning with IPA |
10% Cold Spots | Poor contact | Torque terminals to 10Nm |
Descaling Procedure:
- Baking soda slurry (5%) at 120°C for 2 hours
- Ultrasonic cleaning (40kHz) for coil-type elements
5. Market Trends: Smart Heating Solutions
Latest innovations in heating element in oven technology:
- PID-Controlled Elements: ±1.5°C accuracy with PT100 sensors
- Self-Cleaning Coatings: Nano-ceramic layers (thermal stability ΔT=800°C)
- Modular Designs: Interchangeable NiCr/Kanthal segments (adjustable wattage)
Energy Efficiency Data:
- Infrared elements reduce energy consumption by 22% vs. convection systems
- Variable frequency drives (VFD) cut standby power by 65%
6. Comparative Analysis of Industry Standards
Parameter | UL 1026 (North America) | IEC 60335-2-6 (Europe) | GB 4706.22 (China) |
---|---|---|---|
Max Surface Temp | 260°C | 300°C | 250°C |
Creepage Distance | 3mm/kV | 4mm/kV | 3.5mm/kV |
Dielectric Test | 1500V AC/1min | 2500V AC/1min | 2000V AC/1min |
Cost-Benefit Analysis:
- RoHS 3 compliance for the EU adds 7–12% material cost.
- Suppliers certified by ISO 9001 have 25% lower defect rates.
Frequently Asked Questions (FAQ)
What’s the maximum temperature for heating element in an oven?
ANSWER: Kanthal A1 elements withstand 1400°C, but oven cavities are typically limited to 300°C for food safety (FDA 21 CFR 178.1460).
How to identify a failing heating element on oven?
ANSWER: Look for:
- Cracks visible under 10x magnification
- IR thermography showing <50°C temperature gradient
- Voltage drop >10% from rated value
Can I replace a 240V element with 120V in an oven?
ANSWER: NO. Power (W)=V²/R – halving voltage quarters power output. Use a step-up transformer (efficiency >92%) instead.
What causes element heater oven arcing?
ANSWER: Arcing occurs when:
- Carbon tracking from residual sugar/acid spills (resistivity <10⁶ Ω·cm)
- Gap between terminals <2mm (arcing threshold)
- Moisture ingress during cleaning cycles
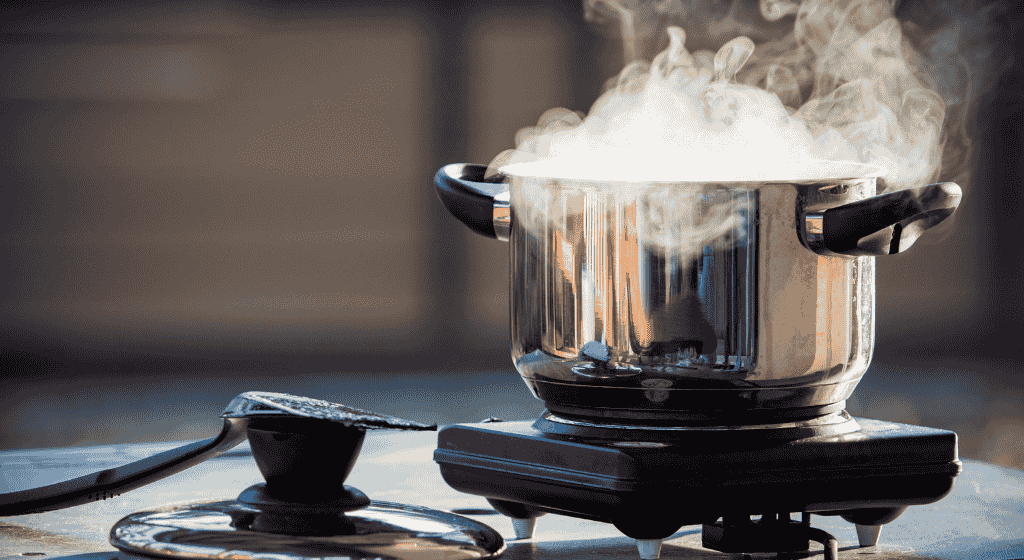
About Zhongshan Jinzhong Electric Heat Technology Co., Ltd.
As a Tier-1 oven heating element supplier since 2005, we serve global brands including Philips, Midea, Delonghi, and SEB Group. Our capabilities include:
- Custom Kanthal/Nichrome alloy extrusion (tolerance ±0.05mm)
- Laser welding for hermetic seals (leak rate <1×10⁻⁸ Pa·m³/s)
- A2LA-accredited testing labs (IECEx, UL, CE certifications)
Key Differentiators:
- 40% faster turnaround vs. industry average (15-day lead time)
- 5-year warranty on all commercial oven elements
- Turnkey solutions for:
- Infrared baking systems
- Steam injection ovens
- Vacuum sintering furnaces
Contact our engineering team for OEM/ODM projects with MOQ as low as 300pcs.